Pulley systems in conveyors play an integral role in the efficient and seamless movement of materials across various industrial applications. For those seeking to delve into the complexities and derived benefits of utilizing different types of pulleys, understanding their functions and design differentiations is paramount. Below, we explore the distinct types of pulleys used in conveyor systems, emphasizing real-world applications, expertise-backed insights, and principles that ensure reliability and effectiveness.
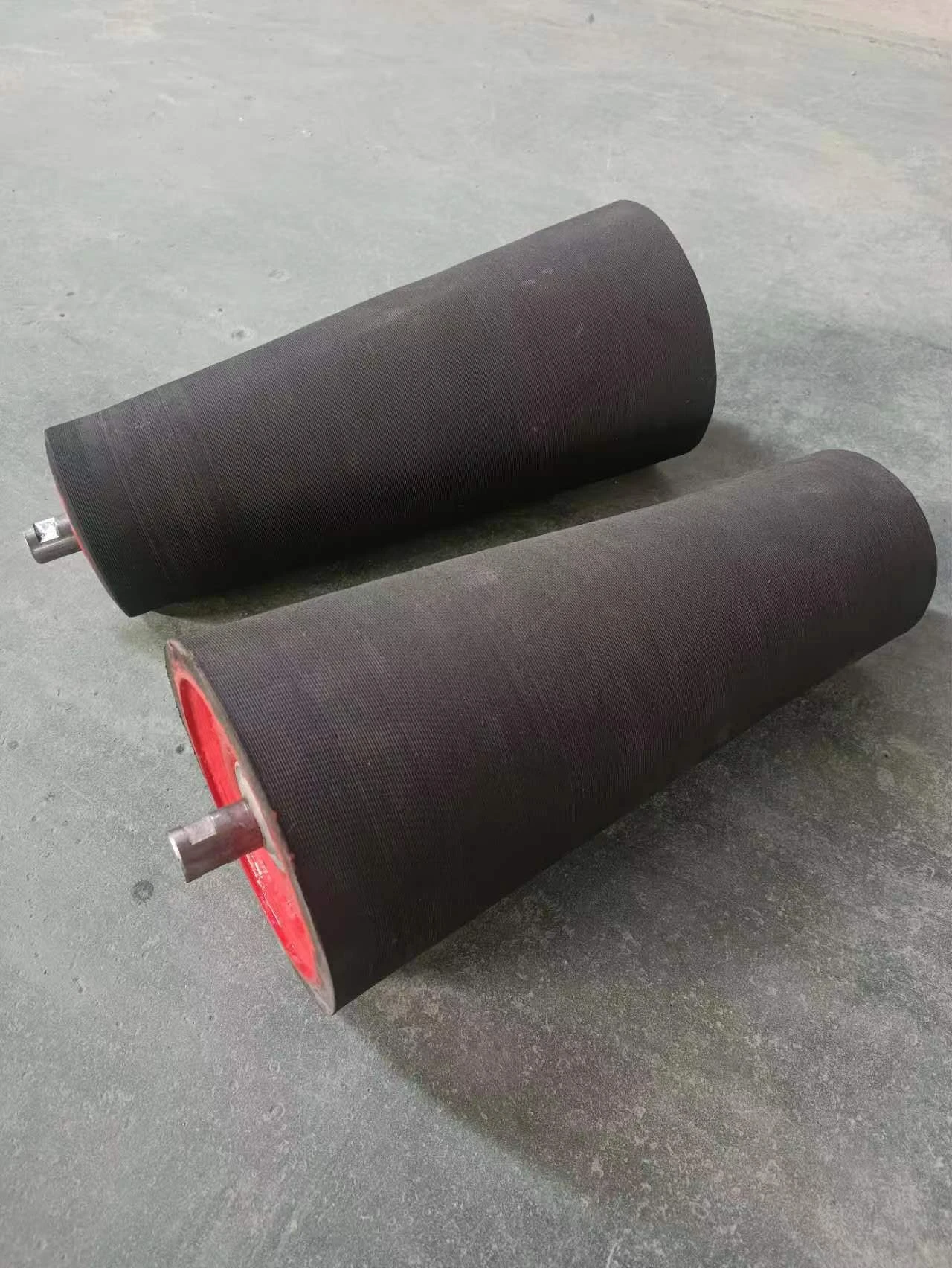
1. Drive Pulley As the main force behind conveyor movement, the drive pulley is powered by an external motor. It's engineered to efficiently transfer energy to the belt, initiating the movement. With its robust design, often constructed from high-strength materials like steel, the drive pulley is an embodiment of power and precision. Choosing an appropriate drive pulley dictates the speed and load-capacity thresholds, thereby playing a critical role in the overall productivity of the conveyor system.
2. Tail Pulley Positioned at the opposite end of the conveyor from the drive pulley, the tail pulley serves to guide and tension the belt, maintaining a steady and consistent path. Its vital function in adjusting the belt tension is crucial for preventing slippage and ensuring the smooth operation of the conveyor. Tail pulleys can be enhanced with removable lagging, providing flexibility and extended service life.
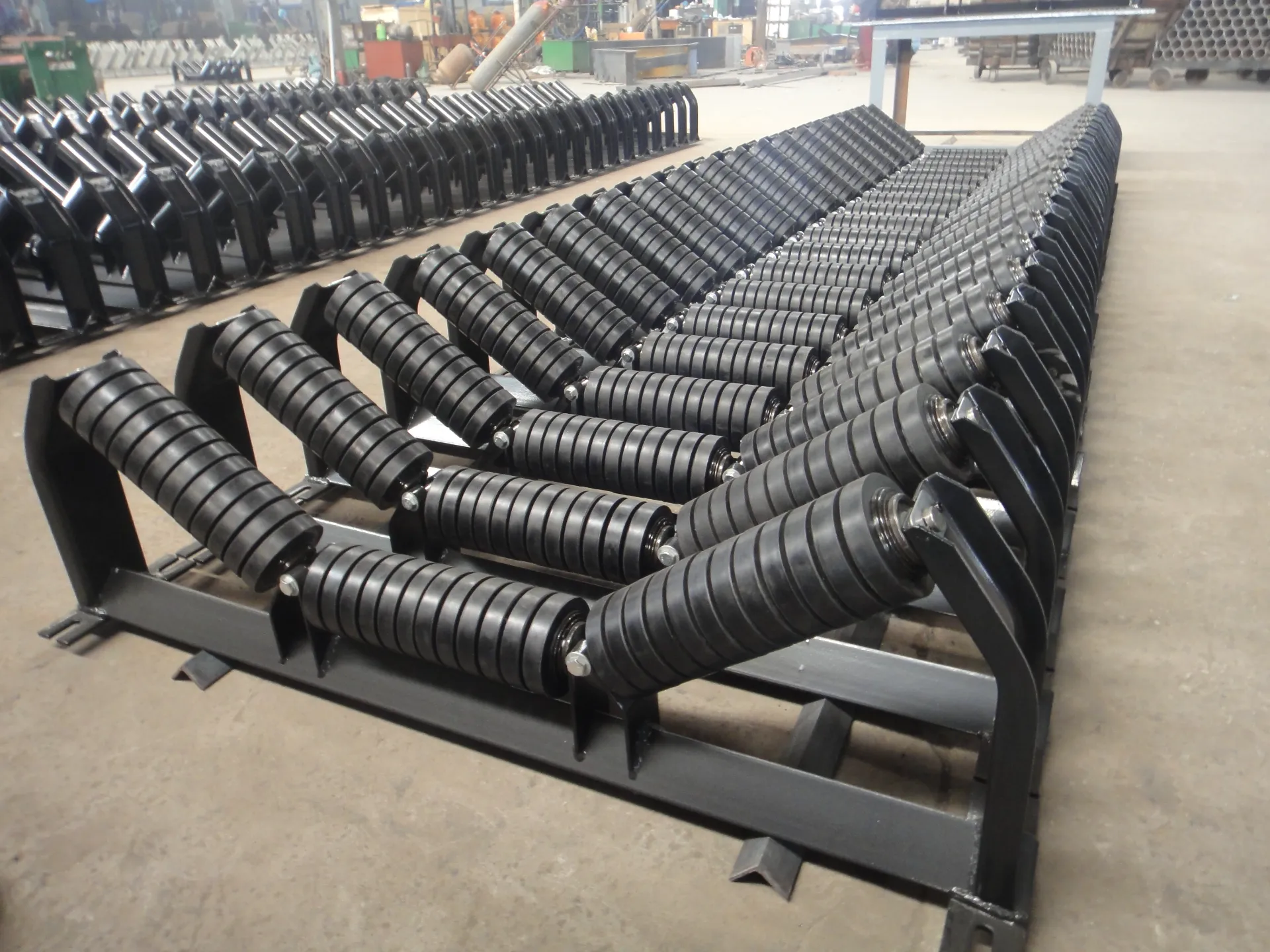
3. Snub Pulley Used primarily to increase the angle of wrap of the belt on the drive pulley, the snub pulley amplifies the friction, thus maintaining a stable grip on the conveyor belt. Strategically positioned, it optimizes the traction provided by the drive pulley. This component is indispensable in operations demanding high tension and torque, articulating the balance between physical dynamics and material handling efficiency.
4. Take-Up Pulley Essential for maintaining optimal belt tension, the take-up pulley is adjusted automatically or manually as per the conveyor system's length and operational load. This pulley ensures the belt remains taut, augmenting the system's efficiency and longevity by minimizing wear and mitigating potential operational downtime.
types of pulley in conveyor
5. Bend Pulley Utilized to change the direction of the conveyor belt or assist the belt's transition between different planes or material handling environments, the bend pulley is pivotal in system customization and flexibility.
Expertise in the angle and material of the bend pulley can dramatically influence the conveyor's capability to adapt to unique operational parameters.
6. Impact Pulley Positioned near loading points, the impact pulley's primary function is to absorb the shock of material loading, thereby reducing belt wear and enhancing longevity. Its intricate design, often involving reinforced buffers, addresses concerns related to impact damage and extends the service life of the conveyor components.
Effective pulley selection and integration within conveyor systems hinge on a nuanced understanding of operational demands and environmental conditions. Proper distribution of radial loads, coupled with professional installation, ensures that each pulley type operates within its design parameters, cementing the conveyor's reputation for reliability and robustness.
Empirical insights from industries like mining, manufacturing, and logistics underscore the significance of each pulley type. Not only does this knowledge enable the fine-tuning of existing systems, but it also assists in the design of new, application-specific solutions. The evolution of pulley systems embodies technological progression, with advancements promising increased efficiency, durability, and user-satisfaction.
In conclusion, selecting the appropriate type of pulley for specific conveyor applications relies on a blend of design expertise, hands-on experience, and a commitment to quality and reliability. The right pulleys, integrated thoughtfully into conveyor systems, yield tangible improvements in performance, ushering industries into new frontiers of operational excellence.