Conveyor idlers are integral components in the bulk material handling industry, providing essential support and guidance for conveyor belts transporting materials across various distances. When selecting and maintaining these crucial elements, it's necessary to rely on a combination of firsthand experience, specialized knowledge, and authoritative insights to ensure optimal performance and longevity.
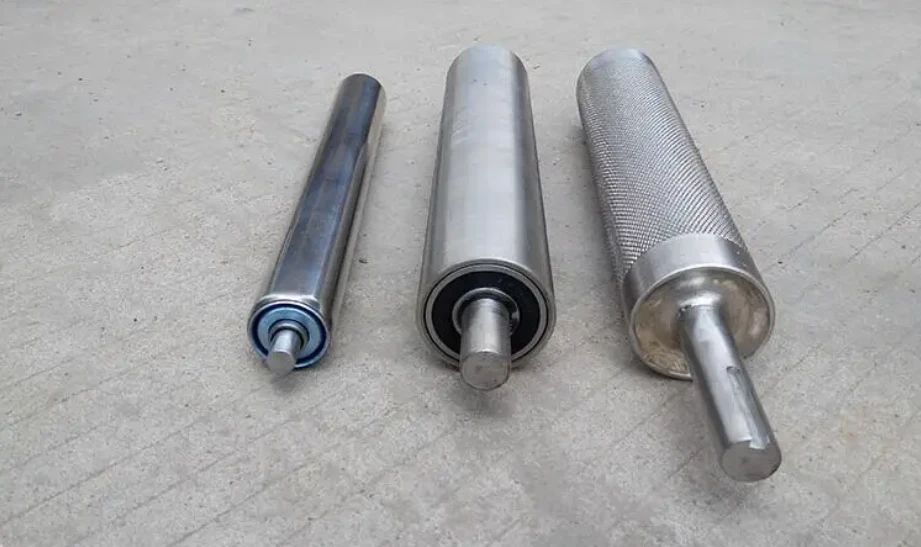
Understanding the nuances of conveyor idlers begins with recognizing their distinct roles within conveyor systems. Typically made up of a roller, frame, and seal, idlers serve as the pivotal support structure for the conveyor belt, evenly distributing the weight of the conveyed material. They come in different types—such as carrying idlers, return idlers, impact idlers, and training idlers—each designed for specific functions within the conveyor system.
One significant aspect to consider when assessing conveyor idler performance is the material composition. Experience has shown that materials like high-density polyethylene (HDPE) and rubber-coated rollers offer advantages in reducing noise pollution, corrosion resistance, and extending the overall lifespan of the idlers. Investing in high-quality materials not only curtails maintenance costs but also enhances the conveyor system's reliability.
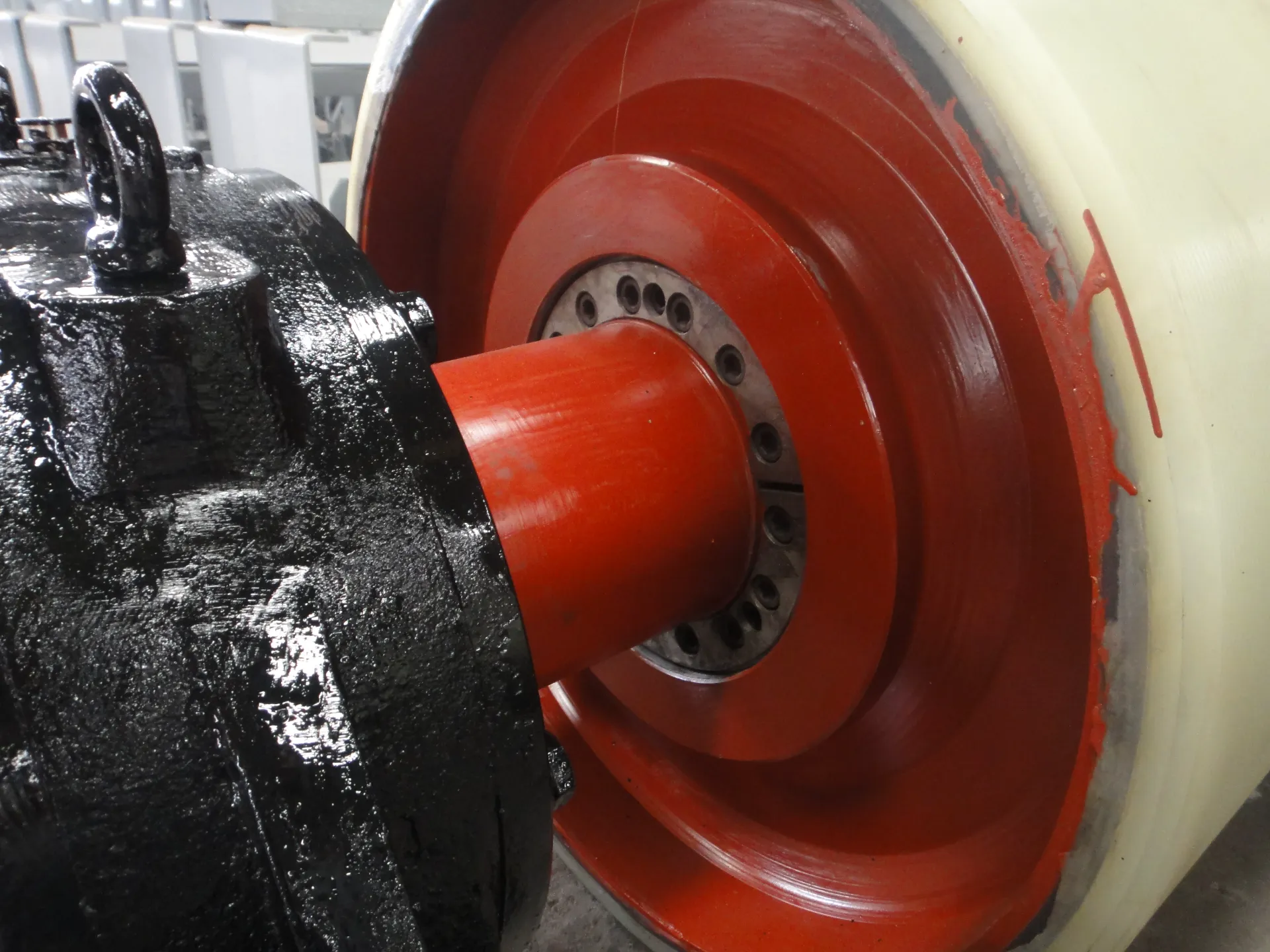
From a technical standpoint, correct idler alignment cannot be overstated. Misalignment leads to uneven belt wear, increased energy consumption, and potential downtime. Best practices suggest regular inspections and utilizing advanced alignment tools, such as laser systems, to ensure precise idler alignment.
For conveyor systems operating in harsh conditions, self-aligning idlers are recommended. These idlers automatically adjust to belt misalignment, guaranteeing smoother operations.
The significance of seal technology in conveyor idlers reflects the industry's shift towards prolonged equipment life and minimal maintenance interventions. Understanding the importance of effective sealing in keeping contaminants like dust and moisture out is critical. Labyrinth seals, which are known for their superior protection capabilities, have become the industry standard.
conveyor idlers
Authoritative insights from industry leaders underscore the value of continuous innovation in idler design to meet evolving industry demands. Incorporating sensors and IoT technology in modern conveyor idlers promises a future of predictive maintenance and real-time monitoring capabilities. The deployment of smart idlers with integrated sensors provides data analytics for proactive maintenance measures, drastically minimizing unexpected failures.
Trust in the selection of conveyor idlers comes from relying on reputable manufacturers with a proven track record of producing high-quality components. An industry-best practice is to choose suppliers with certifications that adhere to strict international standards, ensuring that the idlers meet rigorous quality and safety benchmarks.
Do not underestimate the role of expertise in installation and maintenance practices. Adequate training for personnel involved in the handling of conveyor systems ensures that idlers function effectively. Providing regular training sessions and updates about technological advancements in conveyor systems ensures that teams are well-equipped to manage and mitigate any operational challenges.
Ultimately, the strategic approach to managing conveyor idlers lies in combining robust design elements, top-tier materials, and advanced technological integrations. These result in a system that not only performs efficiently today but also remains adaptable for future technological trends and demands. Balancing these factors with authoritative and trustworthy insights fortifies the position of conveyor systems as an indispensable element in the realm of bulk material handling, steering their evolution towards a more reliable and sustainable future.