Pulley systems form the backbone of efficient and reliable belt conveyors, a common feature across various industries from mining to manufacturing. Understanding the different types of pulleys in belt conveyor systems is essential for selecting the right technology that ensures operational excellence.
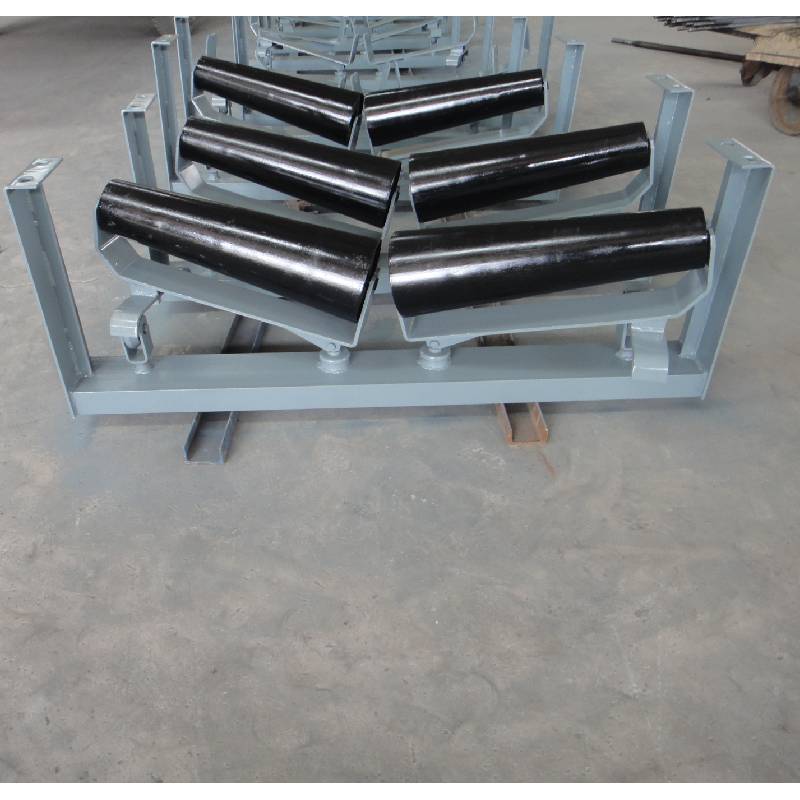
The idler pulley, one of the most ubiquitous types, plays a critical role in directing the belt along the desired path while enabling tension regulation. Built without a mechanical drive, idler pulleys are defined by their simplicity and reliability. Situated along the carrying side of the belt, these pulleys prove essential for preventing sag, which can lead to operational inefficiencies and increased wear and tear on the system. What sets the modern idler pulley apart is its lightweight design and the use of advanced materials that greatly enhance longevity and reduce maintenance requirements.
Another vital component is the drive pulley, which is integral to the motion dynamics of belt conveyors. By interfacing directly with the belt, this pulley initiates the movement of the conveyor system. Driven by electric motors, drive pulleys are typically covered with a lagging material to increase friction, providing the necessary grip to effectively move the belt. Innovations in design have given rise to crowned drive pulleys that automatically center the belt, counteracting misalignment and ensuring smooth, consistent operation.
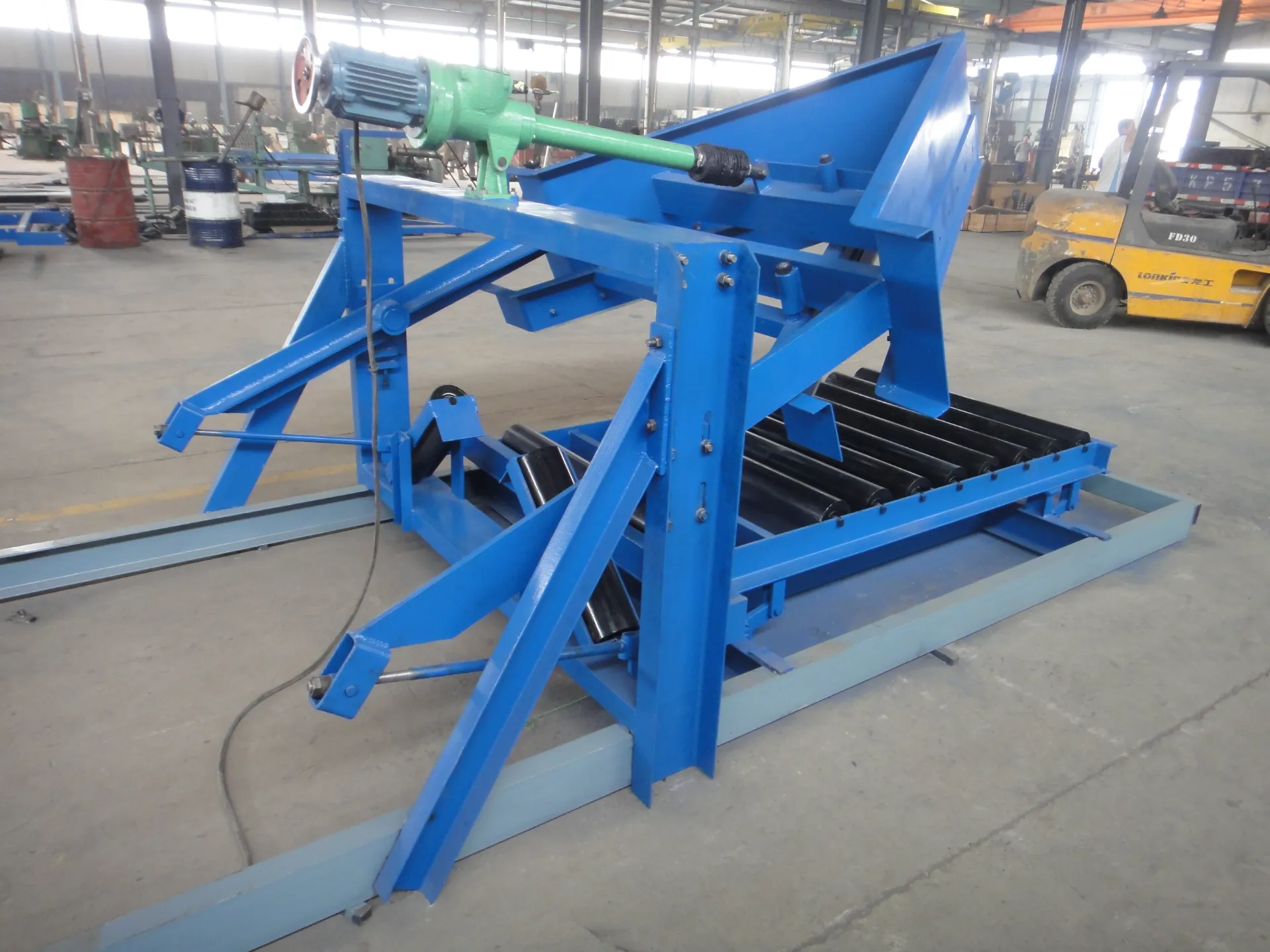
Tail pulleys are positioned at the terminal end of the conveyor, offering a crucial function by providing tensioning adjustments. These adjustments help maintain the required belt tightness to avoid slippage and potential operational failures. The design of tail pulleys often includes features that aid in self-cleaning, reducing the accumulation of debris and materials that can clip the belt surface.
Snub and take-up pulleys add layers of versatility to belt conveyor systems. Snub pulleys wrap the belt closer to the drive pulley, thereby increasing tension and improving traction. Efficient in power transmission, they are indispensable for systems needing high torque. Take-up pulleys, on the other hand, automatically adjust the belt tension, an innovation that compensates for belt stretch, which is particularly beneficial in long conveyor systems. Their ability to dynamically adapt to environmental and operational changes makes them an industry favorite.
types of pulley in belt conveyor
Furthermore, bend pulleys are employed to change the direction of the belt in complex conveyor configurations. These pulleys excel in adapting to spatial constraints, allowing the conveyor system to fit within the architectural limits of a facility without sacrificing performance or safety.
The role of wing pulleys cannot go unmentioned. Used primarily in bulk material handling, wing pulleys incorporate a unique design that reduces material buildup and facilitates self-cleaning. Operating in arduous environments where material spillage is a concern, these pulleys promote enhanced system lifespan and decrease downtime associated with maintenance.
For industry experts, selecting the right type of pulley goes beyond merely understanding their function. It requires a deep knowledge of material properties, environmental conditions, and specific operational demands. When chosen wisely, pulleys can drastically reduce operational costs, improve system reliability, and extend the lifespan of the conveying equipment.
Advancements in pulley technologies continue to evolve, with a focus on sustainability and efficiency. Innovations like energy-efficient motors and smart monitoring systems are setting new standards within the industry. Intelligent monitoring and predictive maintenance, powered by IoT-based solutions, maximize uptime and operational efficiency by alerting operators to potential issues before they culminate in failures, a testament to the ever-growing integration of technology in industrial processes.
In conclusion, understanding the diverse types of pulleys in belt conveyor systems is imperative for maintaining high-performance standards in any industry reliant on material handling. The right choice can lead to significant improvements in productivity and cost efficiency, establishing a cutting-edge operation that stands out for its authority, expertise, and trustworthiness.