In the world of conveyor systems, the head pulley plays a critical role in ensuring efficient and smooth operation. As one of the pivotal components, understanding the nuances of head pulleys can lead to enhanced performance and longevity of conveyor systems. Through years of experience and meticulous expertise, industries have continued to evolve their understanding and application of head pulleys, making them not only essential but also a point of focus for those striving for conveyor excellence.
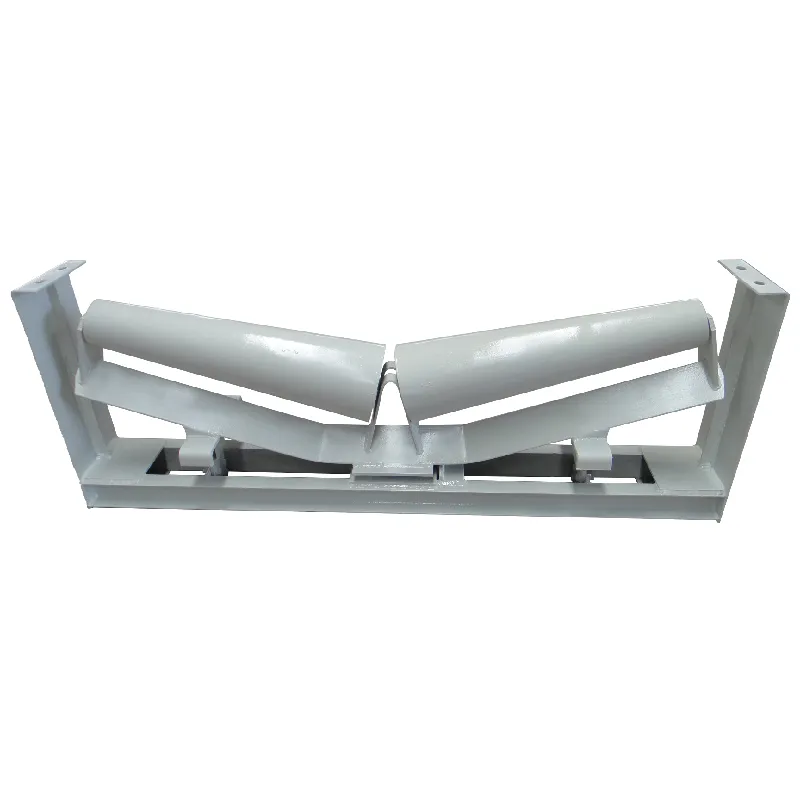
A head pulley is located at the discharge end of a conveyor belt and is responsible for the movement and direction of the belt. It serves as the drive pulley, offering the necessary traction to keep the belt running at optimal speed. The importance of a head pulley cannot be underestimated, as it essentially dictates the belt alignment and conveyor performance. The quality and design of the head pulley directly impact the efficiency of material transportation, influencing productivity across various industries.
In selecting the right head pulley, one must consider several critical factors to ensure it aligns with operational goals. Material composition is of utmost importance. Steel is commonly used due to its strength and durability, but for applications where corrosion is a concern, stainless steel or coated surfaces might be more appropriate. Proper selection ensures the head pulley resists wear and prolongs the system's lifespan, making it a sound investment.
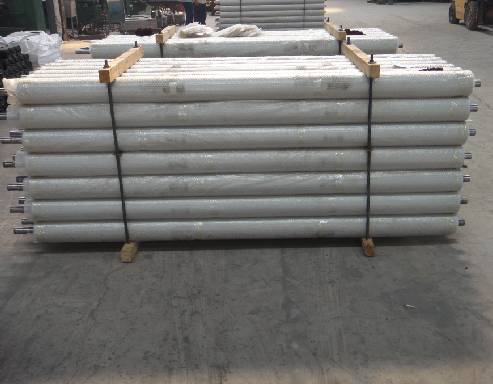
Size and diameter of the head pulley are also vital. A larger diameter can improve the belt's grip and stability, helping to prevent slippage and reduce wear. It's essential to match the size of the pulley with the specific demands of your operation to optimize performance. In addition, crowned pulleys, which are slightly larger in the center, help with belt tracking, reducing the likelihood of misalignment that can lead to costly maintenance and downtime.
head pulley in conveyor
Expertise in installation and alignment cannot be overstated. Misaligned head pulleys can result in substantial operational issues, including uneven wear and stress on the conveyor belt. The alignment process is critical to ensuring the belt runs straight and true. This requires professional skills and precise measurements. Engaging experienced technicians ensures that the installation aligns with the industry best practices, significantly impacting the system's performance and durability.
Routine maintenance and inspection of head pulleys are essential practices to retain their efficiency and functionality. Regular checks can identify potential issues such as signs of wear, misalignment, or belt slippage early on, preventing more severe damage or failure. Leveraging advanced monitoring technologies can also provide real-time insights, allowing for proactive maintenance scheduling. Trustworthiness of the equipment is fortified when a robust maintenance regimen is adhered to, minimizing unexpected downtimes and enhancing reliability.
Authoritative knowledge from leading manufacturers can significantly influence the choice and maintenance of head pulleys. Partnering with reputable suppliers who provide comprehensive guides and support ensures access to the highest quality components and expert advice. They offer a wealth of resources, from technical data sheets to on-site training, empowering teams to optimize their conveyor operations.
In conclusion,
the head pulley is a cornerstone of efficient conveyor system operations. With an in-depth understanding and attention to detail in selection, installation, and maintenance, industries can harness the full potential of their conveyor systems. Investing in high-quality head pulleys and leveraging experienced personnel ensures a seamless and reliable material handling process, ultimately leading to increased productivity and reduced operational costs. Balancing all these factors forms the bedrock of a trustworthy conveyor system, driven by the expertise and authoritative insight that industry veterans and innovative companies offer.