Pulley lagging plays a crucial role in the efficiency and longevity of conveyor systems, a central component in industries ranging from mining to manufacturing. As an expert in this niche, understanding the nuances of pulley lagging can enhance your operational efficiency significantly.
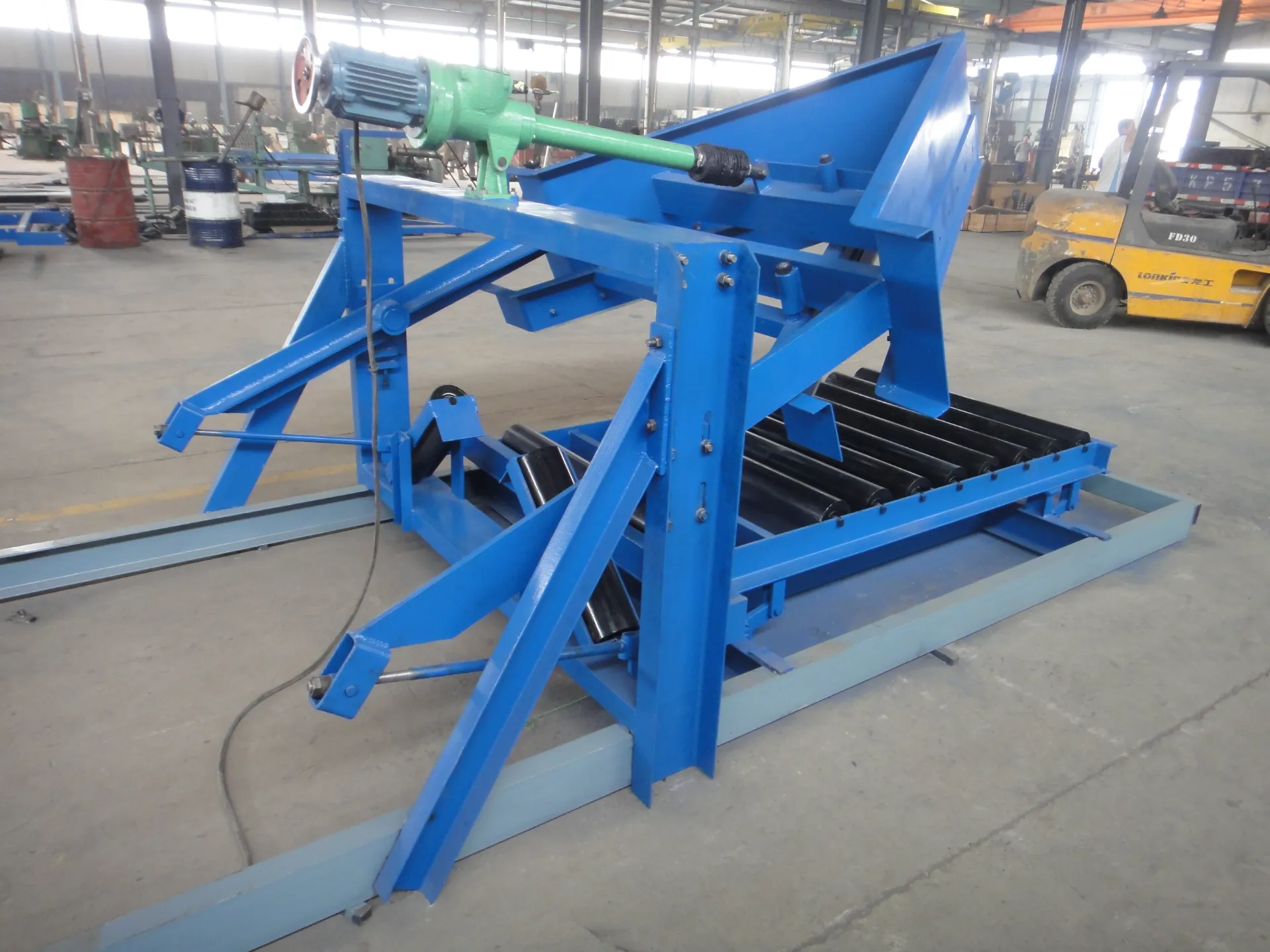
Pulley lagging refers to the application of a material, often rubber or ceramic, to the surface of conveyor pulleys. This not only increases the friction between the belt and the pulley but also extends the lifespan of the belt. With countless hours dedicated to working with conveyor systems, I can attest to the transformative impact of choosing the right pulley lagging.
First, it’s essential to address the experience factor with pulley lagging installations. Prioritizing high-quality materials and precise installation processes ensures that the benefits are maximized. The two most common materials used for lagging are rubber and ceramic, each having its distinct advantages. Rubber lagging is cost-effective and provides excellent grip under a variety of conditions. Ceramic lagging, while more expensive, offers superior resistance to wear and tear, making it ideal for heavy-duty applications. My years in this sector have shown that while both materials are beneficial, the choice depends heavily on specific operational requirements such as load type, environmental conditions, and budget.

Expertise in pulley lagging also involves understanding the diverse types of lagging patterns available. Each pattern serves a unique purpose; for instance, diamond patterns are widely acclaimed for their excellent grip and minimal slippage even under moist conditions. Conversely, smooth lagging is primarily used where the pulley needs a clean surface to start the belt without excessive resistance. It's critical to match the pattern to the application to prevent premature wear and excessive maintenance.
Authoritativeness in this field also comes from staying updated with innovations in lagging materials and techniques. Recent advancements have introduced flame-resistant ceramic laggings that cater to mining operations, where safety is paramount. Moreover, the development of synthetic rubber compounds that offer enhanced thermal resistance has broadened the applicability of rubber lagging in high-temperature environments. Making informed decisions by consulting with manufacturers and keeping abreast of the latest research has been one of the hallmarks of my professional practice in conveyor system maintenance.
pulley lagging
Trustworthiness in your approach can be established by employing only certified professionals for installations and regularly conducting performance audits. Regular checks are crucial; they ensure that the lagging maintains its integrity and the system operates smoothly without unexpected downtime. My recommendation, based on extensive practice, is to conduct comprehensive inspections every three months and replace the lagging preemptively if any signs of wear appear. This not only prevents sudden breakdowns but also ensures optimal performance over extended periods.
Conveyor efficiency heavily relies on the appropriate application of pulley lagging, and mastery of this aspect reflects in reduced operational costs and enhanced system reliability. The right lagging choice considerably enhances friction, protects the conveyor belt from undue stress, and contributes to a more sustainable operating environment through durability and performance stability.
As we look toward future developments, the eco-friendly composition of lagging materials is gaining traction. The industry's move toward greener solutions indicates a gradual shift from traditional materials to those that reduce environmental impact without compromising performance. Professionals who anticipate and adapt to these changes will likely lead advancements in conveyor system management.
In conclusion, whether you're looking to increase the durability of your conveyor system, reduce maintenance costs, or enhance operational safety, comprehending the intricacies of pulley lagging is indispensable. A tailored approach, relying on expertly selecting and maintaining the appropriate lagging, hedges against inefficiencies and extends the life of essential conveyor components. With this understanding, enterprises can significantly bolster their productivity and operational resilience.