Rubber lagging, a critical component in the industrial sector, plays an invaluable role in enhancing the efficiency and longevity of conveyor systems. For businesses reliant on conveyor operations, understanding the intricacies of rubber lagging is essential not just for operational efficiency but also for safeguarding investments in machinery. Drawing on years of industry insights, this exploration dives into the specific advantages of rubber lagging, emphasizing expertise and trustworthiness.
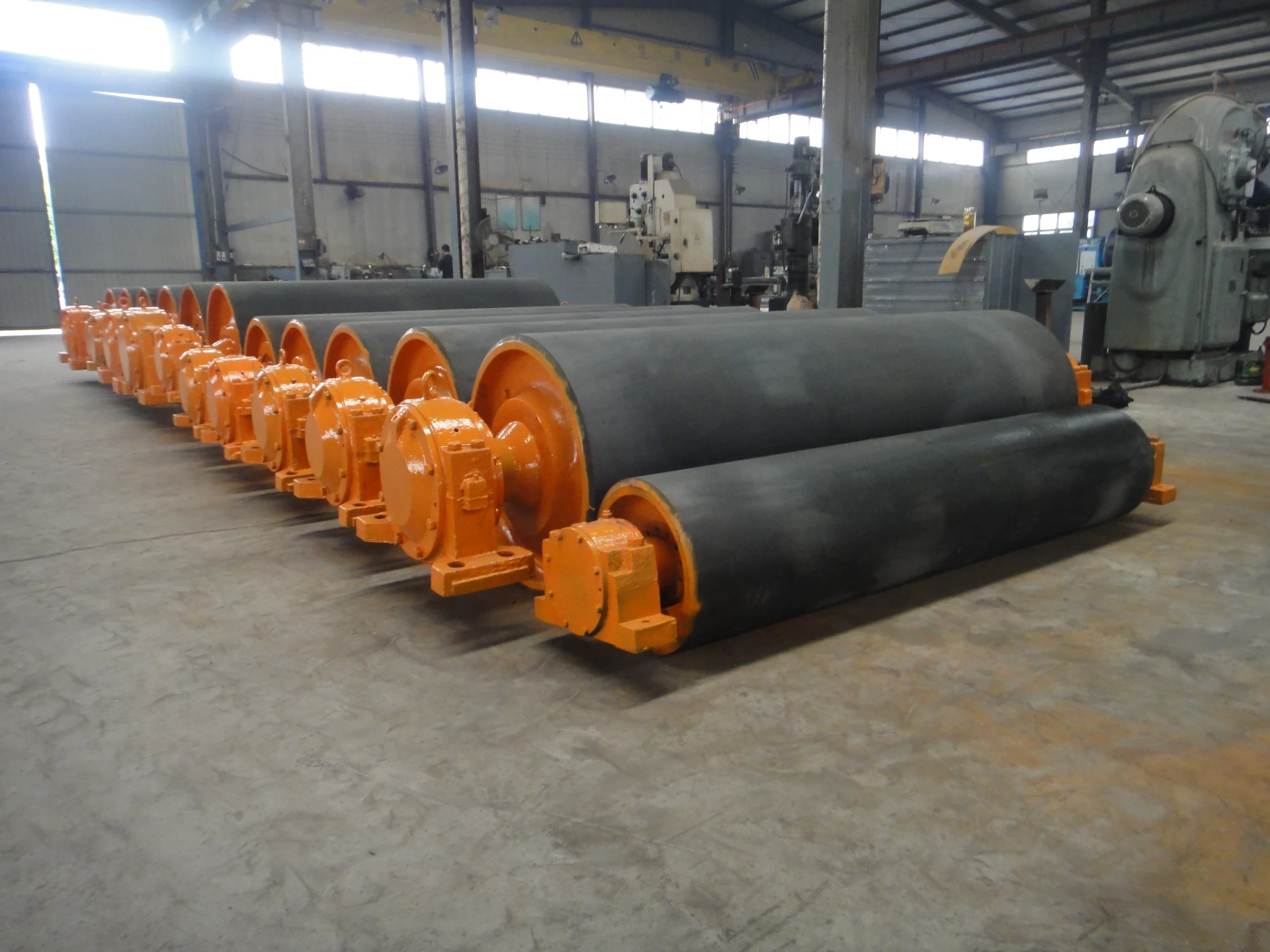
First and foremost, the primary function of rubber lagging is to increase the friction between the conveyor belt and the pulleys, effectively reducing belt slippage. Belt slippage is a common issue in industrial settings that can lead to inefficiencies and even system shutdowns. Businesses that understand this often prioritize the installation of high-quality rubber lagging to ensure uninterrupted operations. Technical expertise in selecting the right rubber compound—whether natural rubber, NBR, or SBR—can further refine this friction-enhancing property, aligning it with specific environmental and operational demands.
In terms of durability, rubber lagging serves as a protective barrier against abrasive materials. While conveyor belts transport a variety of goods, from raw minerals to finished products, the wear and tear caused by abrasive materials can compromise the integrity of the pulleys over time. By serving as a cushioning layer, rubber lagging extends the life of the pulleys—translating into a reduction in both maintenance downtime and replacement costs. This insight is not merely theoretical but is backed by field data showcasing a significant decline in maintenance incidents post-installation of high-grade rubber lagging.
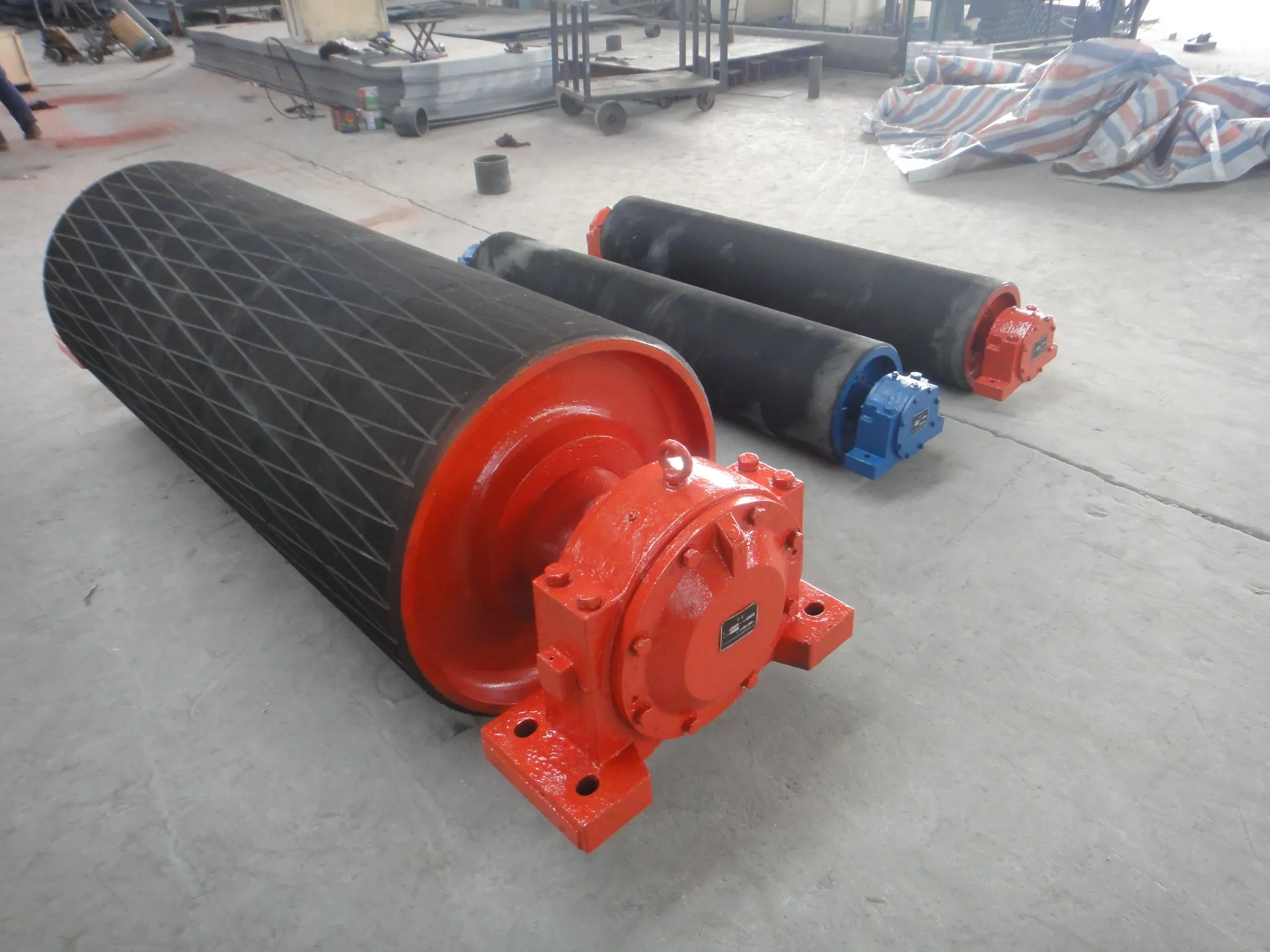
A professional approach to rubber lagging also involves considering environmental factors. For operations in harsh or moist environments, lagging with a high resistance to moisture and temperature variations is crucial. The application of specialized compounds such as Nitrile or EPDM, known for their resilience in oily or extreme conditions, is a testament to the sector’s authority in developing bespoke solutions tailored to specific challenges.
rubber lagging
Furthermore, rubber lagging can also contribute to noise reduction—a growing concern in industries aiming to create more employee-friendly workplaces. By damping vibrations, rubber lagging not only quiets the operation but also reduces wear, providing a dual benefit that underscores the material’s importance. Companies investing in quieter operations often cite employee comfort and improved communication as notable benefits, showcasing the real-world impact of these technical enhancements.
Quality assurance is another critical aspect. Trustworthiness in rubber lagging is often assured through compliance with international standards and certifications. This not only guarantees a baseline of performance but also serves as a reliable metric for companies when selecting suppliers. For industries that cannot afford operational setbacks, choosing a certified product ensures they are investing in reliability and performance.
Ultimately, the role of rubber lagging transcends its apparent functional purpose. Its contribution to operational efficiency, cost-effectiveness, and workplace environment underscores its multifaceted advantages. For businesses aiming for sustainable and efficient operations, integrating rubber lagging into their conveyor systems is not simply an option—it’s a strategic necessity guided by expertise and an unwavering commitment to quality. Through careful selection and application, companies can leverage rubber lagging's full potential, enhancing their operational ethos and strengthening their industrial credibility.