In the complex world of conveyor systems, the head pulley plays a pivotal role in ensuring efficient material handling. A head pulley, often referred to as the drive pulley, is responsible for the movement of the conveyor belt and the materials it carries in industries ranging from mining to manufacturing. With its fundamental role in conveyor systems, understanding the intricacies of head pulleys is essential for optimizing the reliability and performance of your conveyor setup.
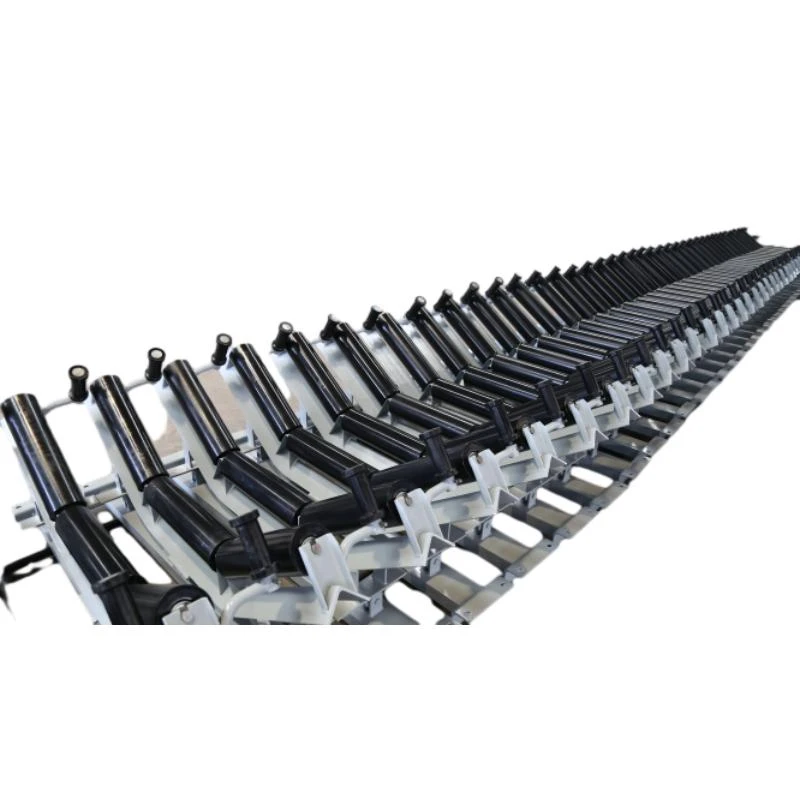
The head pulley is typically located at the discharge end of the conveyor, responsible for driving the belt and determining its speed. It ensures the smooth transition of materials from one process to the next, enhancing productivity and operational flow. Its construction usually involves high-strength materials like steel, designed to withstand significant mechanical stress over extended periods, thereby minimizing downtime and maintaining efficiency.
Experience is a critical factor when considering the implementation and maintenance of head pulleys within conveyors. Skilled technicians with years of hands-on expertise are best equipped to install and maintain these components, ensuring they operate at peak efficiency. The balancing of the pulley and its alignment with the rest of the system are crucial for avoiding premature wear and unexpected system failures, which can be costly.
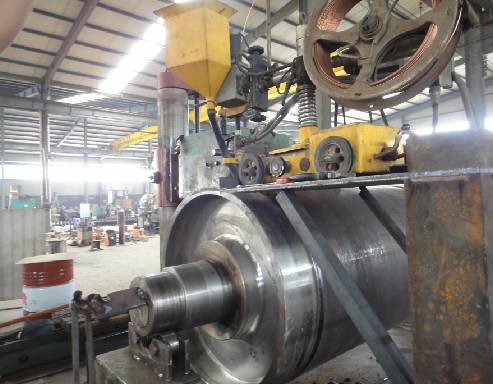
From an expertise viewpoint, understanding the differing types of head pulleys is essential. Crowned pulleys are often used to improve belt tracking, whereas lagged pulleys — covered with a material such as rubber or ceramic — enhance grip and prevent slippage under various conditions. The choice between a crowned or lagged head pulley can profoundly impact the durability and efficiency of the conveyor, as well as maintenance costs over time. Consulting with conveyor system experts and using precise engineering calculations ensures the pulley complements the entire system effectively.
head pulley in conveyor
The authoritativeness in the realm of conveyor component design should not be underestimated. Manufacturers of head pulleys must adhere to industry standards and implement rigorous testing protocols to verify product reliability. The integration of advanced technologies like finite element analysis (FEA) in the design phase allows engineers to predict stress distribution and potential failure points, paving the way for robust and durable products. By sourcing head pulleys from reputable manufacturers with a track record of innovation and adherence to high engineering standards, businesses can trust that their operations will remain uninterrupted.
Trustworthiness is paramount in the supplier relationship for head pulleys. Suppliers should provide comprehensive documentation about product specifications, performance metrics, and installation guidelines. Moreover, offering warranty options and reliable aftersales support builds confidence that any operational challenges will be addressed promptly. Suppliers who actively engage with customer feedback and invest in continuous improvement earn a reputation for dependability.
In conclusion, the head pulley is more than just a component within a conveyor system; it is a critical driver of operational efficiency and productivity in a wide array of industries. The choice and maintenance of the right head pulley, supported by experience and expertise, can significantly affect the long-term success of a conveyor installation. Partnering with authoritative and trustworthy manufacturers ensures that businesses maximize the return on their investment, bolstering their competitive edge in the demanding landscape of material handling.