Wing pulley lagging plays a crucial role in the world of conveyor systems, directly impacting efficiency, longevity, and performance. Understanding the intricacies of this component can significantly enhance the operational effectiveness of a conveyor system. As industries continue to push for optimized productivity, the expertise in selecting and maintaining wing pulley lagging becomes indispensable.
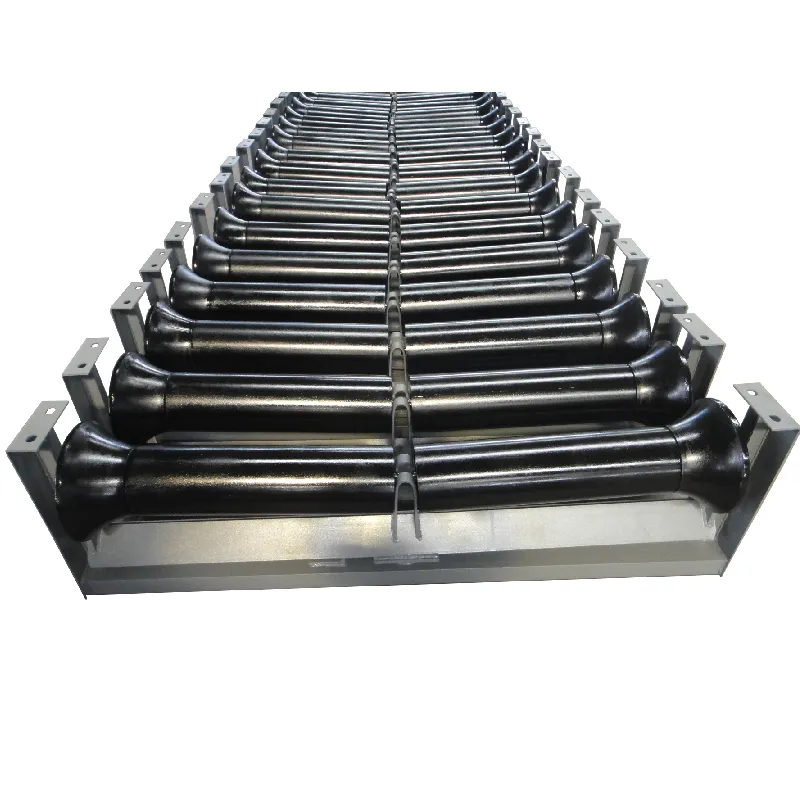
In the dynamic sector of material handling, conveyor belts are lifelines, ensuring the seamless movement of goods. Integral to this process, wing pulleys help in deflecting debris and minimizing wear on belts, thus extending their life. The right lagging material selection further enhances these benefits. Professionals recommend rubber lagging due to its shock-absorbing properties, while ceramic lagging is favored for its high resistance to abrasive materials. Each industry requires a tailored approach, and understanding the environment in which a pulley operates is essential for optimal lagging application.
Expertise in wing pulley lagging also involves understanding different lagging techniques, such as cold vulcanizing, hot vulcanizing, and strip lagging. Cold vulcanizing allows for quicker application without heat, ideal for on-site repairs. Hot vulcanizing, though more time-consuming, offers a stronger bond, ensuring durability under extreme conditions. Strip lagging is useful for easy-replaceable sections, enhancing maintenance capabilities. Each method carries specific advantages, and selecting the appropriate one requires a nuanced understanding of the operational demands and environmental factors.
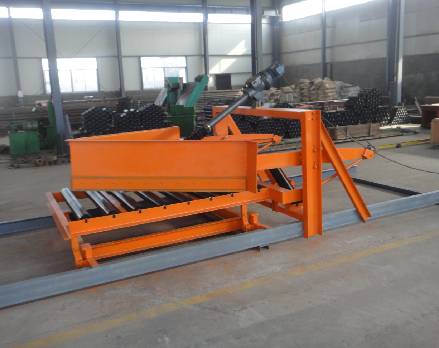
Real-world applications showcase the versatility and necessity of proper pulley lagging. In the mining industry, for instance, ceramic lagging is often employed to combat the constant abrasion from heavy ore loads. The agricultural sector, dealing with moisture-laden materials, might opt for rubber lagging to prevent slippage and ensure uninterrupted conveyance. Customized lagging solutions cater to these varied needs, emphasizing the industry's reliance on tailored expertise.
wing pulley lagging
Authority in the industry is established through consistent performance and innovation. Manufacturers of wing pulley lagging continuously research and develop materials that offer improved performance metrics. The introduction of hybrid materials, combining the resilience of rubber with the hardness of ceramics, reflects this ongoing innovation. Companies that lead in this niche not only provide quality products but also educate and train their partners in installation and maintenance, cementing their reputation as trusted sources of industrial solutions.
Trustworthiness stems from proven reliability and a commitment to quality. Comprehensive testing under simulated operational conditions ensures that the lagging materials meet stringent industry standards. This reliability is crucial, as the failure of conveyor components can lead to significant downtime and economic loss. Trusted providers of wing pulley lagging offer warranties and create enduring relationships with their clients, focusing on long-term operational success rather than short-term gains.
With the advent of smart technology, the future of wing pulley lagging looks promising. Incorporating sensors and remote monitoring systems can offer real-time data on lagging wear and tear, enabling predictive maintenance and reducing unexpected breakdowns. This marriage of traditional mechanical components with modern technology represents the cutting edge of conveyor system efficiency.
In summary, wing pulley lagging is far more than a protective layer on a conveyor pulley; it's a crucial component that demands informed choice and expertise for optimal performance. Industry professionals understand that the right lagging can significantly enhance conveyor system efficiencies, reduce downtime, and save costs. The continuous innovation and reliability offered by leading manufacturers ensure that wing pulley lagging remains a vital aspect of material handling across various sectors. Understanding and investing in the right lagging solutions is a testament to a company’s commitment to excellence in operational management and reflects a broader trend towards intelligent, sustainable industrial practices.