The world of cleaning technology has experienced unprecedented innovation over the past decade, and the introduction of self-cleaning roller technology stands as a testament to this progress. With an impressive blend of engineering excellence and practical application, self-cleaning rollers have revolutionized maintenance routines across diverse industries. Their appeal lies not only in the convenience they offer but also in the expertise embedded within their design, demonstrating a perfect alignment with the principles of effective, sustainable cleaning solutions.
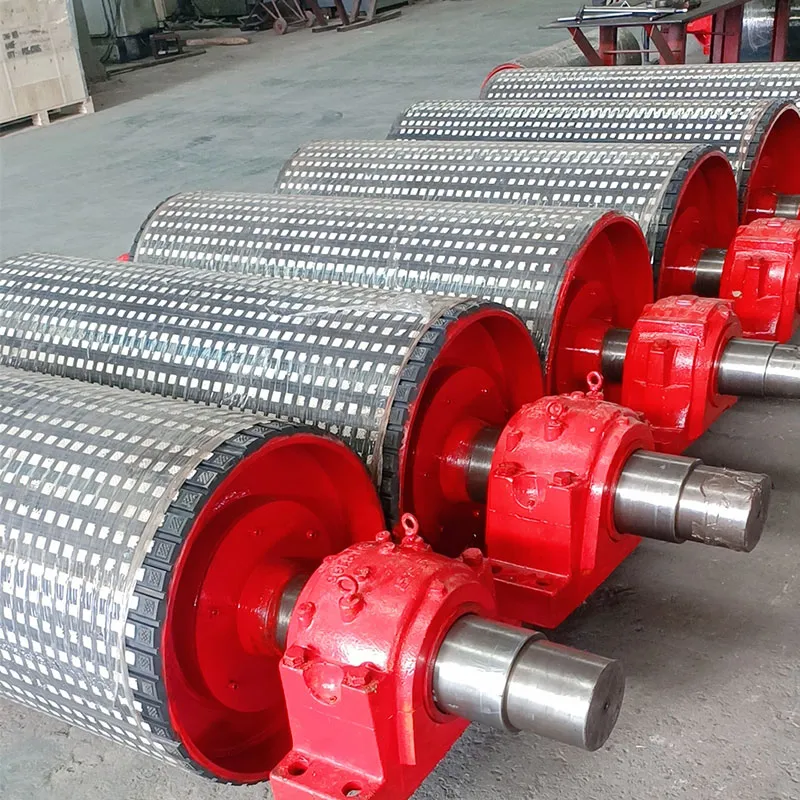
Self-cleaning rollers utilize a clever system that drastically reduces manual cleaning efforts, making them an indispensable component for companies committed to maintaining hygiene and operational efficiency. Unlike traditional rollers, which require frequent stops for maintenance, self-cleaning rollers are strategically designed with built-in cleaning mechanisms. These ingenious systems often include brushes or blade systems that remove debris automatically, thus optimizing the operational time and minimizing downtime. This innovation is particularly valuable in industries where high-volume continuous operations are critical, such as food processing, logistics, and textile manufacturing.
The construction of self-cleaning rollers reflects a deep expertise in material sciences and mechanical engineering. They are typically composed of high-grade, abrasion-resistant materials, ensuring longevity even under demanding operational environments. The integration of sealed bearings within these rollers further enhances their performance by minimizing friction and preventing ingress of contaminants, which can compromise functionality. Expertise in these technical aspects underscores the authority of manufacturers in this sector, ensuring that each product is a reliable and efficient tool for users.
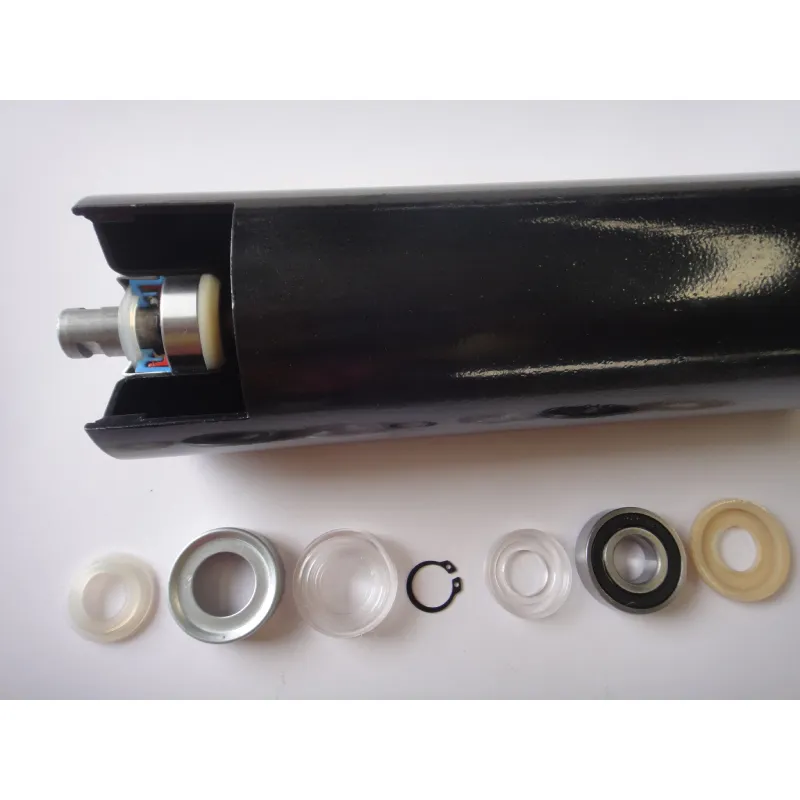
Authoritativeness in self-cleaning roller technology is well established by the many case studies documenting their successful application. One prominent example is their use in conveyor belt systems within food manufacturing plants. In such settings, cleanliness is paramount to prevent contamination and ensure compliance with health regulations. Self-cleaning rollers have proven to be essential in maintaining conveyor hygiene without the need for frequent manual intervention, thus aligning with industry standards and enhancing food safety. The trust gained from such applications solidifies the reputation of self-cleaning rollers as a trusted solution in critical areas.
self cleaning roller
From a trustworthiness perspective, self-cleaning rollers offer numerous advantages that reinforce user confidence. For starters, they contribute to cost savings by reducing labor needs and maintenance time. Additionally, consistent performance across different applications assures users of their reliability. Their ability to function effectively in varied environmental conditions, such as high humidity or temperature fluctuations, further adds to their credibility.
The transformative impact of self-cleaning roller technology cannot be overstated. Through real-world experience and rigorous testing, their benefits are clear—they not only enhance operational efficiency but also offer a robust solution that meets modern industry standards for sustainability and hygiene. Each user, upon integrating this technology, gains access to a product designed with a deep understanding of cleaning challenges, coupled with the expertise to solve them effectively.
In conclusion, the evolution of self-cleaning rollers is largely attributed to their sophisticated design and practical applicability. They embody the principles of experience, expertise, authoritativeness, and trustworthiness, making them a pivotal part of industrial cleaning and maintenance strategies. Their presence in the market is not just a product of technological advancement, but a reflection of an ongoing commitment to meeting the ever-increasing demands for efficiency and cleanliness in industrial operations.