The world of conveyor systems is broad, encompassing various components that work in unison to ensure efficient material handling. Among these components, the head pulley and tail pulley stand out as indispensable elements pivotal to the system’s performance and reliability.
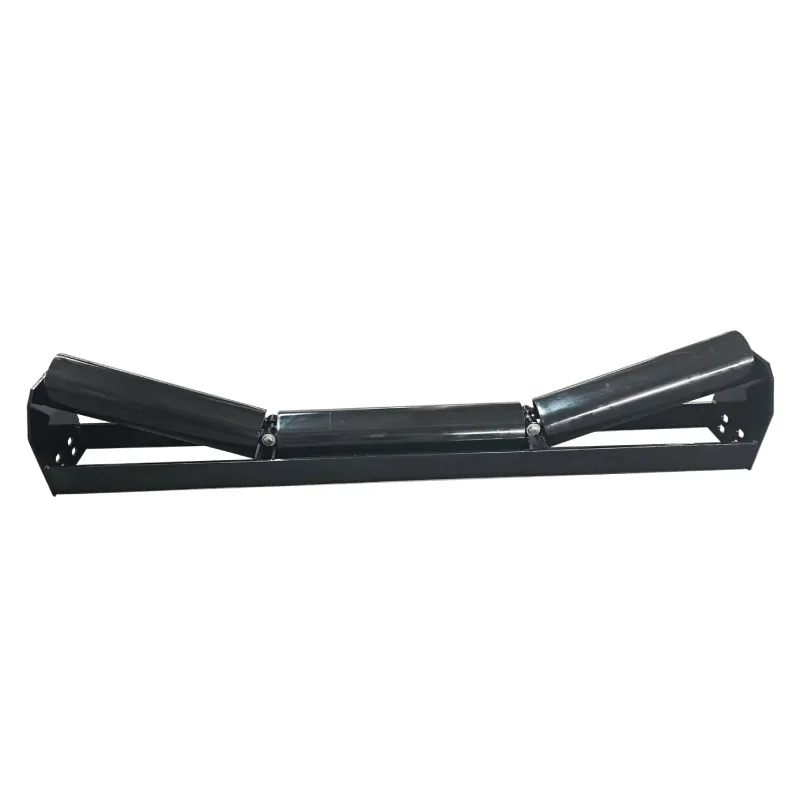
The head pulley is the driving force of the conveyor belt system, situated at its discharge point. Typically motor-driven, this pulley plays a crucial role in imparting motion to the belt, facilitating the smooth transport of materials from one point to another. Made from materials such as heavy-duty steel, the head pulley is often covered with rubber or ceramic lagging to enhance friction with the belt, preventing slip and extending the life of both the belt and pulley. The choice of material and construction quality directly impacts the head pulley’s effectiveness and durability. Expertise suggests that incorporating a high-friction coating enhances operational efficiency, especially in environments with high moisture or dust, where slippage is a common issue.
Conversely, the tail pulley, positioned at the loading end of the conveyor, serves as an idler to redirect the belt back towards the head pulley. Though it may not be involved in driving the belt, its importance is no less significant. The tail pulley provides tension in the system, ensuring that the belt operates under sufficient tension to prevent sagging and maintain alignment. Precision in the alignment of the tail pulley is critical; even slight misalignment can lead to issues like belt wander or accelerated wear, ultimately compromising the entire conveyor system’s integrity. Professional insights stress the use of self-cleaning tail pulleys in environments dealing with bulk materials, as they efficiently prevent material build-up, which could otherwise lead to belt misalignment or damage.

Addressing the need for both reliability and performance, strategic choices regarding the configuration and maintenance of the head and tail pulleys become paramount. Regular maintenance, including the inspection of lagging and the alignment of both pulleys, becomes essential for minimizing unscheduled downtime and ensuring consistent operation. Utilizing advanced condition monitoring technologies can proactively identify potential issues before they lead to significant malfunctions, thereby increasing the system's trustworthiness.
head pulley tail pulley
Engineers and industry experts emphasize the interconnected nature of the head and tail pulleys with other conveyor components. Their design should not only focus on individual performance but also compatibility with the overall conveyor system. For facilities handling materials with abrasive properties, selecting pulleys with wear-resistant surfaces could significantly prolong equipment life and reduce maintenance costs.
When establishing a conveyor system, the choice of head and tail pulleys should align with the specific operational requirements, considering factors such as load weight, speed, and environmental conditions. Authoritative sources recommend consulting with conveyor system specialists during the design phase to ensure a bespoke solution that maximizes productivity and safety.
In essence, the role of the head pulley and tail pulley transcends their mechanical functions, extending into realms of operational strategy and system reliability. A thorough understanding of their operational dynamics, paired with professional maintenance practices, assures that these components contribute positively to achieving seamless and efficient material handling operations. The complex interplay of design, material selection, and ongoing management underscores their critical placement in the broader narrative of conveyor technology advancement.