In the world of industrial machinery and conveyor systems, few components are as crucial yet as understated as head and tail pulleys. These components serve as the backbone of conveyor systems, ensuring efficiency and reliability in material handling across various industries. Understanding the nuances of head and tail pulleys can significantly enhance system performance, reduce downtime, and streamline operations.
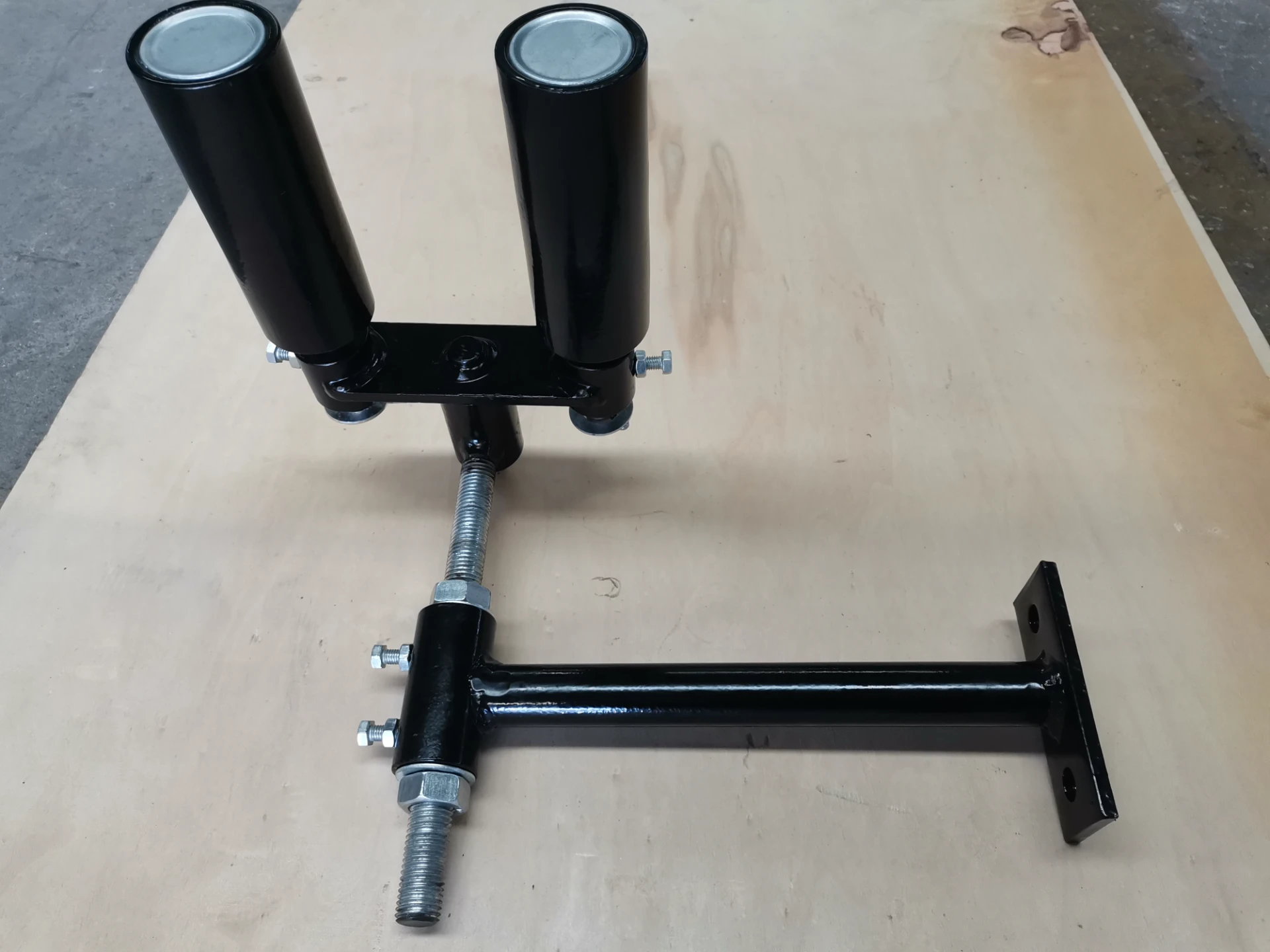
Head and tail pulleys are pivotal in determining the conveyor's operational efficacy. The head pulley is located at the discharge point of the conveyor and is responsible for driving the belt and material towards the destination. Its positioning and functionality are crucial for maintaining belt tension and ensuring smooth operations. The tail pulley, on the other hand, is situated at the feed point of the conveyor. It serves as the belt return, ensuring the belt correctly aligns with the conveyor and maintains consistent speed and tension.
A key aspect of optimizing conveyor systems is selecting the right head and tail pulleys. The materials used in the construction of these pulleys must withstand the specific demands of the industrial environment. For example, mining operations might necessitate pulleys made from high-durability materials to resist abrasion and corrosion. Alternatively, food processing might require stainless steel pulleys to ensure hygiene and compliance with health regulations.
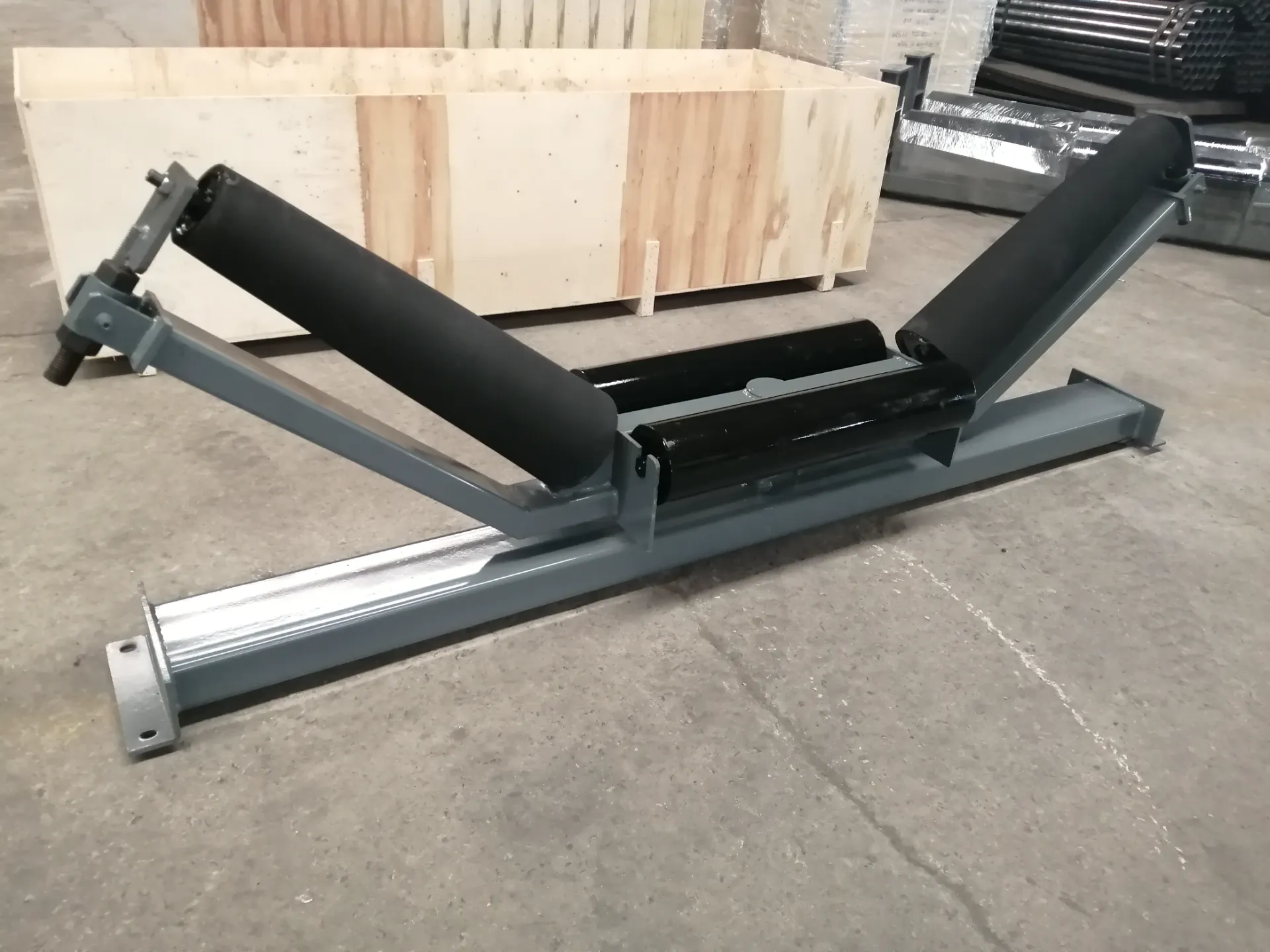
Selecting suitable pulleys also involves considering their size and design. The diameter of the pulley affects the conveyor belt's flexibility and the system's overall efficiency. Larger diameter pulleys can help reduce bending stress on the belt, thereby prolonging its lifespan. Additionally, the design of the pulley, whether crowned or flat, can influence belt tracking and tension. A crowned head pulley, for instance, can improve belt alignment and reduce the chances of slippage, enhancing operational reliability.
head and tail pulley
Furthermore, proper maintenance of head and tail pulleys is essential for optimal performance. Regular inspections are necessary to identify wear and tear, ensuring timely replacements and repairs. Misalignment and buildup of materials around the pulleys can lead to operational inefficiencies or even system breakdowns. Implementing a preventive maintenance schedule can help detect potential issues early, maintaining the conveyor's performance and reducing downtime.
Integrating advanced technologies into pulley systems also presents opportunities for enhancing conveyor efficiencies. Modern pulleys can be equipped with sensors that monitor various parameters such as temperature, alignment, and rotational speed. These sensors provide real-time data, enabling operators to anticipate potential failures and maintain system integrity proactively. Utilizing IoT and data analytics can vastly improve operational efficiencies and lead to significant cost savings.
Additionally, the influence of industry standards and regulations cannot be overstated. Adhering to global standards such as CEMA (Conveyor Equipment Manufacturers Association) ensures that pulley systems meet minimum safety and quality benchmarks. Compliance not only enhances system reliability but also builds trust with stakeholders across the supply chain.
In conclusion, head and tail pulleys play a fundamental role in the overall efficacy of conveyor systems. Their importance extends beyond mere mechanical components to becoming strategic assets in material handling processes. Selecting the right pulleys, prioritizing maintenance, leveraging technology, and adhering to industry standards are key factors in ensuring their optimal performance. As industries evolve and the demand for efficiency increases, the role of head and tail pulleys will continue to be indispensable, driving innovation and operational excellence in material handling systems.