Rubber lagging for conveyor pulleys represents a key component in the efficient operation of conveyor systems across industries. As an experienced professional in industrial manufacturing, I've witnessed the pivotal role that rubber lagging plays in enhancing productivity, extending equipment life, and ensuring safety in material handling processes.
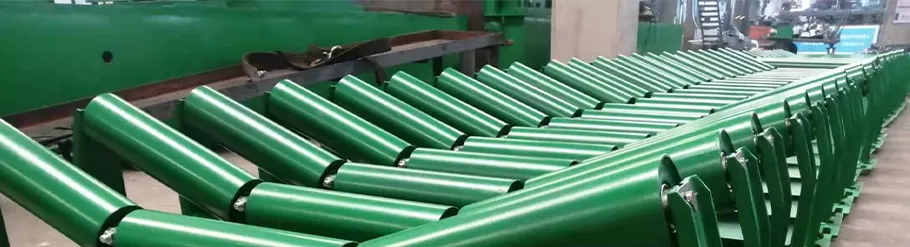
Rubber lagging is critically employed on conveyor pulleys to improve traction, thereby minimizing slippage and wear. This seemingly simple component is engineered with precision, underscoring its importance in heavy-duty applications such as mining, quarrying, and bulk material processing. By providing increased friction between the conveyor belt and the pulley, rubber lagging effectively mitigates the risk of belt misalignment and costly downtime. Engineers who specialize in conveyor system design universally acknowledge the contribution of high-quality rubber lagging to the optimal performance of conveying setups.
When selecting rubber lagging, a discerning focus on material properties and application suitability is paramount. Natural rubber, renowned for its elasticity and abrasion resistance, remains a popular choice for its cost-effectiveness and robust performance in varied industrial environments. Alternatively, for applications requiring heightened resistance to chemicals, extreme temperatures, or oil exposure, synthetic rubbers like Neoprene or EPDM are often recommended. The expertise needed to select and apply the appropriate type of rubber lagging is vital, and collaborating with an experienced engineer can significantly influence operational success.
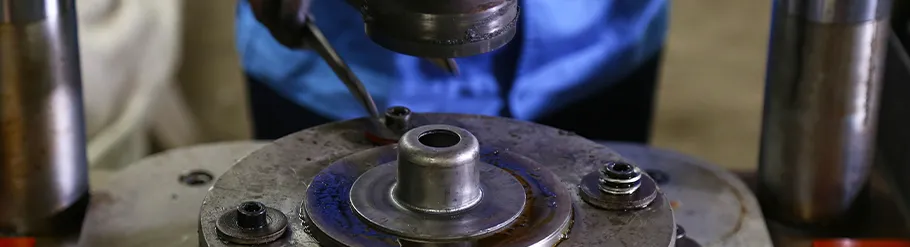
Installation of rubber lagging requires technical precision, reinforcing the notion that expertise in this field is indispensable. When improperly installed, rubber lagging can contribute to premature wear or system inefficiencies. In contrast, expertly installed rubber lagging can dramatically increase the longevity and efficiency of a conveyor system. The process typically involves precision bonding of the lagging material to the pulley, utilizing adhesives or vulcanization techniques that ensure durability under stress. High-quality lagging combines craftsmanship with cutting-edge engineering, demonstrated by its impeccable performance even under demanding operational conditions.
rubber lagging for conveyor pulley
Authoritativeness in the field of rubber lagging is evidenced by industry standards and certifications that guide best practices. Internationally recognized standards, such as those set forth by the International Organization for Standardization (ISO), delineate the specifications for materials, hardness, and installation procedures that maintain safety and efficiency. Compliance with these standards not only reinforces the trustworthiness of a manufacturer's products but also guarantees the safety of the conveyor system as a whole. Regular audits and certifications ensure that rubber lagging solutions remain aligned with evolving industrial requirements and technological advancements.
Trustworthiness in sourcing rubber lagging can be established through a company's proven track record and client testimonials. A manufacturer that prioritizes quality control, offers comprehensive warranties, and provides post-installation support is indispensable for businesses relying on continuous operation of conveyor systems. Trust, fortified through clear communication and consistent product performance, blossoms from a commitment to surpassing client expectations with every conveyor pulley solution provided.
The ongoing advancements in rubber lagging technology are a testament to its enduring relevance and unmatched value in industry. Innovations such as ceramic-infused rubber lagging, which offers enhanced wear resistance and grip, exemplify how research and development continue to refine and elevate conveyor technology. These innovations reflect an expert understanding of industry demands, seamlessly blending endurance with precision engineering.
Rubber lagging for conveyor pulleys thus serves as the unsung hero of industrial material handling, embodying a blend of engineering acumen and industrial experience. From selection to installation, its impact is profound, ensuring not just the efficiency of a single pulley but the holistic success of the entire conveyor system. Incorporating these components proficiently and adhering to global standards reinforces a conveyor system's operational integrity, setting a benchmark for safety and excellence in material transportation.