Choosing the right conveyor belt pulley type is crucial for optimizing the efficiency and longevity of a conveyor belt system. With numerous pulley types available, each suited for specific applications, understanding their differences can be the key to success in materials handling. This guide provides in-depth insights into various conveyor belt pulley types based on technical expertise and real-world applications, thereby enhancing your knowledge and confidence in making informed choices.
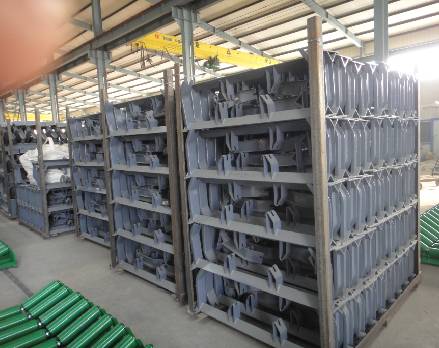
1. Drum Pulleys
These are the most common type used in general conveyor systems. The drum pulley’s cylindrical design is paramount in offering uniform tension across the belt, reducing the chances of slippage. Experience from many manufacturing operations has shown that drum pulleys are incredibly versatile, adaptable to a wide range of belt conditions. These pulleys come with either flat or crowned faces, enhancing tracking capabilities, especially beneficial for long conveyor systems.
2. Wing Pulleys
Wing pulleys find their niche in environments prone to material build-up. Featuring a set of 'wings' or fins that shed material off the pulley, these types reduce belt misalignment and excess wear. Industries dealing with sticky or wet materials often favor wing pulleys because they minimize downtime required for cleaning. The authoritative design of the wing pulley ensures the system remains operational even under challenging conditions, securing trust from many industrial clients.
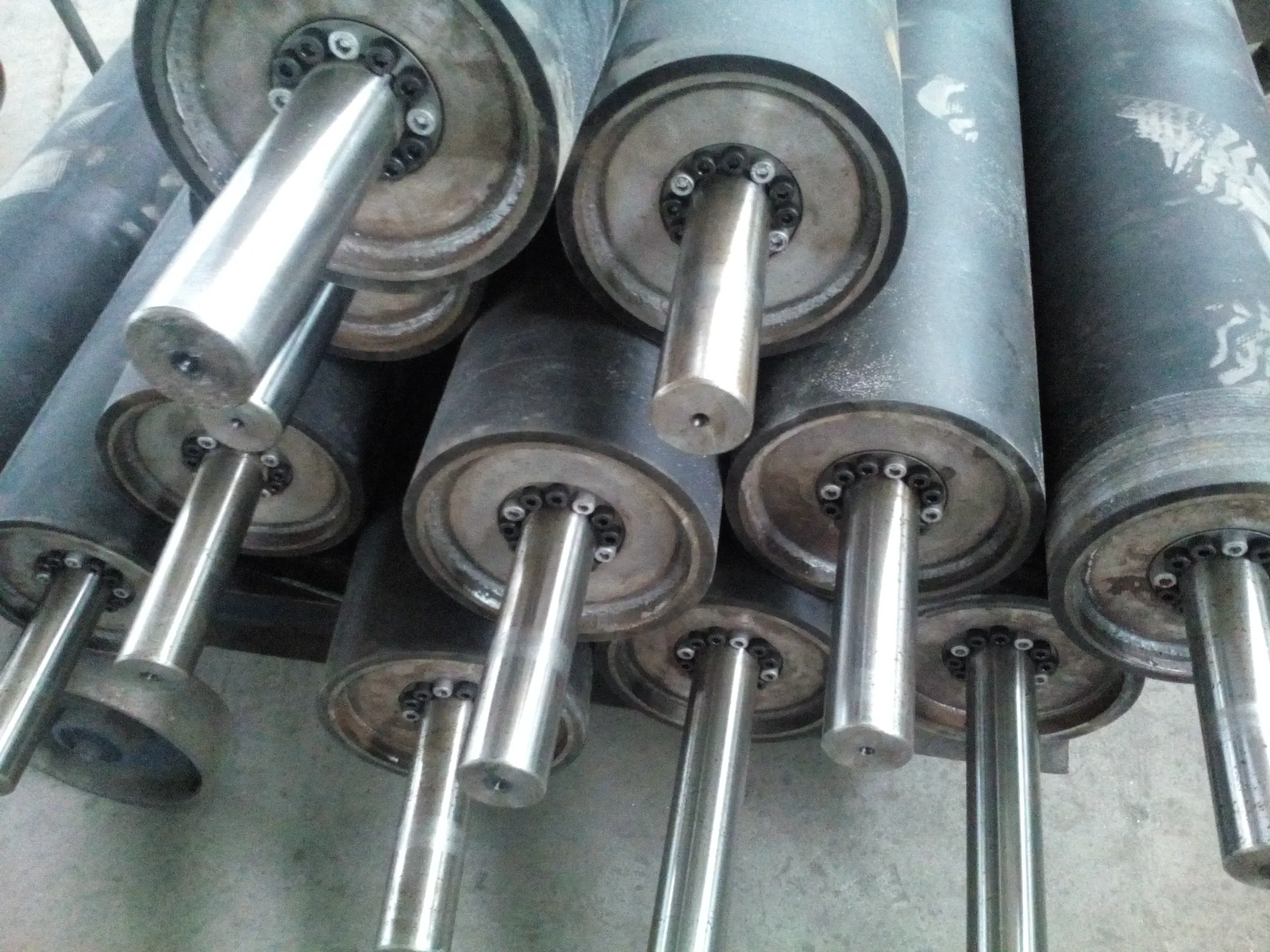
3. Motorized Pulleys
As an efficient and space-saving solution, motorized pulleys encapsulate the drive motor within the pulley shell itself. This design not only reduces maintenance but also provides a safer operation environment by eliminating external components. Real-world implementations have praised motorized pulleys for their neatness and the reduced need for safeguarding measures typically required for traditional drive systems. Furthermore, their credibility lies in offering consistent operational efficiency and reliability.
conveyor belt pulley types
4. Lagged Pulleys
Lagged pulleys are drum pulleys covered with a material like rubber or ceramic to increase friction between the belt and pulley. This design mitigates belt slippage and optimizes power transmission, which is critical when handling heavy loads. Lagging materials are chosen based on rigorous expert assessments of operating conditions, such as temperature and moisture levels. Many conveyor systems, particularly in mining sectors, trust lagged pulleys to function reliably despite environmental challenges.
5. Snub Pulleys
These pulleys are employed to increase the wrap angle of a conveyor's head or tail pulley, thus enhancing the tension on the belt. They are positioned close to the drive pulley and can significantly extend the life of conveyor belts by alleviating undue stress. The expertise required to position snub pulleys correctly underscores their importance in intricate belt systems.
6. Take-Up Pulleys
Crucial for maintaining consistent tension in a conveyor belt, take-up pulleys adjust to the dynamics of operation. Leveraging sophisticated tensioning mechanisms, these pulleys prevent slack and ensure seamless operation. Such systems require installation precision and ongoing adjustments, a task suited for those deeply familiar with material handling technologies.
In conclusion, selecting the appropriate conveyor belt pulley type involves understanding specific operational demands and the conditions under which your conveyor system operates. Through specialized knowledge and practical experiences, each pulley type offers unique advantages. A well-informed choice not only enhances system efficiency but also fortifies the trust and reliability of your material handling solutions. As trends in conveyor technology evolve, staying informed about the capabilities of each pulley type ensures your operations remain cutting-edge and competitive.