In the realm of material handling and transportation systems, conveyor belts serve as a backbone for moving products efficiently across various industries. A crucial component of these systems is the pulley, which helps direct the belt and transmit power. Understanding the different types of pulleys used in conveyor belt systems can significantly enhance operational efficiency and reliability. This article delves into the various types of pulleys utilized in conveyor belts, offering insights into their distinct functions and advantages.
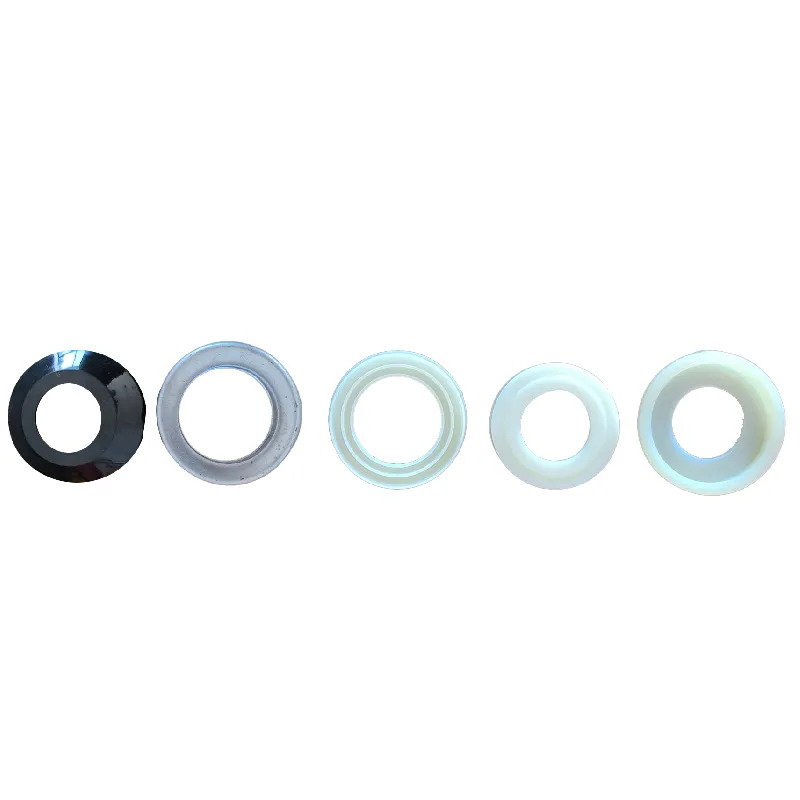
The first type commonly encountered is the Drive Pulley. Positioned at the discharge end of the conveyor, drive pulleys are typically motorized and responsible for propelling the belt. These pulleys are fabricated from robust materials like steel, which ensures durability and supports heavy load capacities. The drive pulley often features a crowned face or lagging—materials like ceramic or rubber that are bonded to its surface. Lagging increases the traction between the belt and pulley, preventing slippage and ensuring smooth movement, even under demanding conditions.
Next, we explore the Return Pulley, also known as the tail pulley. Installed at the tail end of the conveyor system, this pulley facilitates the redirection of the belt back towards the drive pulley. Its primary function is to provide tension to the belt and ensure its alignment. Return pulleys are simpler in design compared to drive pulleys, often lacking motorization. However, they play a pivotal role in maintaining optimal belt tension and preventing sagging, which can lead to operational inefficiencies.
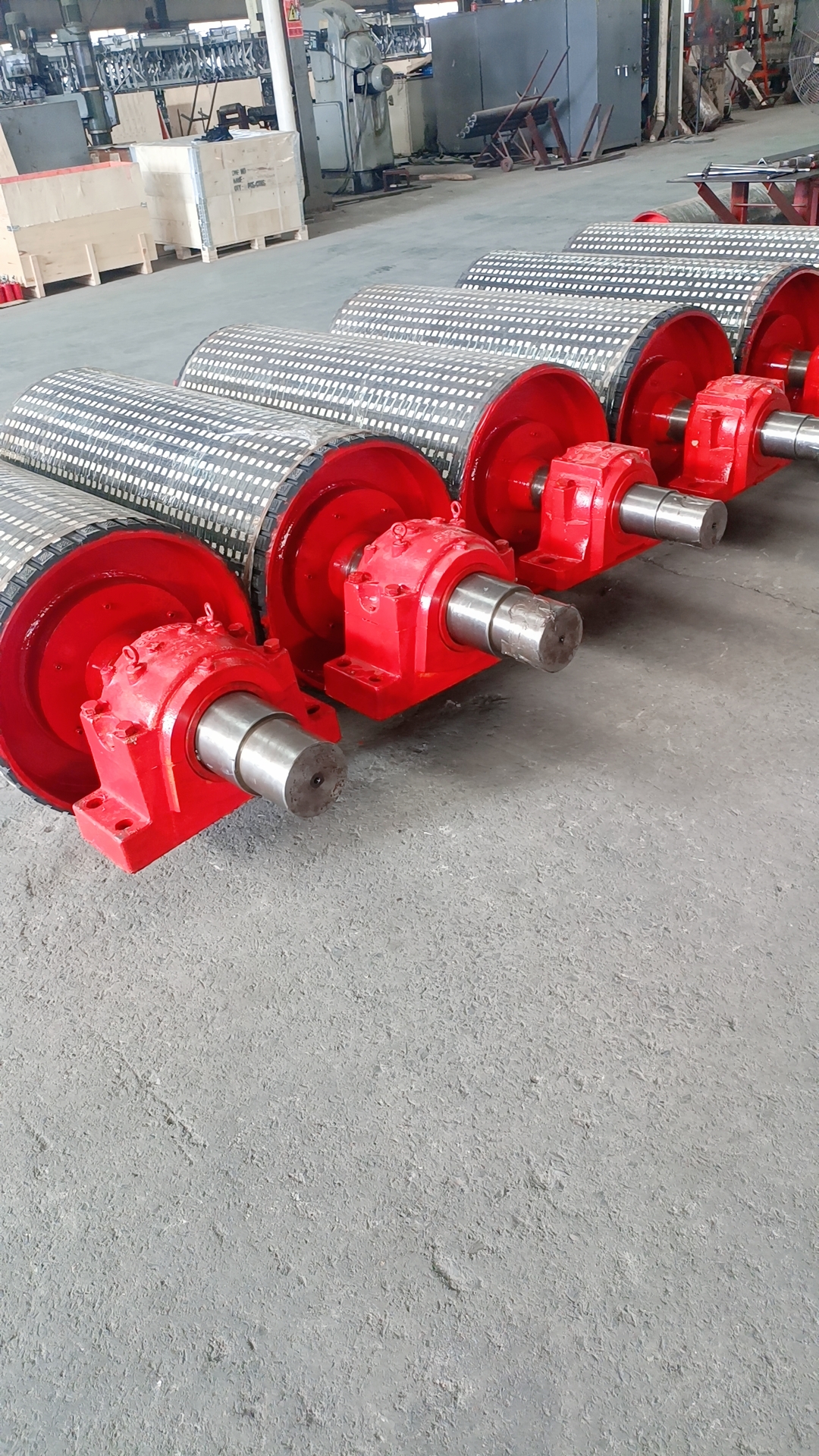
An integral type often paired with return pulleys is the Snub Pulley. Positioned close to the drive pulley, snub pulleys enhance the belt's contact angle with the drive pulley. This increased wrap angle results in improved friction between the belt and drive pulley, which is essential for preventing slippage. Snub pulleys are crucial for tackling heavy-duty applications and are especially beneficial in conveying systems transporting bulky materials.
A specialized variant is the Bend Pulley. These pulleys are employed to alter the belt's direction by an angle of 180 degrees. Located near the tail end or along any point in the belt where a direction change is necessary, bend pulleys manage the flow continuity by guiding the belt smoothly around corners. They share design characteristics with tail pulleys but are distinguished by their strategic placement to facilitate smooth directional changes.
types of pulley in conveyor belt
The Take-Up Pulley is another critical variety in conveyor belt systems. This type is central to maintaining optimal belt tension, an essential factor for system stability. Generally, take-up pulleys are mounted on movable frameworks, allowing them to be adjusted to maintain appropriate tension levels as the belt expands and contracts due to operational stress and temperature changes. By ensuring consistent tension, take-up pulleys help prevent belt slippage and premature wear.
Lastly, we examine the Wing Pulley, designed with a series of evenly-spaced, wing-shaped projections along its circumference. These pulleys perform exceptionally well in environments prone to debris and material build-up between the pulley and the belt. The wing design minimizes material accumulation by allowing loose debris to fall away, thus avoiding belt misalignment and reducing maintenance demands. Wing pulleys are ideal for applications in construction and mining where exposure to granular materials is constant.
In conclusion, selecting the appropriate pulley type is critical to the efficiency and longevity of conveyor belt systems. While each pulley type serves a unique function, they collectively contribute to the seamless operation of conveying tasks across industries. From enhancing traction to ensuring proper belt alignment and tension, these pulleys play indispensable roles. For businesses striving to optimize their material handling operations, investing in quality pulley systems tailored to their specific needs can yield significant performance benefits, ensuring reliability and operational excellence.
When planning to upgrade or install a new conveyor system, consulting with experienced professionals and conducting a thorough analysis of operational demands are crucial. By understanding the unique characteristics and applications of each pulley type, businesses can better equip their systems to meet both current and future challenges, ensuring smooth and efficient material transportation.