Hot vulcanized pulley lagging stands at the forefront of innovation in the field of conveyor belt systems, promising enhanced performance and reliability that set it apart from traditional methods. This advanced technique involves applying a vulcanized rubber layer directly onto the pulley, creating an integrated bond that significantly enhances the pulley’s frictional properties, reduces slippage, and extends its lifespan.
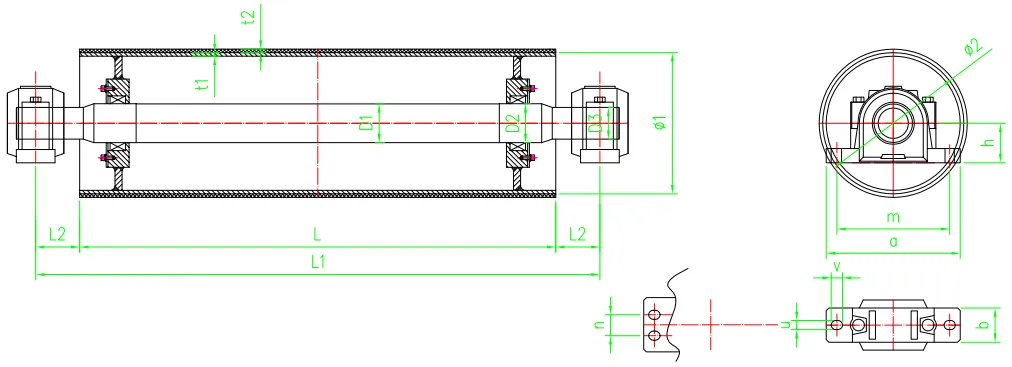
From an experiential standpoint, industries across various sectors, including mining, agriculture, and manufacturing, have reported outstanding improvements in operational efficiency following the implementation of hot vulcanized pulley lagging. The direct vulcanization process ensures that the lagging adheres with unmatched strength, eliminating the peeling and material degradation commonly associated with glued methods. Users have noted not only a marked decrease in downtime due to maintenance needs but also a tangible boost in conveyor belt throughput, as optimal tension and alignment are consistently maintained.
From an expertise angle, hot vulcanized pulley lagging represents a synthesis of material science and engineering expertise. Specialists in the field understand that the quality of the vulcanization process is critical - it requires precise temperature control, skilled handling, and thorough preparation of pulley surfaces to achieve peak effectiveness. The rubber compounds used are meticulously formulated to resist wear and abrasion, handling high temperatures and harsh environmental conditions without compromising integrity. This expertise in material selection and process perfection ensures that hot vulcanized lagging remains a superior choice for demanding industrial applications where reliability is paramount.
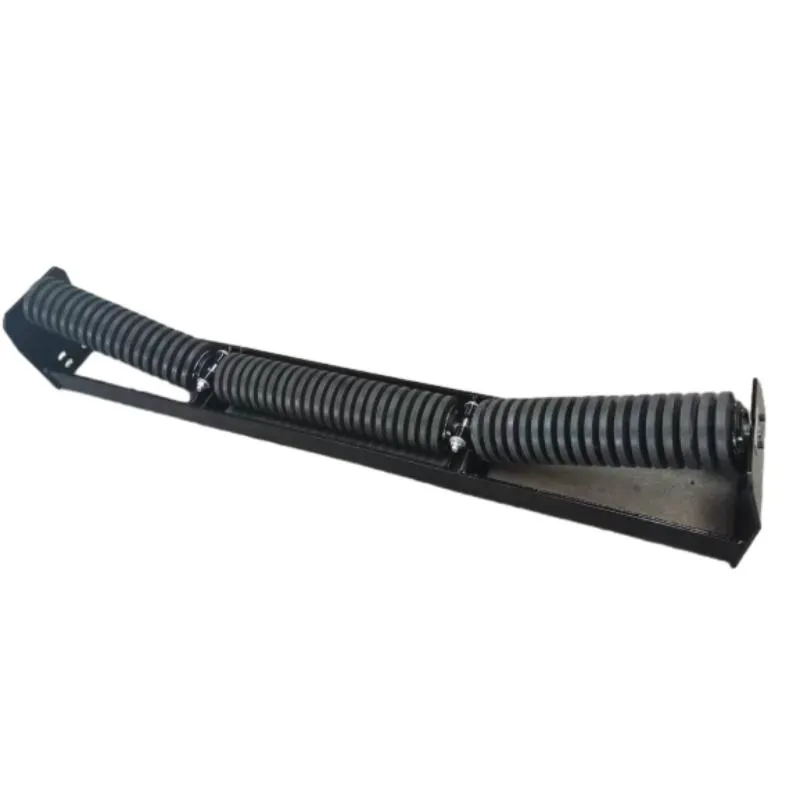
hot vulcanized pulley lagging
The authoritativeness of hot vulcanized pulley lagging is bolstered by its adoption among leading corporations who prioritize efficiency and innovation. Case studies and published reviews consistently underscore its superior performance metrics compared to cold bonding alternatives. Industry experts advocate for its use in scenarios where the cost of conveyor downtime is significantly higher than the initial investment in upgraded lagging solutions. The seamless integration and zero-gap finish of hot vulcanized lagging are frequently highlighted in technical forums and trade publications, lending further credibility to its status as a preferred choice for modern material handling systems.
Trustworthiness is deeply embedded in the track record of service life improvements and reduced total cost of ownership that hot vulcanized pulley lagging delivers. Clients who have transitioned to this method report significant cost savings over time, thanks to the reduction in emergency interventions and scheduled maintenance. This reliability assures stakeholders that opting for hot vulcanized pulley lagging equates to a measured, strategic enhancement of their conveyor operations. Trust is also reinforced through warranties offered by manufacturers, who stand by their product's longevity and performance, allowing operational managers to plan with confidence.
In summary, hot vulcanized pulley lagging offers a compelling mix of experience-driven results, expert-led innovations, authoritative endorsements, and trustworthy performance assurances. Its ability to transform operational efficiencies makes it an indispensable upgrade for conveyor systems where safety, speed, and cost-effectiveness are critical. As technology progresses and industrial demands evolve, hot vulcanized pulley lagging continues to lead in delivering cutting-edge solutions that propel productivity forward.