In the world of industrial and logistical operations, belt conveyors are ubiquitous. A crucial component of these systems is the pulley, playing a significant role in the efficiency and functionality of conveyor operations.
Different types of pulleys are used depending on the specific requirements of the conveyor system. Understanding these variations not only enhances operational efficacy but also extends the lifespan of the machinery, ensuring maximal productivity and minimal downtime.
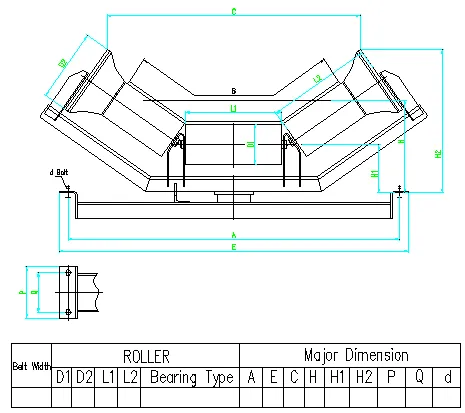
The drive pulley operates as the primary power source in a belt conveyor system, directly influenced by the motor. It determines the speed and direction of the conveyor belt. Typically, these pulleys are cylindrical and may feature lagging—a layer of material, often rubber, designed to increase traction between the pulley and the belt. In high-tension applications, ceramic lagging may be used due to its durability and ability to resist slippage even in adverse conditions like wet environments.
Slightly different in function is the idler pulley, which exists to support the tension in the belt and maintain its alignment without directly impacting its movement. These pulleys are generally less robust as they are not subjected to the same forces as drive pulleys. However, their design and placement are critical; an improperly aligned idler pulley can drastically reduce a belt’s lifespan by causing uneven wear.
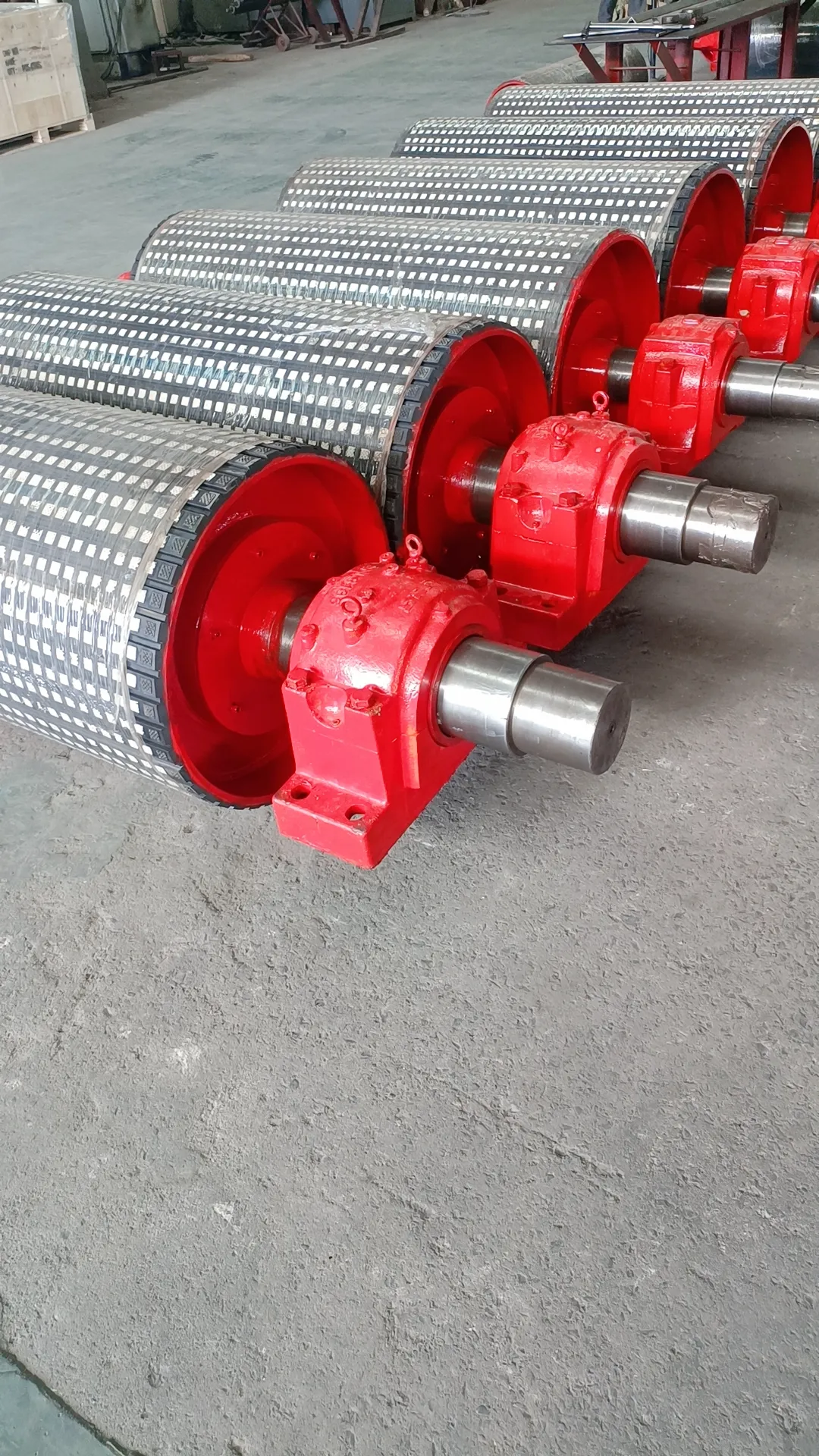
Snub pulleys, meanwhile, enhance the wrap angle of the belt on the drive pulley. By increasing the contact arc between the belt and the drive pulley, they provide additional grip. This is particularly useful in systems where more friction is needed to prevent belt slippage under load.
Tension pulleys are used to automatically adjust the tension in the conveyor belt as it expands and contracts due to temperature variations or load changes. These pulleys are often spring-loaded, maintaining a constant tension on the belt and accommodating dynamism within the system without manual intervention. This feature is essential for maintaining operational continuity and extending the life of the conveyor system by preventing excessive slack or tightness.
types of pulley in belt conveyor
Specialized applications may also require wing pulleys, which have a unique spoke-like structure. These are typically used in environments where material buildup is a problem. The design of the winged pulley allows loose material to fall away rather than becoming trapped between the pulley and the belt, thereby reducing wear and maintaining belt cleanliness.
Each type of pulley serves a distinct purpose and is optimized for specific operational conditions, underscoring the necessity for precise selection based on system needs. Choosing the right pulley configuration requires an understanding of the materials being transported, the environmental conditions, and the overall design of the conveyor system. An incorrect choice could lead to increased maintenance costs and unwanted interruptions in operations.
From an operational standpoint, expertise and authority in pulley selection and maintenance are vital for industry professionals. Having a comprehensive understanding of pulley types not only improves the efficiency of the belt conveyor systems but also enhances trust among stakeholders. This trust translates into a perceived reliability that empowers businesses to operate seamlessly, reassured by machinery that is both competent and enduring.
In conclusion, pulley selection is not merely a component choice but a strategic decision that impacts the entire conveyor system's operational excellence. Businesses seeking to optimize their logistical operations should focus on tailored pulley solutions, ensuring that the system's experience and reliability are uncompromised, ultimately enhancing their overall competitive advantage in the industry.