The seal roller stands as an innovative solution in various industries, particularly in manufacturing and packaging, where precise control and efficient sealing play pivotal roles. Understanding the intricacies of the seal roller involves delving into its applications, benefits, working principles, and the expertise required for its optimal utilization. As a cornerstone in versatile sectors, the seal roller demonstrates its significance through practical experience and authoritative insights.
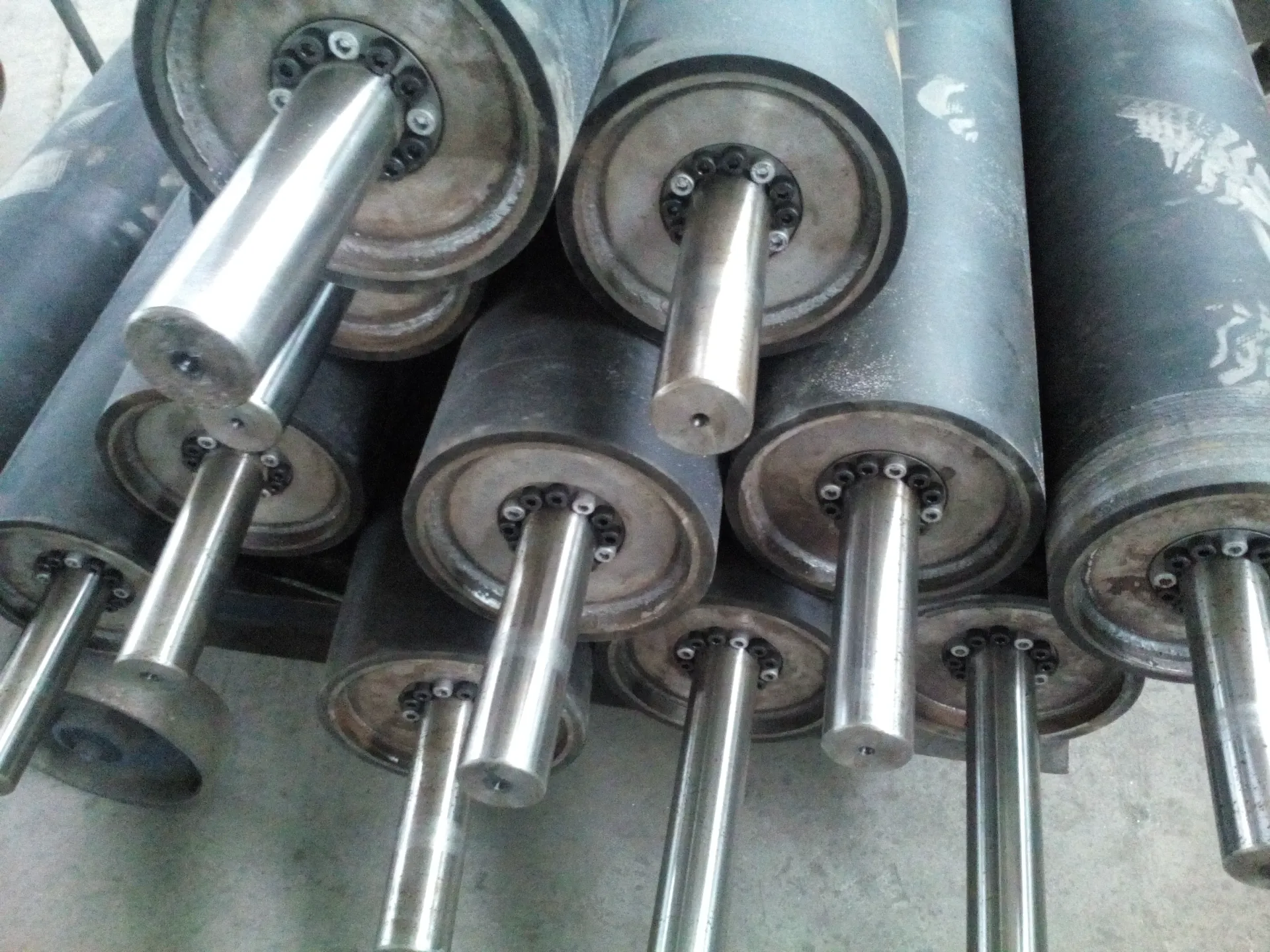
Seal rollers are primarily employed in environments where materials—ranging from plastic films, papers, foils, to textiles—require sealing through pressure and heat.
These components ensure that seams are strong, airtight, and aesthetically pleasing, thereby enhancing product durability and consumer appeal. Their application in conveyor systems and continuous production lines highlights their vital role in high-speed operations, ensuring seamless production without compromising on quality.
Experience in implementing seal rollers in packaging lines reveals significant improvements in operational efficiency. Businesses transitioning to automated sealing processes with these rollers have reported a reduction in labor costs, minimized material waste, and an increase in output capacity. The expertise involved in optimizing these systems often focuses on calibrating pressure, speed, and temperature to suit specific materials, which underscores the technical proficiency required to harness their full potential.
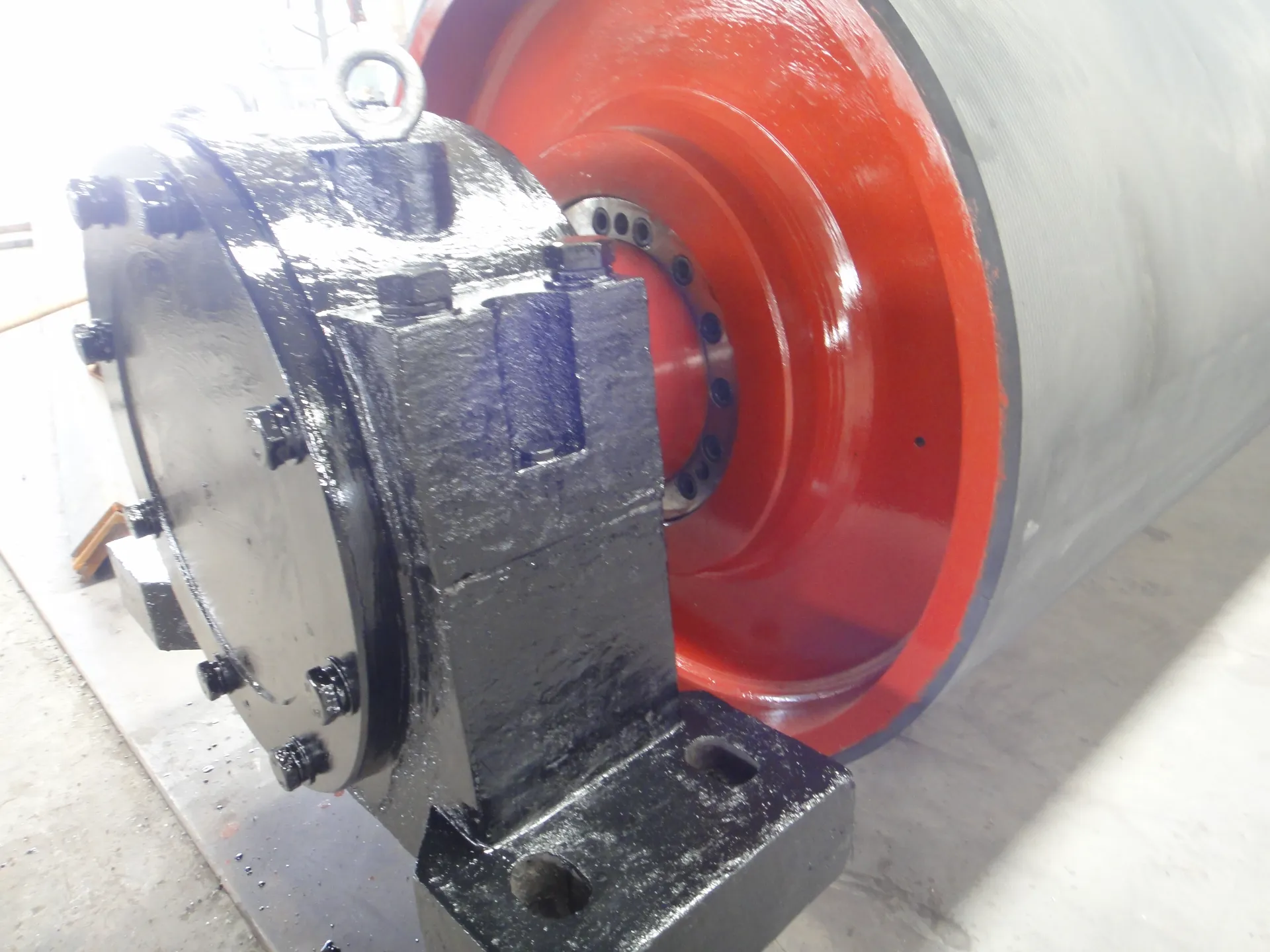
Professionals versed in seal roller technologies emphasize the critical nature of maintenance and regular monitoring. A well-maintained seal roller ensures consistency in quality and can significantly extend equipment lifespan. From an expert standpoint, factors such as roller surface condition, alignment, and wear resistance are paramount in maintaining peak performance. Regular training and upskilling of operators and maintenance staff are essential strategies to uphold the authoritative status of operations using these systems.
seal roller
Authoritative insights into the development and advancement of seal rollers showcase continuous innovations aimed at enhancing their adaptability and efficiency. Modern seal rollers integrate smart technologies, such as temperature sensors and automated adjustments, which further streamline the sealing process. Industry leaders prioritize sustainable materials and energy-efficient designs, aligning with global environmental standards and reinforcing the trustworthiness of seal roller systems in contemporary industrial applications.
Trust in seal roller applications is bolstered by rigorous testing and adherence to safety standards. In sectors like food and medical packaging, where hygiene and safety are paramount, the reliability of a seal roller system underlines its essential role. Compliance with international standards and certifications fosters trust among clients and end-users, ensuring that products sealed by these rollers meet the highest quality expectations.
Choosing the right seal roller involves evaluating several key factors, tailored to specific industry requirements. Professionals recommend considering the nature of the material, production speed, and required seal strength when selecting a seal roller system. Consulting with manufacturers and industry experts often reveals valuable insights into custom solutions that enhance production processes.
In conclusion, the significance of seal rollers in industrial settings is underscored by their capacity to enhance productivity, reduce operational costs, and maintain high-quality standards. Through the lens of experience, expertise, authority, and trust, seal rollers are recognized not only as essential components in modern manufacturing but also as pivotal players in the advancement of technology and efficiency in industrial operations. Whether it's through implementation in packaging lines or integration into automated systems, seal rollers remain fundamental to driving innovation and excellence across numerous industries, ensuring that they remain indispensable in the landscape of modern manufacturing.