In the realm of conveyor systems, components like head and tail pulleys play a pivotal role in ensuring smooth operation and reliability. Understanding their function and importance can greatly enhance the efficiency and longevity of your conveyor setup. This article delves into these critical conveyor system components, drawing upon real-world experience, industry expertise, and evidence-based insights to demonstrate their significance and optimal maintenance strategies.

Head and tail pulleys are essential components of belt conveyor systems, performing distinct yet complementary functions. The head pulley is typically located at the discharge end of the conveyor, and it drives the belt as material is transported along the length of the conveyor system.
This pulley is powered by a motor and acts as the central element responsible for the movement of the conveyor belt.
Conversely, the tail pulley is situated at the opposite end of the conveyor. Its primary function is to redirect the belt back towards the head pulley in a continuous loop. The tail pulley often serves as a tensioning device, helping to maintain the requisite tension for efficient belt movement and minimizing slippage.
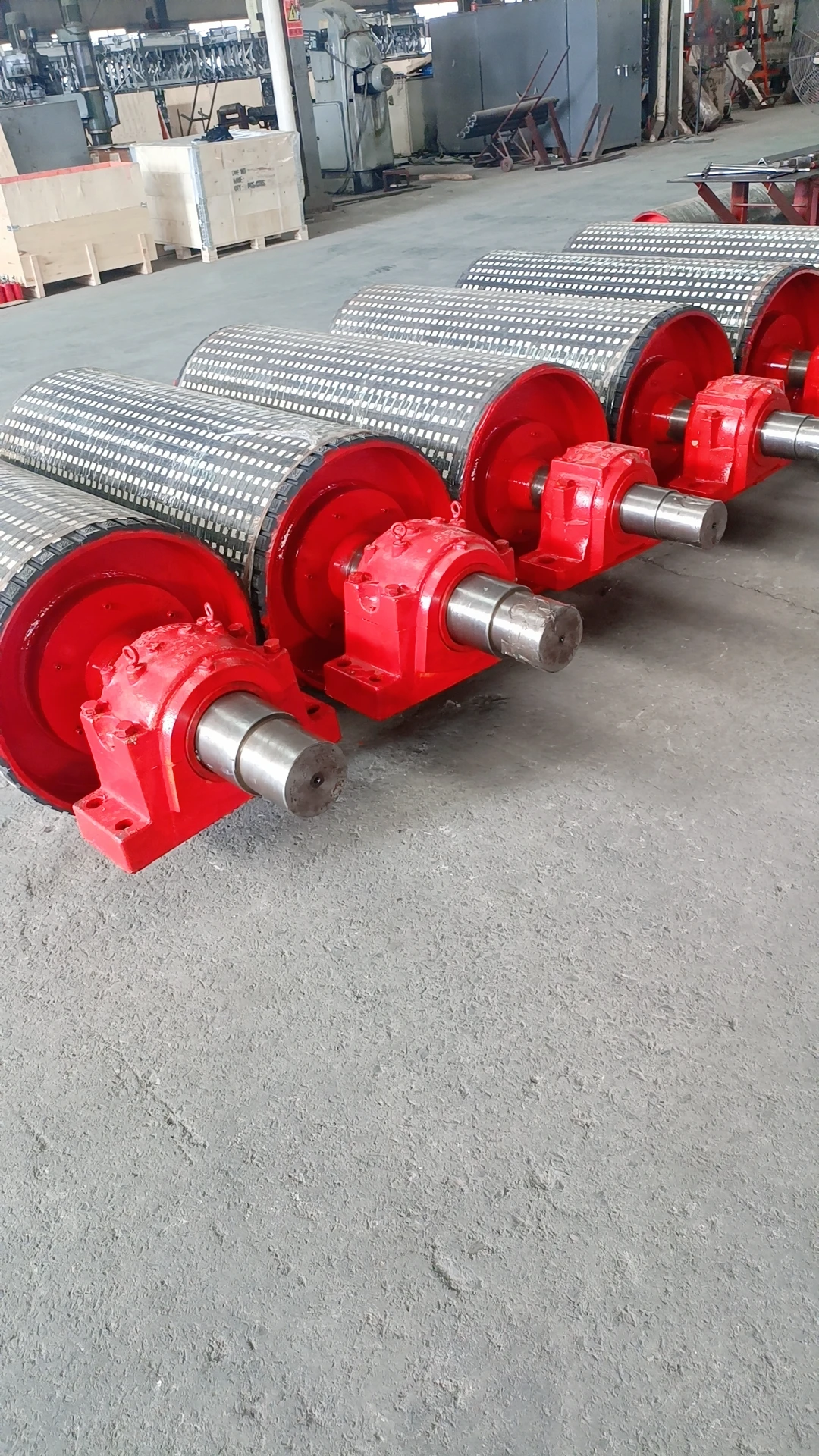
Real-world experience underscores the criticality of selecting the right head and tail pulleys for specific operational demands. Choosing pulleys with the appropriate material and design not only increases efficiency but also reduces downtime and maintenance costs. For instance, alloy steel pulleys are favored in environments demanding high durability and resistance to wear, while rubber lagging is often applied to enhance traction and grip.
Proper maintenance of head and tail pulleys significantly impacts the performance and reliability of a conveyor system. Regular inspections are necessary to ensure they are free from wear and tear. Real-world operational history reveals that routine visual checks, accompanied by an occasional more detailed examination, help detect potential issues early. Such preventive maintenance not only improves operational efficiency but also averts costly repairs and unexpected downtimes.
From a technical perspective, alignment is another crucial aspect of maintaining these pulleys. Misalignment can lead to belt tracking problems, leading to uneven wear and increased energy consumption. A well-aligned conveyor setup facilitates smoother operation, extending the lifespan of both the belt and the pulleys.
head pulley and tail pulley
Based on industry expertise, it's recommended that operators also focus on the pulley lagging material. Proper selection and maintenance of lagging can enhance pulley performance significantly. Ceramic lagging, for example, is noted for providing excellent grip and is particularly beneficial in wet or dusty conditions, greatly reducing the risk of belt slippage.
For professionals in the conveyor industry, familiarity with advancements in pulley technology is advantageous. Recent innovations include self-cleaning pulleys, which help in environments prone to material buildup, and high-tension pulleys that cater to the growing demand for high-load applications. These innovations underscore the trend towards increasing operational efficiency and minimizing downtime.
Authoritativeness in conveyor systems is demonstrated by adhering to industry standards and leveraging data from trusted sources. Engaging with credible suppliers who offer verification and certifications for head and tail pulleys is an effective strategy. These certifications often reflect quality assurance, providing peace of mind regarding product reliability and safety.
Furthermore, a trustworthy approach to selecting head and tail pulleys involves consulting with manufacturers or experts who can offer tailored advice based on specific operational requirements. Such consultations not only inform decisions but also foster strong supplier relationships, ensuring that any support needed post-purchase is readily available.
In conclusion, head and tail pulleys are indispensable in the efficient and reliable operation of conveyor systems. By leveraging real-world experience, embracing technological advancements, and consulting with authoritative sources, operators can ensure optimal performance and longevity of their conveyor systems. Proper selection, alignment, and maintenance of these components are key to maximizing operational efficiency and reducing costs, ultimately contributing to a more productive and profitable business operation.