In the world of mechanical engineering and automotive design, attention to small details often makes a significant impact on the overall performance of a system. One component that often goes unnoticed but plays a crucial role in the smooth functioning of machinery is the idler bearing housing. This seemingly modest part can determine the longevity and efficiency of various mechanical systems, ensuring optimal performance.
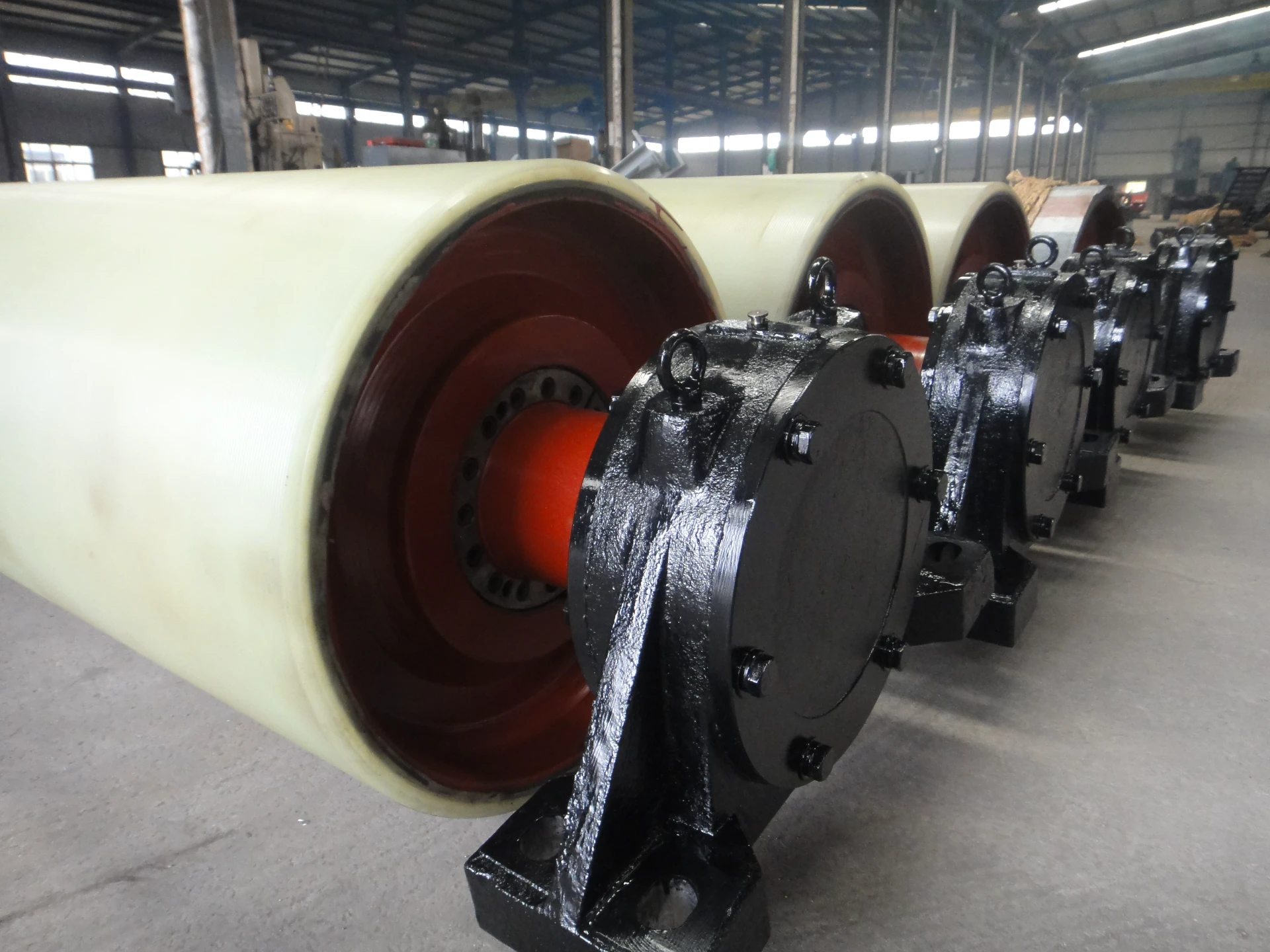
An idler bearing housing serves as the support structure for idler bearings, which are used mainly to guide and maintain tension in belts and chains within machines. These housings are impeccably designed to withstand various operational stresses, ensuring that the bearings and the connected components work without unnecessary friction or misalignment. Key industries where idler bearing housings are pivotal include automotive, aerospace, and manufacturing, where reliability and precision are non-negotiable.
One of the standout features of idler bearing housings is their material composition. Often constructed from high-grade metals like stainless steel or heavy-duty plastics, these housings must strike a perfect balance between strength and weight. The choice of material impacts not just the functionality but also the durability and maintenance needs of the entire assembly. Stainless steel, for example, offers robust protection against corrosion and wear,
making it ideal for harsh industrial environments.
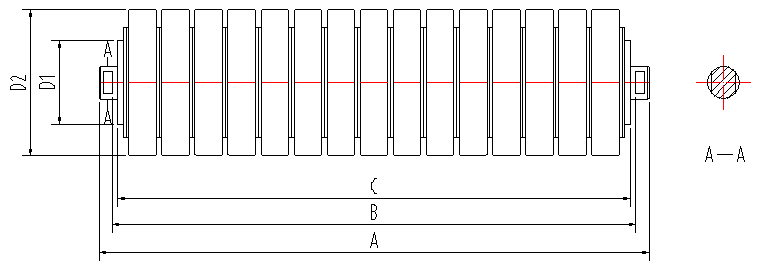
When choosing an idler bearing housing, one must consider the operational environment. For applications involving high-speed machinery, housings must be designed to dissipate heat effectively to prevent overheating, which can lead to premature failure of the bearings. An advanced design might incorporate fins or channels to facilitate air flow and cool the system naturally, or include provisions for lubricant dispersal to further reduce friction and heat.
Precision engineering in the manufacture of idler bearing housings is paramount. Advanced techniques such as CNC machining ensure that each housing meets tight tolerances, a critical aspect that influences the bearing’s lifespan and performance. The slightest deviation can lead to misalignment, causing vibrations that could disrupt the operation of the entire machine. Thus, manufacturers must adhere to strict quality control protocols to guarantee that each unit is flawless.
idler bearing housing
For engineers and maintenance professionals, understanding the nuances of idler bearing housings is crucial. Not only does it involve selecting the correct type and material, but it also requires knowledge of installation best practices. Proper alignment during installation can prevent undue stress on the system, significantly extending the service life of both the bearings and the housing. Regular inspection for signs of wear and tear can pre-empt costly repairs, maintaining operational efficiency and safety.
Sustainability is also an emerging trend in the design and application of idler bearing housings. With environmental issues taking center stage, there is a growing demand for components that minimize energy consumption. Innovative design modifications such as adopting lighter materials and improved aerodynamic shapes can lead to reduced energy usage. Additionally, new coatings and surface treatments are being developed to prolong the operational life of these housings, thereby reducing the frequency of replacements and the associated waste.
Collaboration among manufacturers, engineers, and end-users is essential to push the boundaries of what idler bearing housings can achieve. Sharing insights and experiences contributes to developing industry standards that optimize performance while considering safety and environmental impact. Such collaborative efforts can lead to bespoke solutions tailored for specific industry needs, enhancing productivity and reliability.
In conclusion, idler bearing housings, while often overlooked, are a linchpin in ensuring the seamless operation of myriad machines across different sectors. Their design and application require a profound understanding of materials, mechanics, and maintenance, emphasizing the importance of expertise and precision. As technology advances, the potential for these components to become even more efficient and sustainable grows, promising a future where machinery operates with even greater efficacy and minimal environmental footprint.