Plastic pipe rollers have revolutionized the way industries handle, install, and maintain piping systems. These essential components, often overlooked, play a pivotal role in ensuring the smooth operation of industrial processes, reducing installation time, and minimizing maintenance costs. As industries increasingly turn towards automation and efficiency, understanding the benefits, applications, and innovations in plastic pipe rollers is crucial for businesses aiming to optimize their operations.
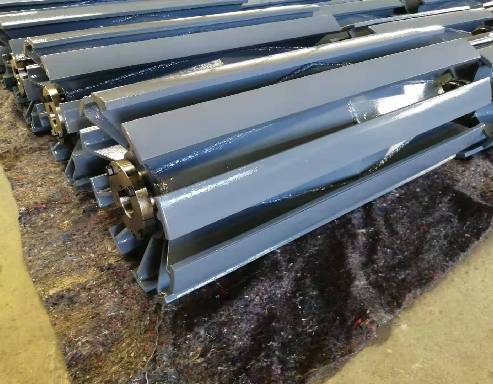
Plastic pipe rollers, primarily made from high-density polyethylene (HDPE) or similar robust polymers, offer several advantages over traditional metal rollers. One of the most significant benefits is their non-corrosive nature. Unlike metal rollers, which can rust or degrade in harsh environments, plastic rollers maintain their integrity, providing long-lasting performance even in corrosive environments such as chemical plants or maritime applications. This longevity not only reduces the frequency of replacements but also saves on maintenance costs, making them a cost-effective solution for businesses.
Furthermore, plastic pipe rollers are lightweight yet remarkably strong. Their low weight facilitates easier handling and installation, significantly reducing labor costs and time. This characteristic is particularly beneficial in large-scale projects where efficiency is paramount. Additionally, the strength of these rollers ensures they can support substantial loads, making them suitable for a wide range of piping systems, from small-scale residential plumbing to expansive industrial pipelines.
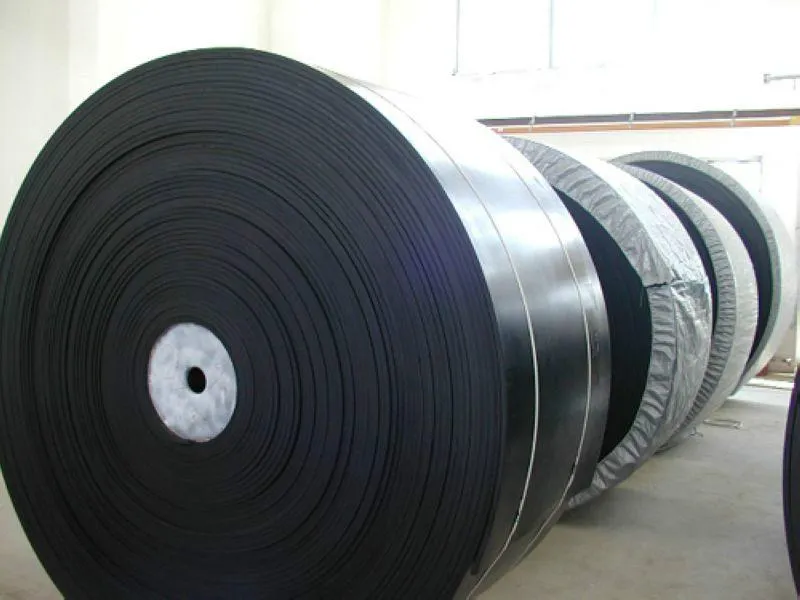
The versatility of plastic pipe rollers extends to their compatibility with various pipe materials. Whether working with PVC, steel, copper, or composite pipes, plastic rollers provide a smooth, low-friction surface that allows for seamless movement. This feature is essential in applications where pipes need to be regularly adjusted or replaced, as it minimizes drag and potential damage to the pipes.
In terms of innovation, recent advancements have seen the introduction of customizable plastic pipe rollers. These state-of-the-art models can be tailored to meet specific project requirements, whether through adjustments in size, load capacity, or the integration of specialized surface treatments to enhance durability. Such customization ensures that businesses can deploy solutions precisely aligned with their operational needs, optimizing performance and extending the lifespan of their infrastructure.
plastic pipe rollers
Expertise in the design and manufacturing of plastic pipe rollers is critical for ensuring they meet the rigorous demands of industrial applications. Manufacturers typically employ refined engineering processes, utilizing advanced CAD software and precision molding techniques to create rollers with exacting specifications. This precision engineering guarantees that each roller not only fits perfectly within its designated application but also provides consistent performance under varying conditions.
Authoritativeness in the field of plastic pipe rollers is often demonstrated by the adoption of industry standards and certifications. Leading manufacturers subject their products to rigorous testing, adhering to international standards such as ISO and ANSI to verify their reliability and safety. Such certifications provide consumers with the assurance that their chosen rollers have undergone thorough evaluation and meet the highest quality benchmarks.
Trustworthiness is further enhanced through transparent customer engagement and robust after-sales support. Companies known for their plastic pipe rollers often emphasize the importance of client education, offering detailed usage guides, maintenance tips, and troubleshooting advice. Additionally, they provide comprehensive warranties and easy access to replacement parts, ensuring long-term customer satisfaction and peace of mind.
Testimonials from industry professionals highlight the transformative impact of plastic pipe rollers on various projects. Consider the case of a major infrastructure company tasked with installing a new sewage system in a coastal city. The use of HDPE plastic pipe rollers facilitated the rapid and smooth installation of large-diameter pipes across challenging terrain, resulting in the project being completed ahead of schedule and under budget.
In summary, plastic pipe rollers offer a combination of durability, versatility, and cost-effectiveness that is unmatched by traditional materials. Their non-corrosive nature, coupled with their strength and lightweight design, make them indispensable in both longstanding and emerging industries. As technology advances, the potential for innovation in plastic pipe rollers grows, promising even greater efficiency and reliability in pipeline management. For businesses seeking to enhance their operational capacity, investing in high-quality, expertly manufactured plastic pipe rollers is a strategic decision that promises substantial returns in both performance and cost savings.