In the manufacturing and materials handling industries, roller lagging stands as a critical component for improving the performance and lifespan of conveyor systems. This article explores the nuances of roller lagging, anchoring its relevance in real-world applications to provide a comprehensive understanding.
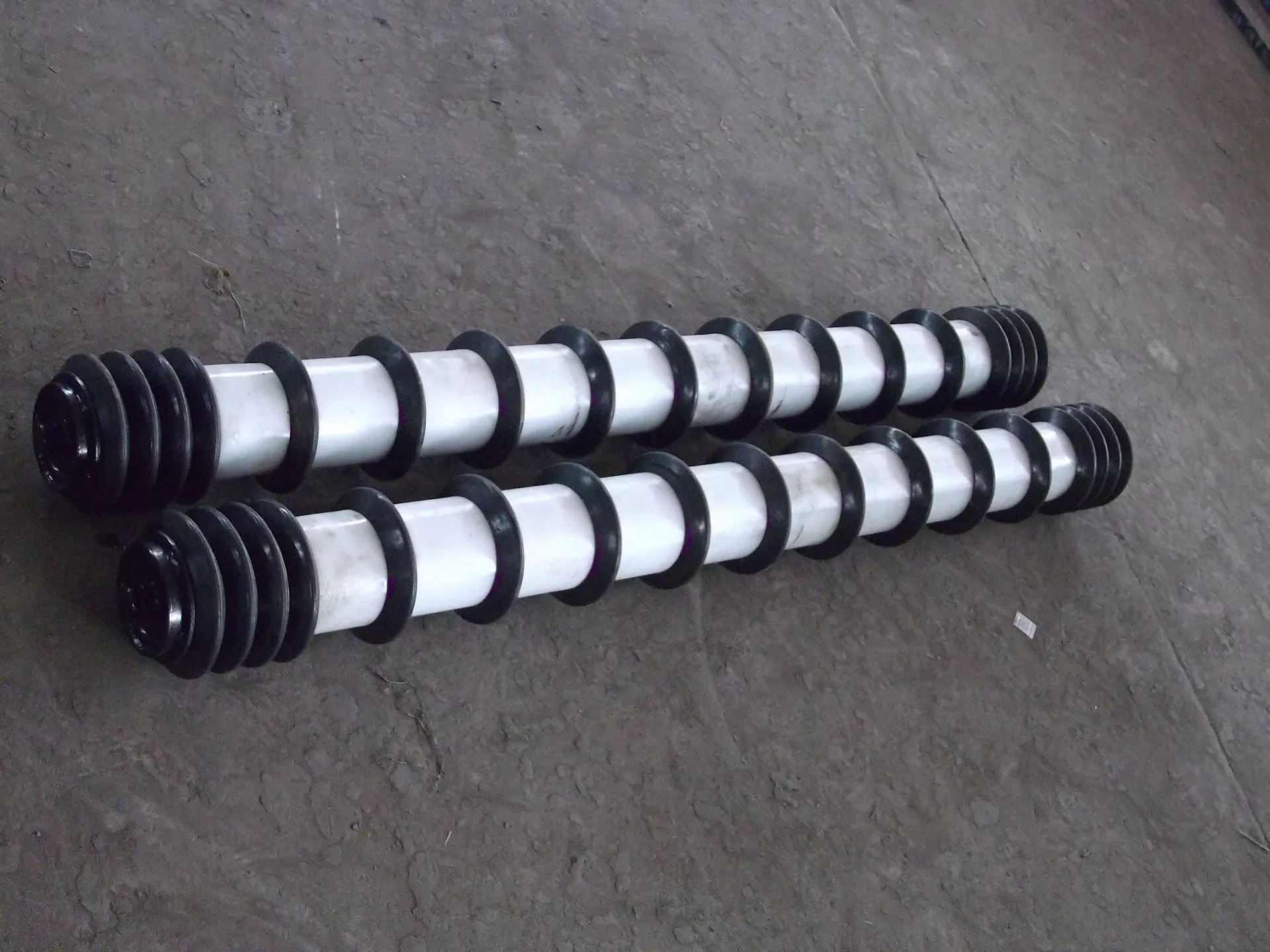
Roller lagging refers to the application of a cover to conveyor rollers to enhance their traction abilities and prolong the conveyor's lifespan. The process is integral in reducing slippage between the conveyor belt and rollers, thereby increasing operational efficiency and reducing downtime.
Experience in Roller Lagging Applications
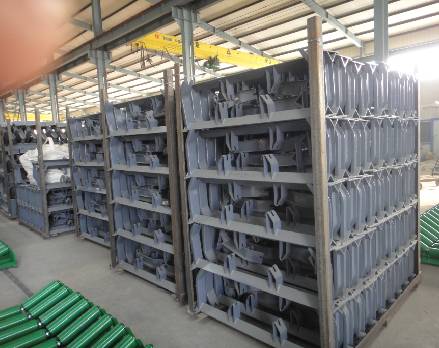
Across industries like mining, agriculture, and logistics, users consistently report significant performance improvements following the installation of roller lagging. A logistics company based in the Midwest, for example, attributes a 30% reduction in unscheduled maintenance to the strategic use of roller lagging on its high-capacity conveyors. Similarly, a mining operation in Australia noted a considerable decline in belt wear and maintenance after switching to a high-grade ceramic roller lagging, which provided the necessary grip and abrasion resistance in harsh, abrasive conditions.
Expert Insights on Material Selection
When discussing expertise in the sector, it is crucial to focus on the materials used for roller lagging. Natural rubber remains popular for applications requiring flexibility and noise reduction, while ceramic lagging excels in providing superior abrasion resistance in heavy-duty environments. Noteworthy is the advent of new composite materials that combine polymers with embedded ceramic beads, offering both flexibility and enhanced grip.
Industry specialists emphasize the importance of selecting the correct material based on the specific operational conditions. The wrong choice can lead to premature wear and increased operational costs. For example, in environments where moisture is prevalent, rubber lagging with a chevron or diamond groove pattern offers superior grip over smooth surfaces, preventing belt slippage.
roller lagging
Authoritative Guidelines for Installation and Maintenance
Authoritativeness in roller lagging installation and maintenance stems from adherence to industry standards and guidelines set forth by organizations like CEMA (Conveyor Equipment Manufacturers Association). Proper installation is not only a matter of following step-by-step procedures but also understanding the nuances of tension and pressure settings that influence the overall effectiveness of the lagging.
Industry leaders recommend a professional installation to ensure the integrity of roller alignment and belt tension.
Moreover, regular maintenance checks are critical. Parameters such as tension, lagging wear, and conveyor alignment need to be monitored closely. Companies often deploy integrated monitoring systems that use sensors to track wear patterns in real-time, thereby preemptively addressing potential failures.
Trustworthiness Through Demonstrated ROI
The trustworthiness of roller lagging is anchored in demonstrated ROI (Return on Investment) metrics. Data from case studies highlight scenarios where companies observed up to a 200% return through prolonged equipment life and reduced energy consumption. One notable case involved a manufacturing plant that reported a 40% decrease in energy costs after installing energy-efficient roller lagging paired with optimized belt tensioning systems.
Furthermore, environmental safety practices, such as using lagging materials that are resistant to a range of temperatures and chemicals, boost the trust factor for industries handling hazardous materials. The use of eco-friendly adhesives and heat-resistant materials underscore the commitment to sustainability, a crucial element in today's eco-conscious industry landscape.
Overall, roller lagging is not merely a protective measure but a strategic investment to maximize conveyor efficiency and extend longevity. The integration of innovative materials, adherence to authoritative practices, and the positive impact on a company’s bottom line collectively make a compelling case for its widespread adoption across industries. As conveyor technology continues to evolve, the role of roller lagging will likely expand, promising even greater efficiencies and advancements in operational capabilities.