In the realm of material handling, conveyor belts play a pivotal role in optimizing processes and enhancing productivity. Among the key components vital to the functionality and efficiency of conveyor systems are pulleys. As an expert in conveyor technology, understanding the different types of pulleys used and their specific applications can significantly contribute to systems operation excellence.
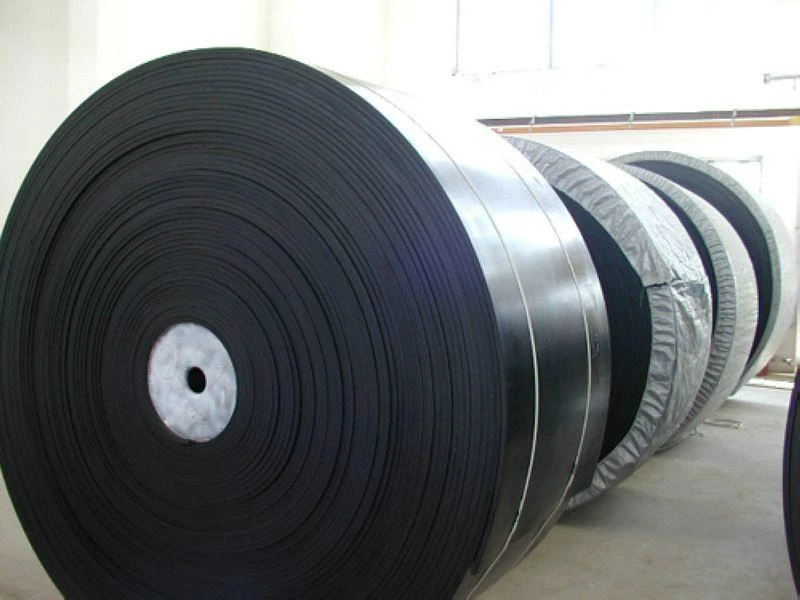
Conveyor belt systems utilize various pulley types, each designed to fulfill distinct roles crucial to the conveyor's operation. The head pulley is fundamental, typically situated at the discharge end of the conveyor.
It serves as the driving force behind the conveyor belt movement, driven by external motors. For applications demanding superior grip to prevent slippage, rubber lagging is often applied to increase friction between the belt and the pulley.
The tail pulley, in contrast, is located at the opposite end, acting as a tensioning tool. This component ensures that the belt remains taut by adjusting based on the distance between itself and the head pulley. Proper tensioning is critical in preventing belt slack, which could lead to operational inefficiencies or mechanical failures.
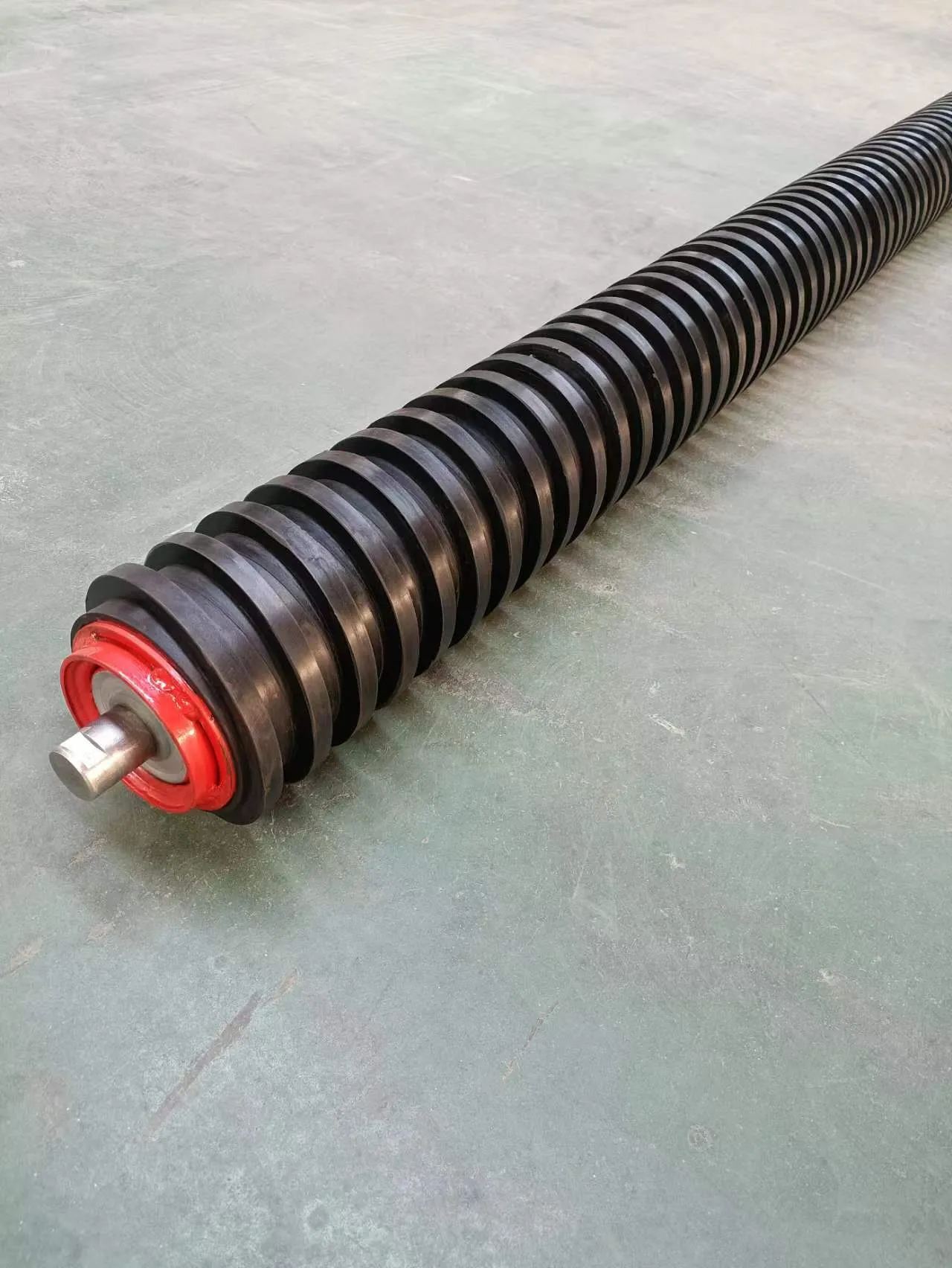
Snub pulleys, located close to the head pulley, serve to increase the belt wrap around the head pulley. This increased contact area enhances the transmit of force from the drive motor, augmenting power transfer and minimizing belt slippage, especially in high-capacity systems.
A bend pulley is utilized to alter the belt's direction, facilitating smoother and more versatile conveyor routing. These components are integral in intricate systems where conveyor pathways must adapt to spatial constraints while maintaining efficient flow.
types of pulley in conveyor belt
In heavy-duty applications, take-up pulleys come into play as components designed to prolong system longevity by moderating belt tension. They accommodate belt stretching and wear, utilizing either manual or automatic tensioning mechanisms. Properly adjusted take-up pulleys ensure optimal belt tracking and reduce the risk of malfunction due to misalignment or excess stress.
For specialized applications, wing pulleys are particularly beneficial in environments with materials susceptible to sticking. Their unique construction includes wing-like features that shed sticky substances, maintaining a clean belt surface and mitigating carry-back concerns.
Within the industry, trusted manufacturers prioritize quality and precision engineering in pulley fabrication, recognizing the impact these components have on operational dependability and safety. Adopting quality pulleys from reputable sources is imperative, ensuring long-term performance and reducing maintenance costs.
Staying abreast with innovative pulley designs and material advancements can empower professionals to select the most suitable pulley type for their specific applications, fostering improved conveyor operation, lower downtime, and enhanced productivity.
In crafting a conveyor belt system that meets rigorous industrial standards, selecting the right pulley types and maintaining them with expertise reflects a commitment to excellence and reliability. This understanding not only underscores the significance of each pulley within a conveyor framework but also solidifies the authoritative stance of an expert well-versed in the nuances of material handling solutions.