In the expansive world of industrial machinery and conveyance systems, drum pulley lagging stands out as a pivotal component ensuring optimal efficiency and longevity. This article provides an in-depth exploration of drum pulley lagging, delving into the benefits, types, and significant influence on equipment performance through the eyes of a seasoned expert.
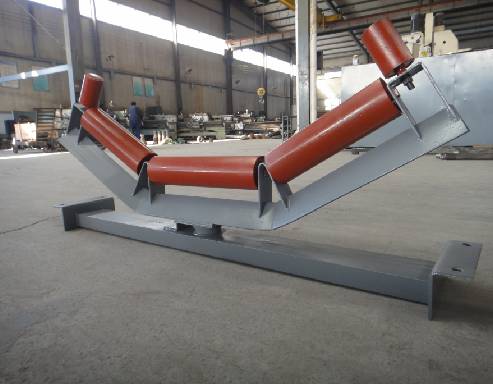
A fundamental understanding of drum pulley lagging reveals its role as an essential feature of conveyor systems used across various industries. It functions by providing a friction-enhancing layer on the drum pulley, which is crucial in maintaining accurate belt alignment and reducing wear and tear. The adoption of high-quality lagging can significantly extend the life span of conveyor belts, reducing operational costs.
The expertise behind choosing the right drum pulley lagging begins with acknowledging the types available. Common categories include rubber lagging,
ceramic lagging, and urethane lagging. Each type has unique properties tailored to specific operational challenges.
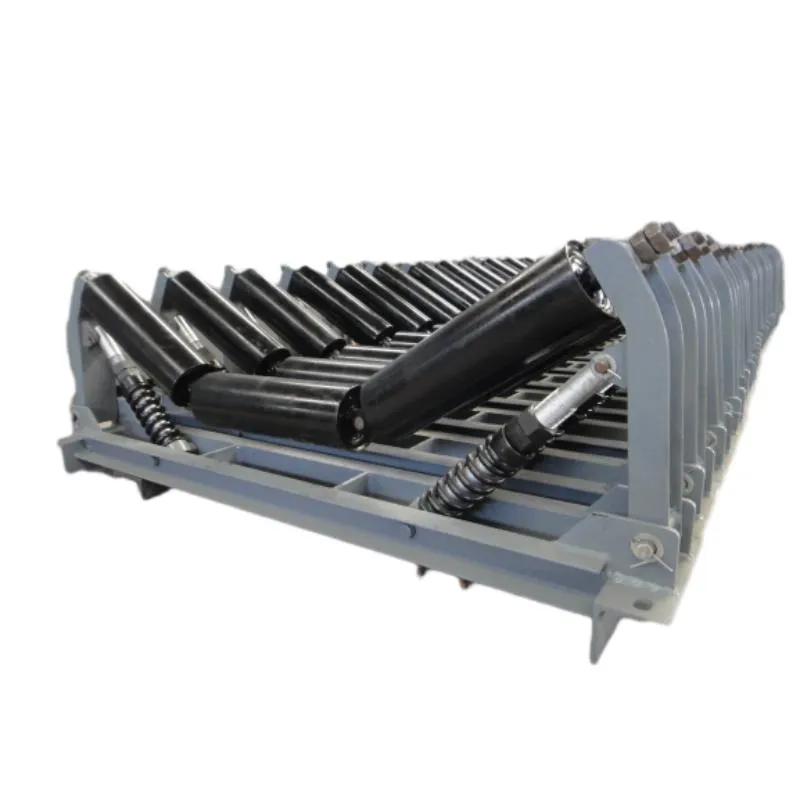
Rubber lagging is celebrated for its versatility and cost-effectiveness. It provides excellent grip and is capable of dissipating water, which minimizes slip during operations. This type of lagging is a staple in many industries, including agriculture and mining, where conditions can be slippery and abrasive. Its flexibility and ease of installation make it a favored choice for operations that require quick maintenance without substantial downtime.
For environments where abrasion resistance and maintenance of peak performance in harsh conditions are critical, ceramic lagging emerges as the premier choice. Composed of ceramic tiles embedded in a rubber matrix, this type offers superior durability and reduced maintenance costs over time. Industries heavy in material handling, such as the transport of ores or coal, benefit the most from ceramic lagging, as it can withstand the abrasive nature of these materials with unparalleled resilience.
drum pulley lagging
Urethane lagging, known for its high-performance capabilities, bridges the gap between rubber and ceramic in terms of durability and cost. It provides excellent resistance to chemical exposure, making it ideal for environments where material spillage or leakages are a concern.
Authority in the selection and maintenance of drum pulley lagging involves understanding the specific needs of the machinery involved. Engineers and maintenance crews must consider factors such as operational speed, environmental conditions, and the nature of materials being transported. Incorporating thorough risk assessments, customized lagging solutions can be developed to optimize performance and lifespan, reflecting a deep expertise in machinery care and reliability.
Alongside the technicalities, trustworthiness in the realm of drum pulley lagging is built upon a foundation of credible product sourcing and installation craftsmanship. Partnering with manufacturers that uphold rigorous quality standards ensures that the lagging materials used are of the highest caliber. Additionally, investment in reliable and skilled technicians for the installation process is crucial, as improper lagging fitting can negate potential benefits, leading to increased downtime and costs.
The real-world experience of utilizing efficient drum pulley lagging has demonstrated its significance in boosting operational productivity. Case studies often highlight a remarkable reduction in belt slippage, leading to smoother operation and fewer interruptions in workflow. This enhances the overall handling efficiency, ensuring that installations meet their throughput targets with minimal disruption.
In essence, drum pulley lagging serves as a guardian of conveyor systems, ensuring longevity and efficiency are upheld. Through expert selection, installation, and maintenance, it is instrumental in influencing positive industrial outcomes. This insight not only supports the practical applications but also stands as a testament to the authority and credibility required in optimizing conveyor system performance. Industry leaders who recognize and apply true expertise in the field will continue to benefit from the substantial return on investment provided by high-quality drum pulley lagging solutions.