Pulley systems in conveyor applications are fundamental components that significantly impact performance and efficiency in material handling processes. These pulleys, often overshadowed by other conveyor elements, vary in design, material, and application, each serving distinct purposes within a conveyor system. Understanding these types of pulleys offers a clear edge in optimizing conveyor system operations and ensuring industry-specific solutions.
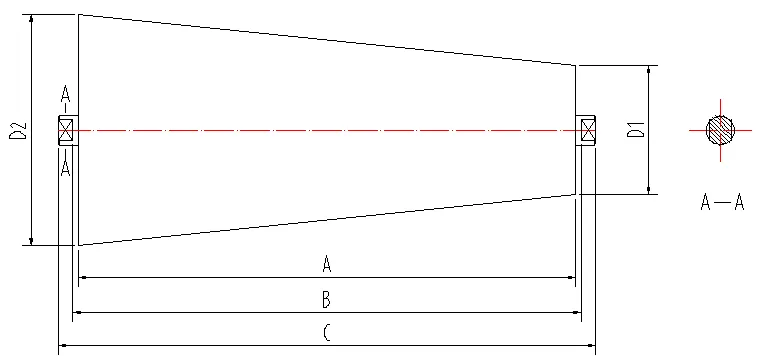
The most basic and widely used type of pulley in conveyor systems is the drive pulley. It plays a pivotal role as it connects to the motor, providing the necessary traction for the belt conveyor to move. Typically, the drive pulley is located at the head of the conveyor and is often larger in diameter compared to other pulleys. This design ensures a higher torque transmission, facilitating the movement of heavy loads over long distances. Materials used for drive pulleys usually include steel or aluminum, lending them robustness to endure the constant rotation and pressure.
Another crucial type is the idler pulley, which serves to support the weight of the conveyor belt and its carried load, maintaining belt tension and minimizing sag. Unlike the drive pulley, the idler pulley is not connected to the motor but rotates freely, ensuring smooth belt motion and alignment. Idler pulleys come in various forms, including flat, v-groove, and flanged, each specifically tailored to handle different belt orientations and load capacities.
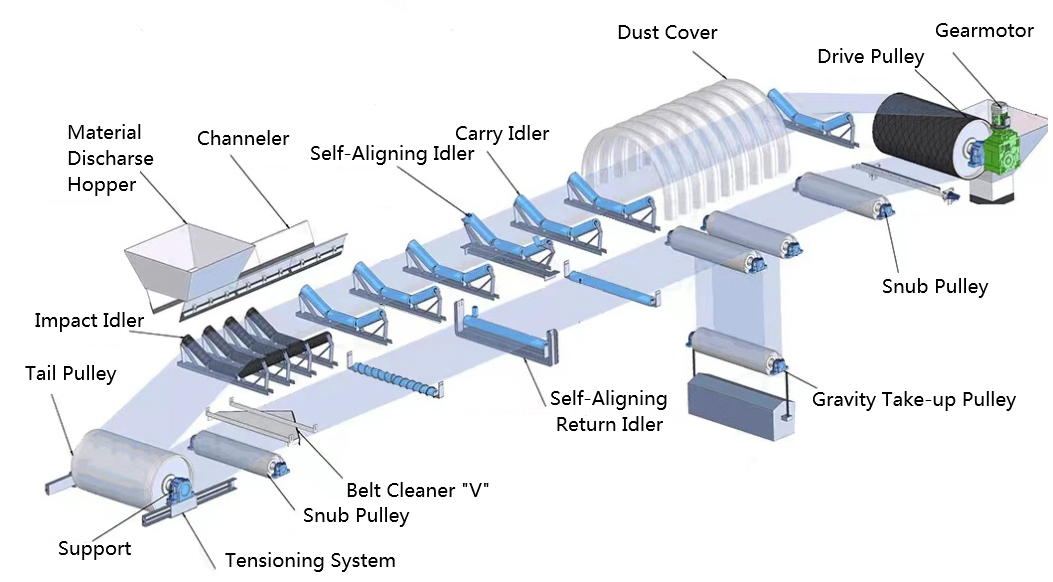
An essential counterpart to the idler pulley is the snub pulley. Its primary function is to increase the contact between the conveyor belt and drive pulley, enhancing friction and improving belt traction. Positioned at a critical angle close to the drive pulley, the snub pulley aids in achieving optimal belt tension, reducing slippage, and enhancing the overall efficiency of the conveyor system. High-friction materials are often used for snub pulleys to maximize their grip on the belt surface.
The take-up pulley is designed to maintain proper belt tension throughout the operation of the conveyor. Situated within a frame that allows it to move in a controlled manner, this pulley adjusts to changes in belt length due to stretching or load fluctuations. Proper tension is critical to prevent belt slippage and sagging, thereby reducing wear and tear on the belt and prolonging its service life. Take-up systems can be either automatic or manually adjusted, depending on the requirements of the conveyor operation.
types of pulley in conveyor
Wing pulleys are a specialized type of pulley that feature a series of evenly spaced wings or fins protruding from their surface. These features help in self-cleaning by dislodging debris that may accumulate on the belt, particularly useful in settings with abrasive or sticky materials. Wing pulleys are typically used in the tail position of conveyors to prevent material buildup and minimize maintenance needs.
Finally, the bend pulley is used to change the direction of the conveyor belt or to create a loop with the belt. This pulley enhances the operational flexibility of conveyor systems, making it integral in more complex conveyor layouts where changes in belt routing are required.
Choosing the right type of pulley for a specific conveyor application involves understanding the materials being transported, the conveyor environment, and operational demands. This selection process requires technical know-how and industry experience to ensure that the system is not only effective but also economical and sustainable in the long run. Investing in high-quality pulleys from reputable manufacturers further bolsters system reliability and underscores the importance of using components conforming to industry standards.
In summary, the diversity of pulley types within conveyor systems underscores their pivotal roles, from driving and guiding the belt to maintaining its tension and ensuring cleanliness. Properly specified and maintained pulleys contribute to efficient, reliable, and safe material handling operations, making them indispensable components within the varied applications of conveyor technology.