Roller seals, a critical component in industrial machinery, possess attributes that ensure efficiency and reliability in various applications. Their vital role in minimizing friction and wear while maintaining robust sealing capabilities makes them indispensable in sectors such as automotive, aerospace, and manufacturing.
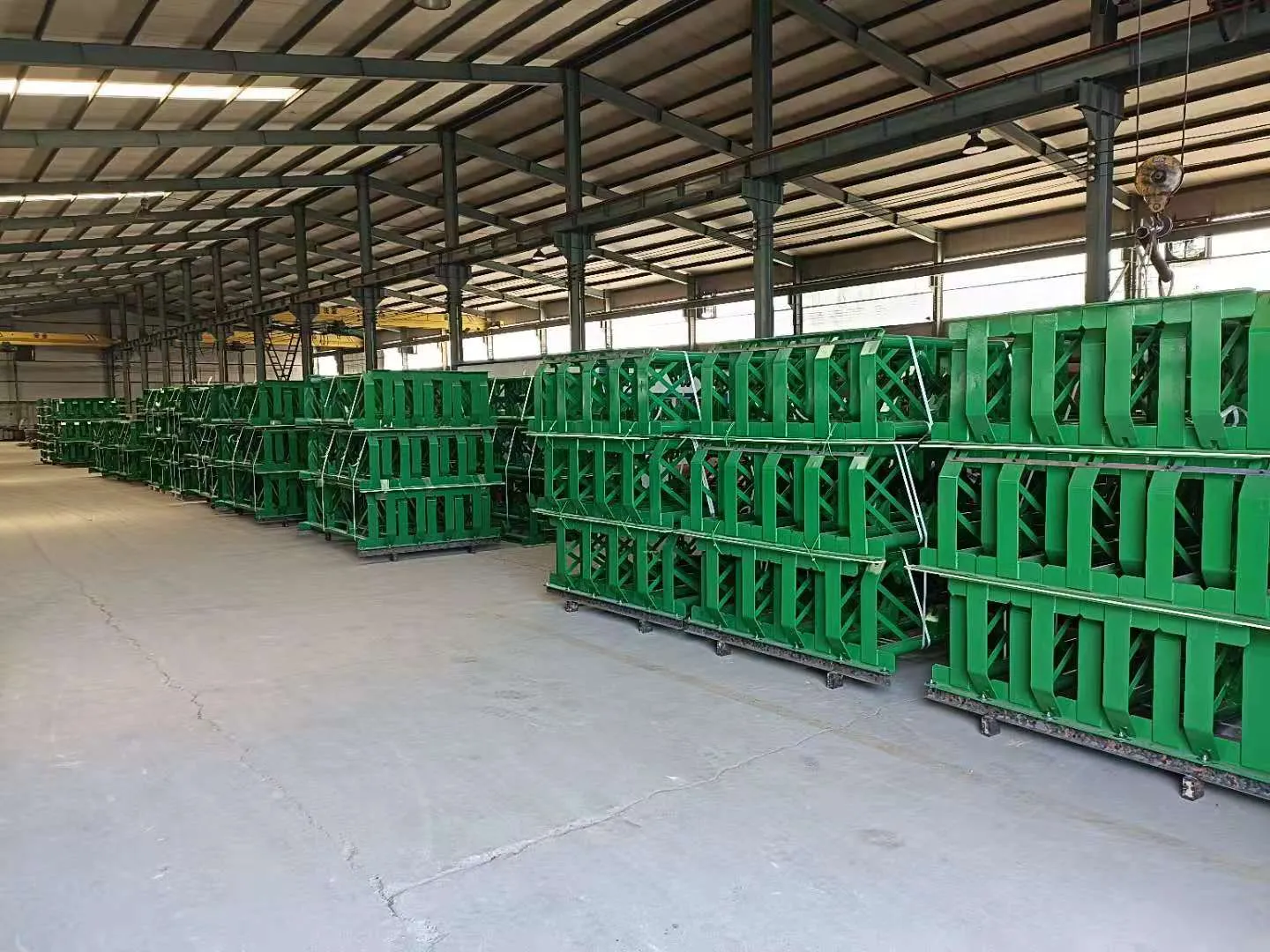
Experience in the field underscores the significance of selecting the appropriate roller seal for specific applications. Industries have witnessed substantial advancements through the integration of high-performance roller seals designed to withstand extreme conditions, such as high temperatures and pressures. Thus, understanding the dynamics of these seals can drastically enhance the longevity and performance of machinery.
Expertise in engineering has led to the development of roller seals with materials that offer exceptional durability. Engineers often choose seals made from materials like nitrile, silicone, and Viton, each providing unique benefits suited to different environmental challenges. For example, Viton seals are renowned for their excellent resistance to heat and chemical exposure, making them ideal for harsh industrial settings.
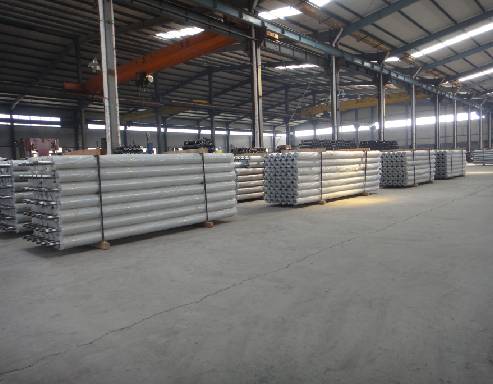
Authoritativeness in the market for roller seals is driven by continuous research and development by leading manufacturers. Companies invest in cutting-edge technology to produce roller seals with enhanced sealing efficiency and lifespan. Patented designs and collaborations with research institutions boost a manufacturer's credibility, ensuring they deliver products that set industry standards for quality and innovation.
Trustworthiness in roller seal brands is cultivated through rigorous testing and quality assurance protocols. Reliable manufacturers implement comprehensive testing regimes, which include lifecycle analysis, to guarantee their products meet the stringent requirements of various industrial applications. Reviews and testimonials from engineers and industry professionals further cement a brand's reputation as a producer of dependable roller seals.
Selecting the correct roller seal involves understanding the specific demands of the application. It's crucial to consider factors such as the operational environment, the type of fluid or gas being sealed, and the mechanical stresses involved. This ensures that the chosen seal not only performs optimally but also contributes to the overall safety and efficiency of the machinery.
roller seal
In addition to material selection, the design and configuration of the roller seal also play critical roles. Advanced computational analyses allow for the design of seals that provide superior sealing performance while reducing energy consumption. Optimal seal design helps in minimizing leakage, thereby enhancing the operational efficiency of the machinery it supports.
To fully harness the benefits of roller seals, proper installation and maintenance are essential.
Incorrect installation can lead to premature wear or failure, even in seals made from the highest-quality materials. Regular inspections and maintenance routines prolong the life of the seal and the equipment it serves, offering peace of mind to operators and reducing downtime due to equipment failure.
The integration of roller seals in preferred machinery exemplifies how targeted innovation and attention to detail can uplift the performance standards across industries. The right seal can significantly impact the machinery's efficiency, emphasizing the need for industry professionals to stay informed about the latest developments in roller seal technology.
The journey of roller seals, from standard components to high-performance devices, highlights the intersection of engineering expertise and innovative material science. Their evolution is pivotal in the ongoing quest for improved industrial performance, underscoring the necessity for continued research and development in seal technology.
With advances in artificial intelligence and data analysis, the future of roller seals will likely involve smarter designs that can predict wear and failure, enabling proactive maintenance strategies. By adopting seals that incorporate sensor technology, industries can expect even greater reliability and efficiency from their machinery.
In conclusion, roller seals are more than mere components; they are essential contributors to the seamless operation of modern industrial equipment. As technology advances, the role of these seals will continue to expand, solidifying their importance in an ever-evolving industrial landscape.