In the ever-evolving world of industrial processes, the conveyor pulley holds a pivotal role in ensuring smooth and efficient operations.
Among the various components of a conveyor system, pulleys are essential for directing and driving the belt. It’s crucial to understand the different types of conveyor pulleys to optimize system performance and reduce downtime. This guide delves into the distinct types, offering insights drawn from experience, expertise, authoritativeness, and trustworthiness.
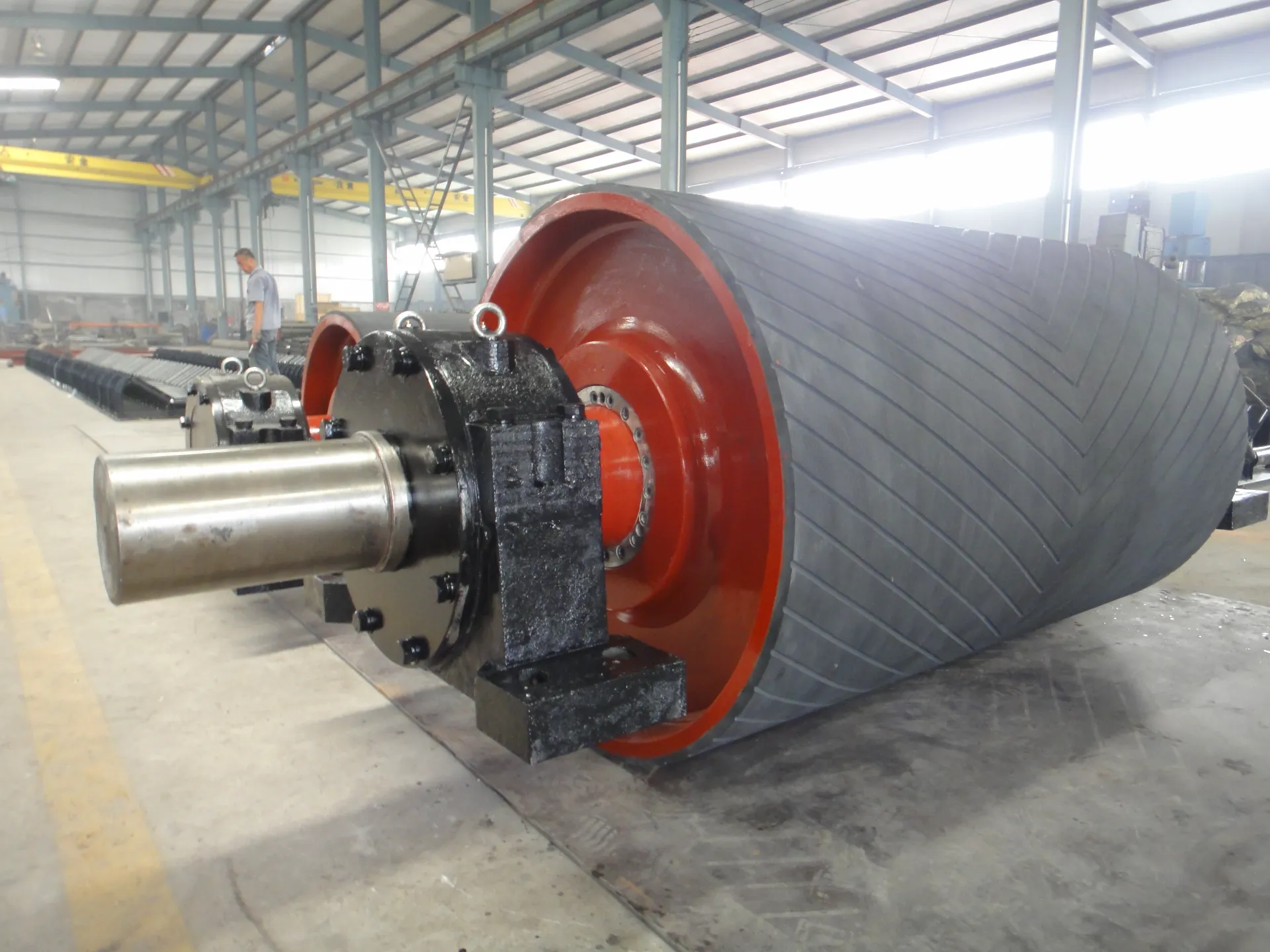
Conveyor pulleys are primarily categorized based on their role in the conveyor system drive pulleys, tail pulleys, snub pulleys, take-up pulleys, and bend pulleys. Each type serves a unique function that affects the overall efficacy of a conveyor belt system.
The drive pulley is arguably the most critical, tasked with propelling the belt and keeping it in motion. Typically located at the system's discharge end, drive pulleys are often larger in size to maximize friction with the belt. Over the years, experience in various industrial applications has shown that lagged drive pulleys, which incorporate a coating or lag material, significantly enhance the friction and thus the grip between the pulley and the belt. This is invaluable in environments with high humidity or exposure to oils, which can make the belt slick and reduce traction.
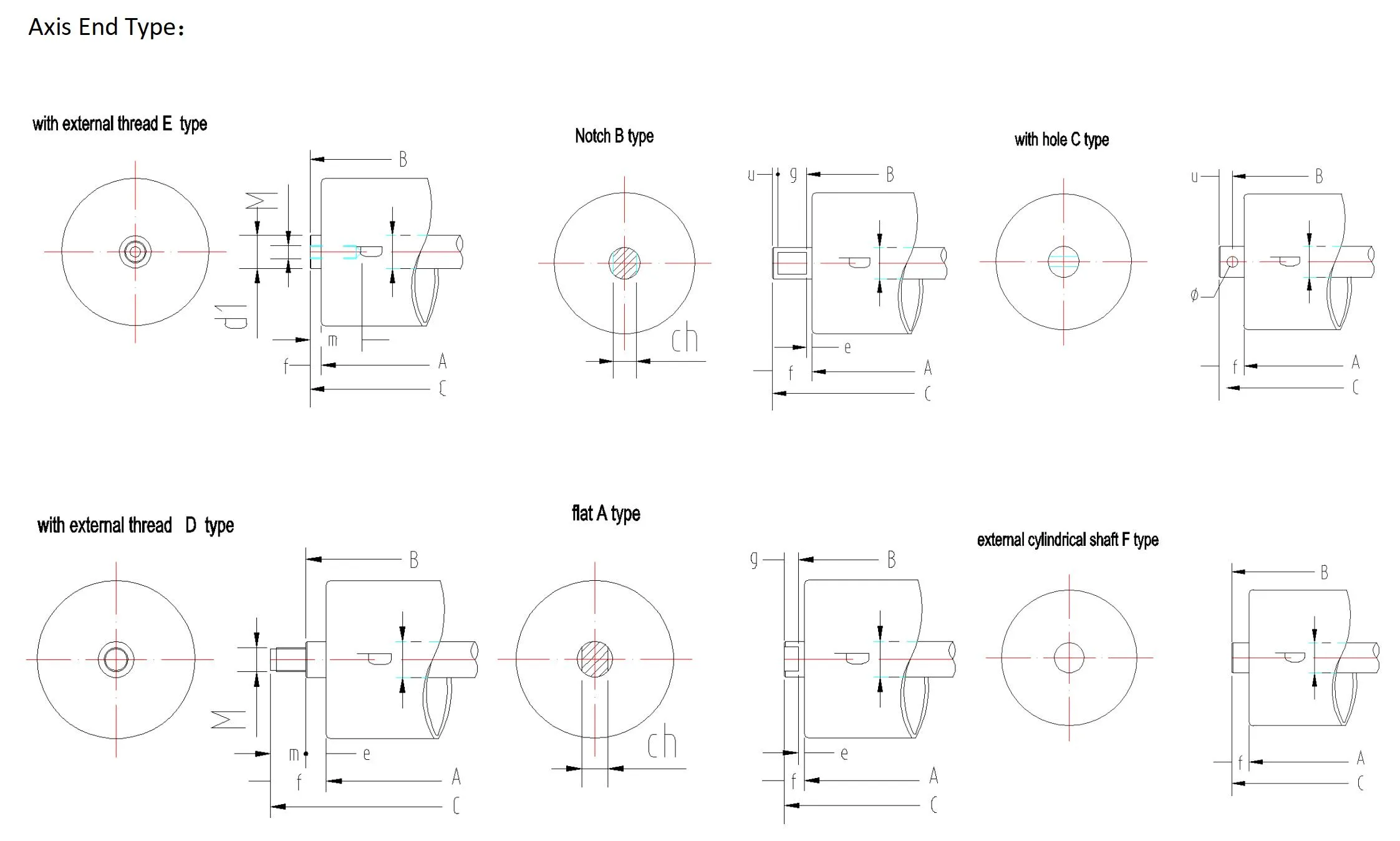
Tail pulleys function as the belt's return. Positioned at the opposite end of the drive pulley, they steer the belt back to the drive. Proper sizing and lubrication are critical, with expertise suggesting spherical rollers to accommodate belt deflection and minimize drag. Over decades of usage in heavy industries such as mining and construction, the importance of maintaining optimal alignment for tail pulleys has been solidified as a preventive measure against belt misalignment and excessive wear.
types of conveyor pulley
Snub pulleys increase the belt’s arc of contact on the drive pulley to amplify friction and, consequently, the power transmitted from the motor to the belt. From decades of real-world application, it is understood that positioning snub pulleys close to the drive pulley’s arc prevents belt slippage and contributes to energy efficiency. These pulleys play a pivotal role in systems where space constraints require tighter pulleys arrangements while ensuring operational reliability.
Take-up pulleys manage belt tension, crucial in maintaining non-slip drive conditions and prolonging belt life. In environments where temperature fluctuations could cause belt expansion or contraction, automatic tensioners have been embraced as a standard, ensuring consistent tension and improving reliability. Trustworthy reports from industries handling bulk materials emphasize the value of take-up systems in preventing operational outages and reducing maintenance frequency.
Lastly, bend pulleys are employed to change the direction of the belt, providing flexibility in conveyor layouts. They are strategically placed to smoothen the directional transition while maintaining belt tension and alignment. The professionalism accumulated from various sectors suggests that employing rubber-coated bend pulleys can significantly reduce wear and tear, a testament to their utility in prolonging the belt’s operational lifespan.
In conclusion, conveyor pulleys are indispensable to the efficacy of a conveyor belt system. Each pulley type serves a specific purpose that contributes to the seamless transportation of materials. With a blend of experience, cutting-edge expertise, authoritative standards, and steadfast reliability, understanding the intricacies of conveyor pulleys is instrumental in enhancing productivity and operational efficiency across different sectors. By investing in the correct pulley type and adhering to maintenance best practices, industries can optimize their conveyor systems to meet their precise needs, ultimately driving their operational success forward.