Herringbone rubber lagging, a staple in various industrial applications, has gained popularity for enhancing conveyor system efficiency. Whether you're involved in mining, agriculture, or logistics, the importance of reliable conveyor operation cannot be overstated.
Herringbone rubber lagging promises to meet these demands with precision and efficacy.
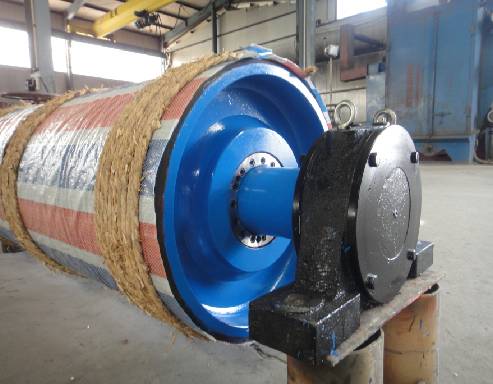
Understanding the application of herringbone rubber lagging begins with recognizing its structure and benefits. The herringbone pattern, resembling the bones of a fish, ensures maximum grip and minimizes slippage. This unique configuration is particularly advantageous for conveyors operating under harsh conditions, where maintaining friction is paramount. Unlike traditional flat lagging, the angular, v-shaped grooves of herringbone lagging are strategically designed to repel water and debris, minimizing downtime due to maintenance.
Industries facing challenges like moisture and contamination will appreciate the robustness that herringbone rubber lagging provides. In agricultural settings, for instance, the transportation of grain and fertilized earth often encounters environmental elements that can alter conveyor performance. Here, the self-cleaning characteristics of the herringbone pattern are indispensable. By ensuring materials are effectively transported without clumping or sticking, operational efficiency is upheld.
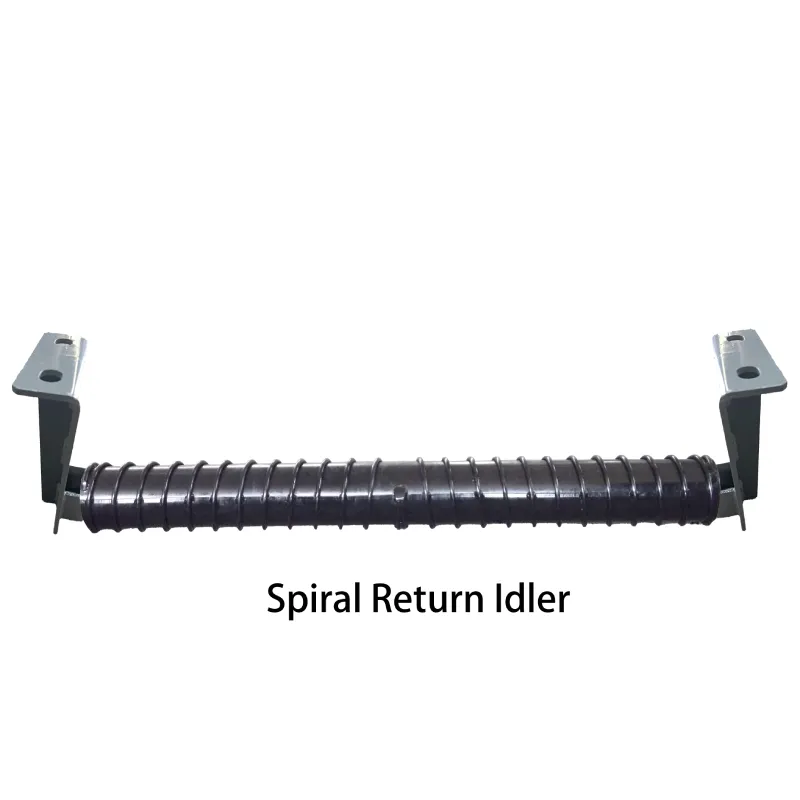
Moreover, expert analysis highlights that businesses utilizing herringbone rubber lagging report noticeable reductions in energy consumption. By optimizing grip and reducing slippage between the belt and pulley, conveyors require less energy to maintain movement, thus contributing to significant cost savings over time. This energy efficiency not only lowers operational costs but also aligns with sustainable practices by reducing overall carbon footprint.
The expertise of specialists in manufacturing high-quality herringbone rubber lagging cannot be overlooked. This product’s effectiveness heavily depends on the precision engineering and material composition. High-grade rubber compounds used in the lagging confer resilience against abrasion and wear, extending the lifespan of conveyor systems. Selecting a reputable supplier is crucial, as their commitment to quality assurance and thorough testing protocols ensures that lagging meets industry standards in durability and performance.
herringbone rubber lagging
Authoritativeness on the subject is backed by studies and case analyses conducted across various sectors. A mining operation in Australia, for instance, implemented herringbone rubber lagging and noted a 30% improvement in conveyor belt life. This kind of statistical data provides a compelling narrative for companies considering transitioning to or upgrading their conveyor lagging systems.
Trustworthiness comes from transparency and shared experience. Companies that have transitioned to using herringbone rubber lagging often share testimonials highlighting their journey. From initial skepticism to proven outcomes, these stories fortify trust in the product’s capability and potential benefits. Consulting with industry experts and reading comprehensive reviews contribute to an informed purchasing decision, cutting through marketing jargon to focus on tangible results.
Incorporating herringbone rubber lagging requires an understanding of the specific needs and conditions of the operating environment. Proper installation and ongoing maintenance play critical roles in maximizing the benefits of this technology. It is advisable to engage experienced technicians for installation to ensure the alignment and tension are optimized, which directly impacts the overall efficiency and longevity of the system.
For enterprises looking to integrate herringbone rubber lagging into their conveyor systems, ongoing education and updates on technological advancements are crucial. Attending industry conferences, partaking in workshops, and collaborating with experts in rubber technology can provide insights into future trends and innovations that could further benefit operations. Staying ahead in the competitive landscape calls for continuous learning and adaptation.
In conclusion, herringbone rubber lagging stands as a testament to innovation within the industrial sector, providing reliable solutions to longstanding challenges in conveyor system management. When selected and implemented correctly, it not only enhances operational efficacy but also aligns with modern sustainability goals. As businesses strive to optimize productivity, investing in such technology becomes not just a choice but a necessity.