Choosing the right conveyor roller pulley can significantly impact the efficiency and longevity of conveyor systems, a crucial component in industries ranging from manufacturing to logistics. Here's an exploration into this pivotal element, informed by hands-on experiences and industry expertise.
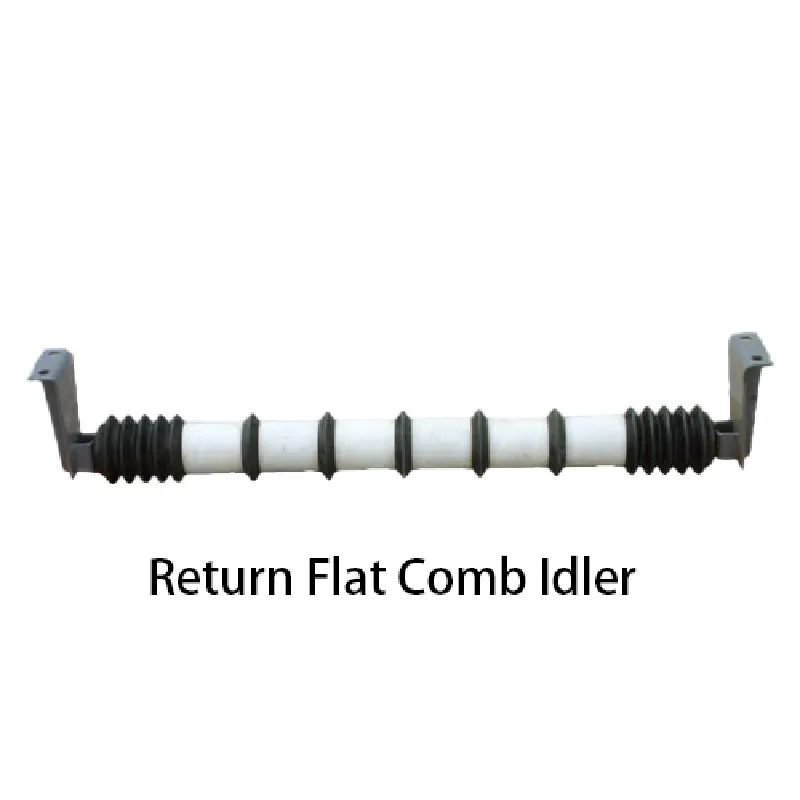
Conveyor roller pulleys serve as the heart of most material handling systems. They are responsible for driving the conveyor belt and ensuring smooth transportation of goods. Therefore, selecting an optimal pulley system is not merely a matter of checking specifications but understanding its role in the larger operational context.
A pivotal consideration when choosing a conveyor roller pulley is the material composition. Steel pulleys are renowned for their durability and strength, making them ideal for heavy-duty operations. However, for industries that require lightweight solutions or deal with corrosive materials, aluminum and stainless-steel options offer a strategic advantage. These materials resist corrosion while maintaining structural integrity under varying loads.
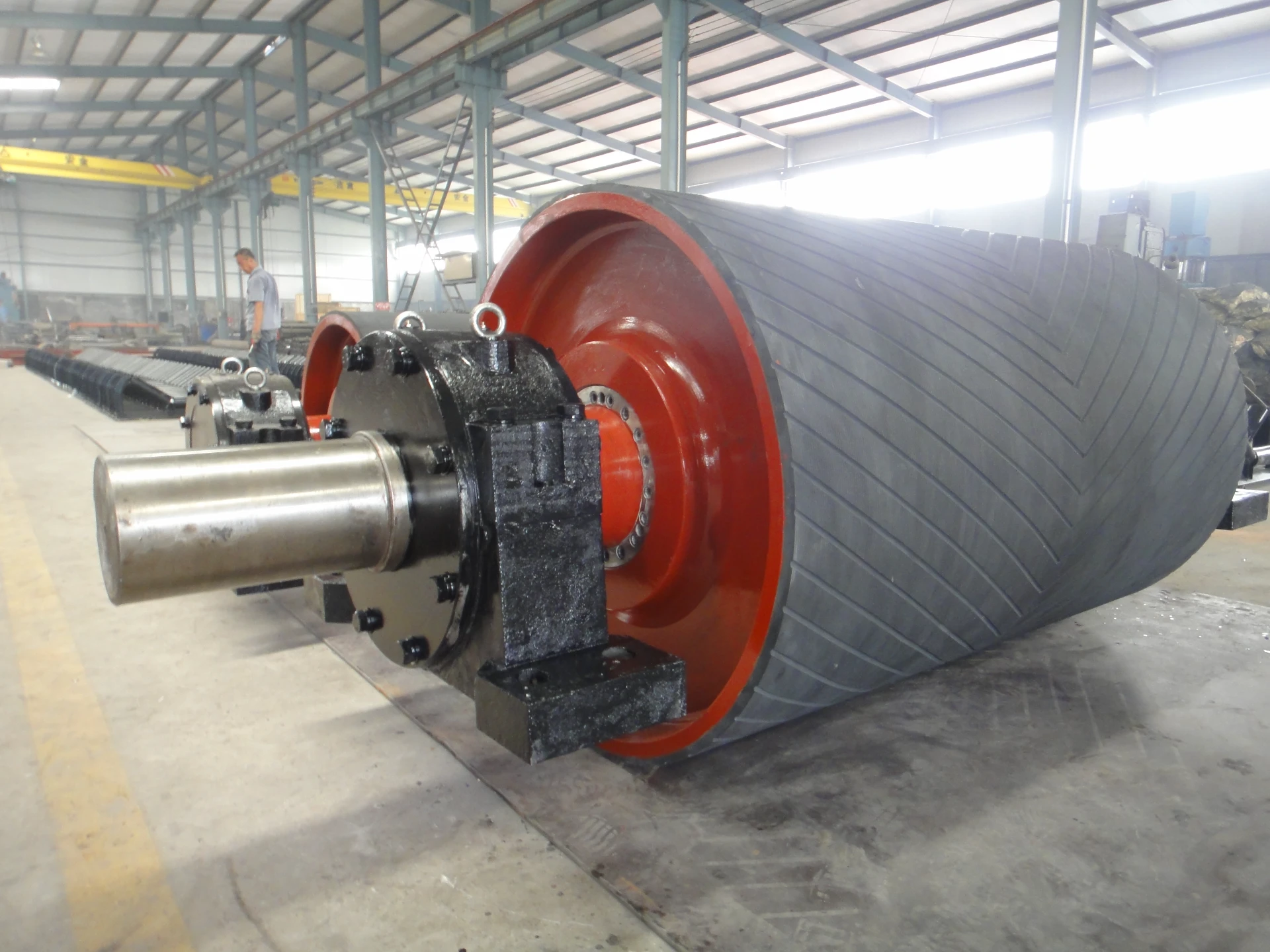
Industry experience reveals that pulley design significantly influences operational efficiency. Crowned pulleys, for instance, prevent belt slippage by promoting self-centering of the belt, a feature crucial in maintaining operational consistency and reducing downtime associated with belt misalignment. Furthermore, drum pulleys with a larger diameter can reduce belt tension, thereby extending the belt's lifespan. Such technical nuances underscore the importance of aligning pulley type with operational requirements.
Maintenance ease and accessibility also play a vital role. From an operational reliability perspective, investing in conveyor roller pulleys that simplify maintenance processes can reduce the total cost of ownership. For instance, pulleys with sealed bearings offer the advantage of being low maintenance by protecting components from dust and debris, thereby enhancing system reliability.
conveyor roller pulley
Furthermore, an expert’s take on pulley lagging indicates its importance in enhancing grip and performance. Lagging material, such as rubber, has been shown to increase friction, reduce belt slippage, and effectively increase the lifespan of both the pulley and the belt. On the other hand, ceramic lagging is often preferred in environments where superior grip and durability are needed despite challenging conditions.
The complexity of conveyor systems necessitates a well-rounded understanding not just of the pulley itself, but how it interacts with other system components. Installing a well-matched motor and speed controller with your roller pulley is essential. These components should synchronize to avoid excessive wear or unnecessary energy consumption – factors that can significantly inflate operational costs over time.
As an authoritative voice in the field, understanding and communicating the implications of each choice and design consideration cannot be understated. Expert consultation and collaboration with manufacturers that offer custom pulley solutions can provide additional optimization avenues tailored to specific project requirements. This personalized approach not only meets immediate operational goals but also aligns with long-term business strategies.
This expert insight emphasizes trustworthiness through methodical and pragmatic analysis of conveyor roller pulley choices. By leveraging empirical evidence and drawing on deep-seated industry knowledge, stakeholders can make informed decisions that bolster their operational frameworks.
Undoubtedly, the selection of conveyor roller pulleys is a multifaceted process that intertwines technical precision, durability considerations, and operational adaptability. This comprehensive understanding enables businesses to uphold their commitment to efficiency and reliability in ever-evolving industry landscapes.