The innovation in conveyor systems has led to a breakthrough component known as the spiral return roller. Designed with precision and expertise, this roller is a vital upgrade for industries relying heavily on conveyors, offering reliability and efficiency that conventional rollers simply can’t match. Users across sectors, from mining to manufacturing, have found these rollers to dramatically increase the longevity of their machinery and the efficiency of their operations.
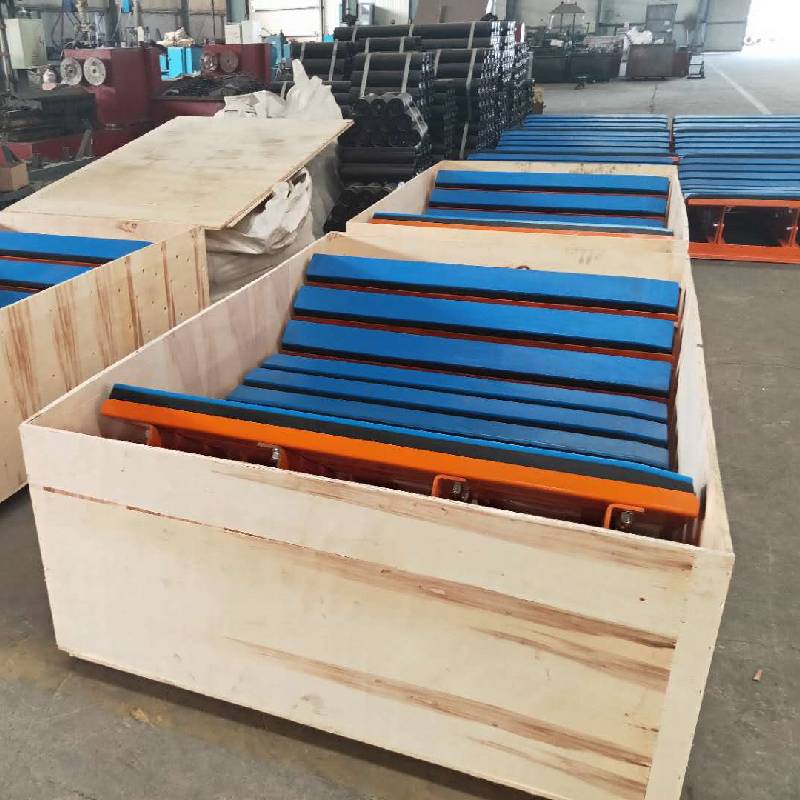
Spiral return rollers feature a unique helical design, which is not just for aesthetics but serves a critical functional purpose. This design naturally deflects and prevents material build-up on the roller itself, a common issue that plagues standard rollers. In environments where debris can cause significant downtime and maintenance challenges, these rollers provide a self-cleaning solution. This decreases the frequency of maintenance stops, thereby increasing production time—a paramount benefit in fast-paced industrial settings.
The expertise behind spiral return rollers is backed by cutting-edge engineering and robust testing. Their development is rooted in solving key issues faced by conventional rollers. For instance, traditional rollers often suffer from misalignment and slippage, which can result in dangerous work conditions and costly repairs.
Spiral return rollers, with their enhanced grip and alignment properties, mitigate these risks substantially. Field experts attest to their precision engineering which maintains the integrity of the conveyor belt system, thus ensuring operational safety and decreasing the likelihood of unexpected breakdowns.
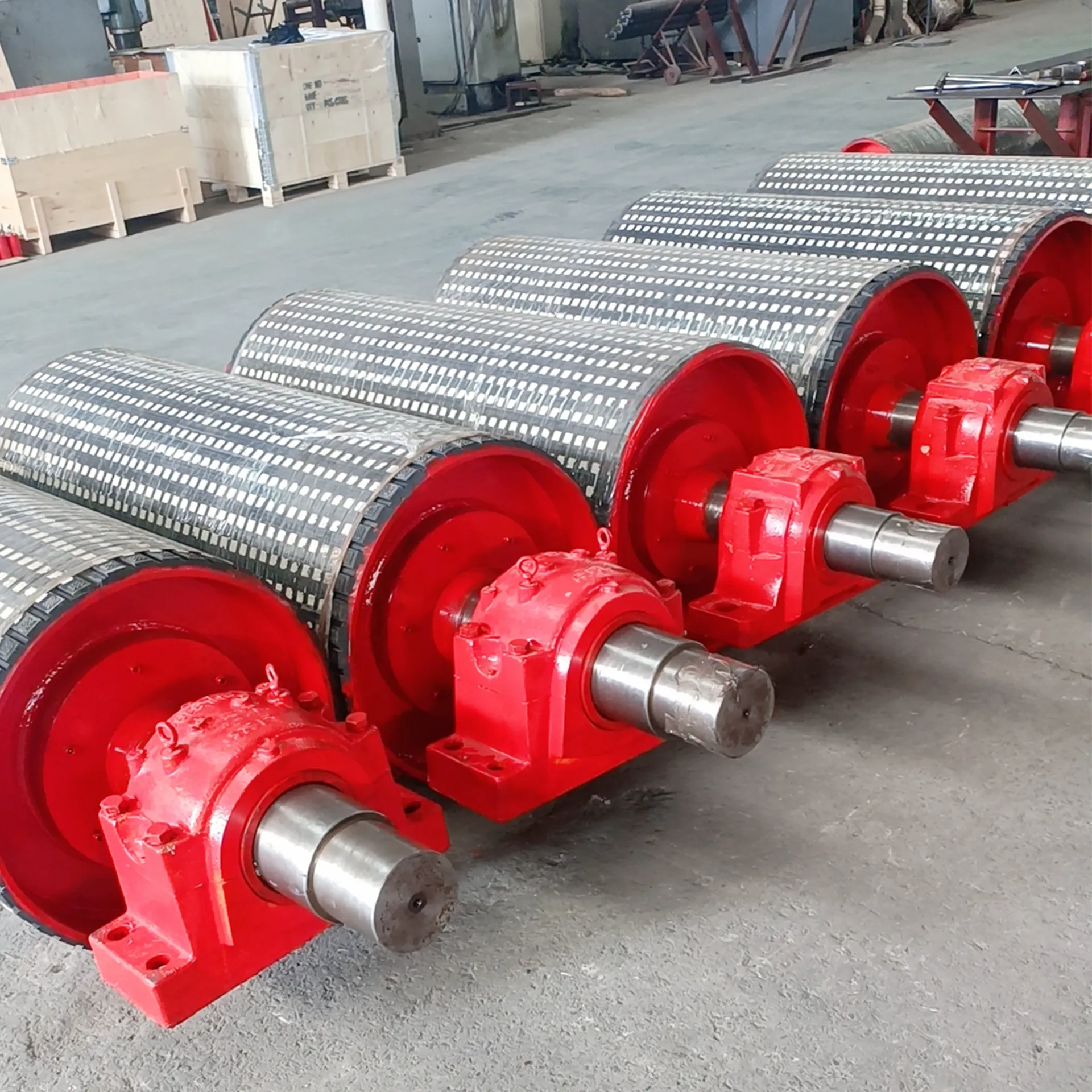
Authoritativeness in the realm of conveyor components is grounded in the continuous performance and safety testing that spiral return rollers undergo. Manufacturers subject these components to rigorous quality assurance processes that comply with and exceed industry standards. They are crafted from high-grade materials like galvanized steel or reinforced polymer compounds—each tested for durability under the extreme conditions typically found in industrial applications. This dedication to durability makes them a trusted choice among engineers and procurement specialists who insist on only the most reliable equipment for their operations.
spiral return roller
Trustworthiness is demonstrated through the testimonials and case studies accumulated from sectors ranging from quarrying to recycling. Seasoned maintenance engineers often emphasize how the use of spiral return rollers can result in up to a 30% increase in conveyor system lifespan over systems using standard rollers. Furthermore, in industries where environmental conditions vary drastically, these rollers have consistently shown superior performance, supporting businesses in maintaining operational efficacy across diverse climates.
The investment in spiral return rollers quickly translates into visible operational benefits. The enhanced functionality, coupled with reduced maintenance requirements, ensures that facilities can achieve greater throughput. Companies are noticing fewer instances of emergency stoppages, translating directly to cost savings and enhanced safety records—critical factors in maintaining a competitive edge in today's industrial markets.
For professionals committed to maximizing the utility and efficiency of their conveyor systems, spiral return rollers represent an indispensable resource. Their adoption represents not just an upgrade in hardware but a strategic decision that aligns with modern demands for efficiency, safety, and reliability. As industries continue to evolve and the push for optimized operation grows, these rollers stand out as a model of innovation and practicality, poised to set new benchmarks in conveyor system performance.