A friction drive pulley is a fundamental component in various mechanical systems, providing an efficient and reliable method for transmitting power without the use of chains or gears. Understanding the intricacies of friction drive pulleys can offer a significant advantage for anyone involved in mechanical design or maintenance, ensuring optimal performance and longevity of machinery.
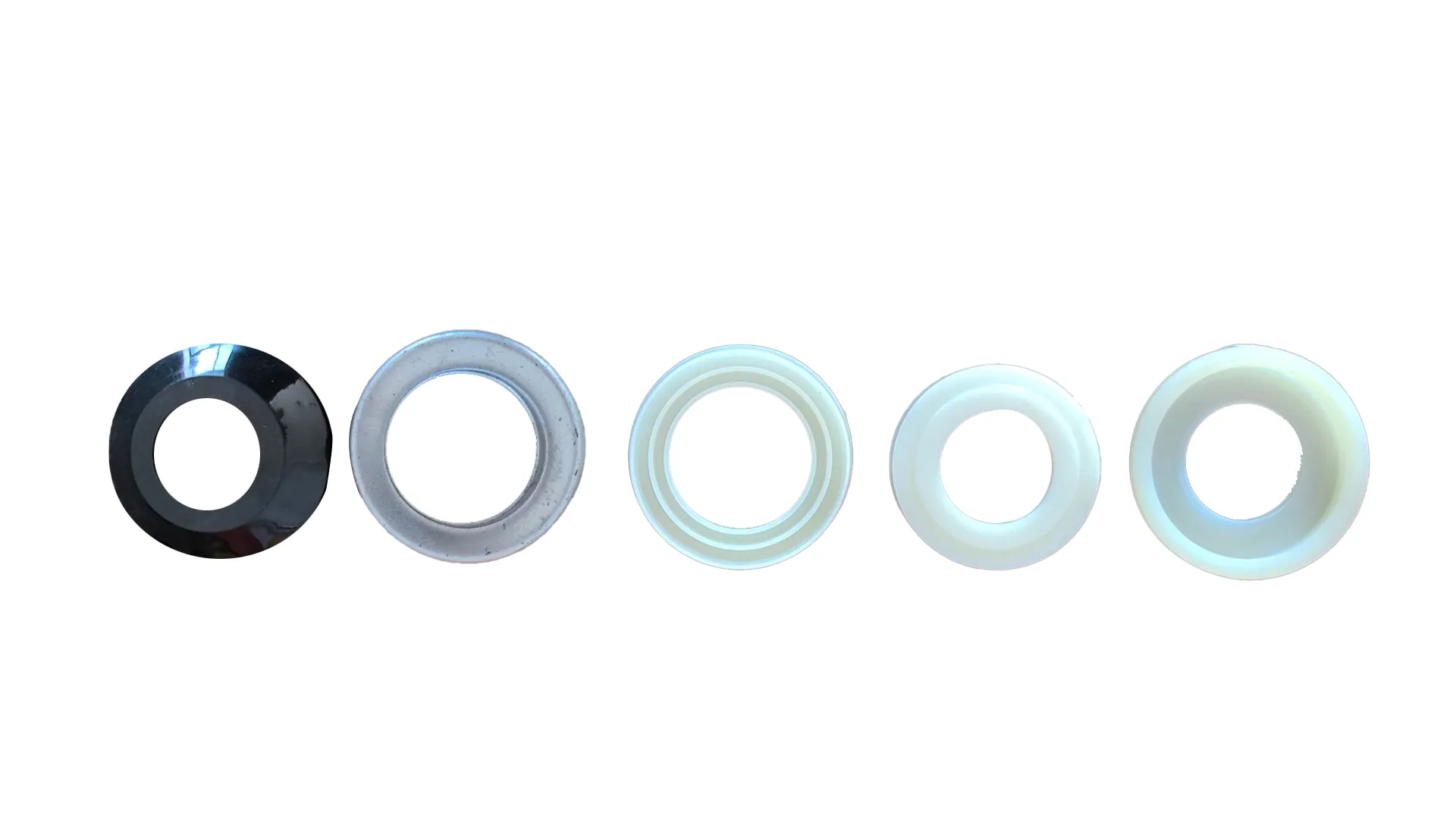
Experience has shown that the selection of the right friction drive pulley can dramatically influence the efficiency of your machinery. A client of mine in the textile industry was struggling with frequent downtimes due to belt slippage. After a thorough analysis of their system, it became clear that the issue stemmed from the improper specifications of the pulleys in use. By switching to a correctly sized friction drive pulley with the appropriate surface texture and material, the client managed to reduce downtime by 30%, thus increasing overall productivity.
Expertise in the field is crucial for both selecting and maintaining friction drive pulleys. These pulleys come in various materials, including rubber, metal, and composite, each suited for different operational demands. Rubber pulleys, for instance, are known for their excellent grip and vibration absorption, making them ideal for applications where smooth, noise-free operations are required. Metal pulleys, on the other hand, offer durability and strength, making them suitable for heavy-duty applications.
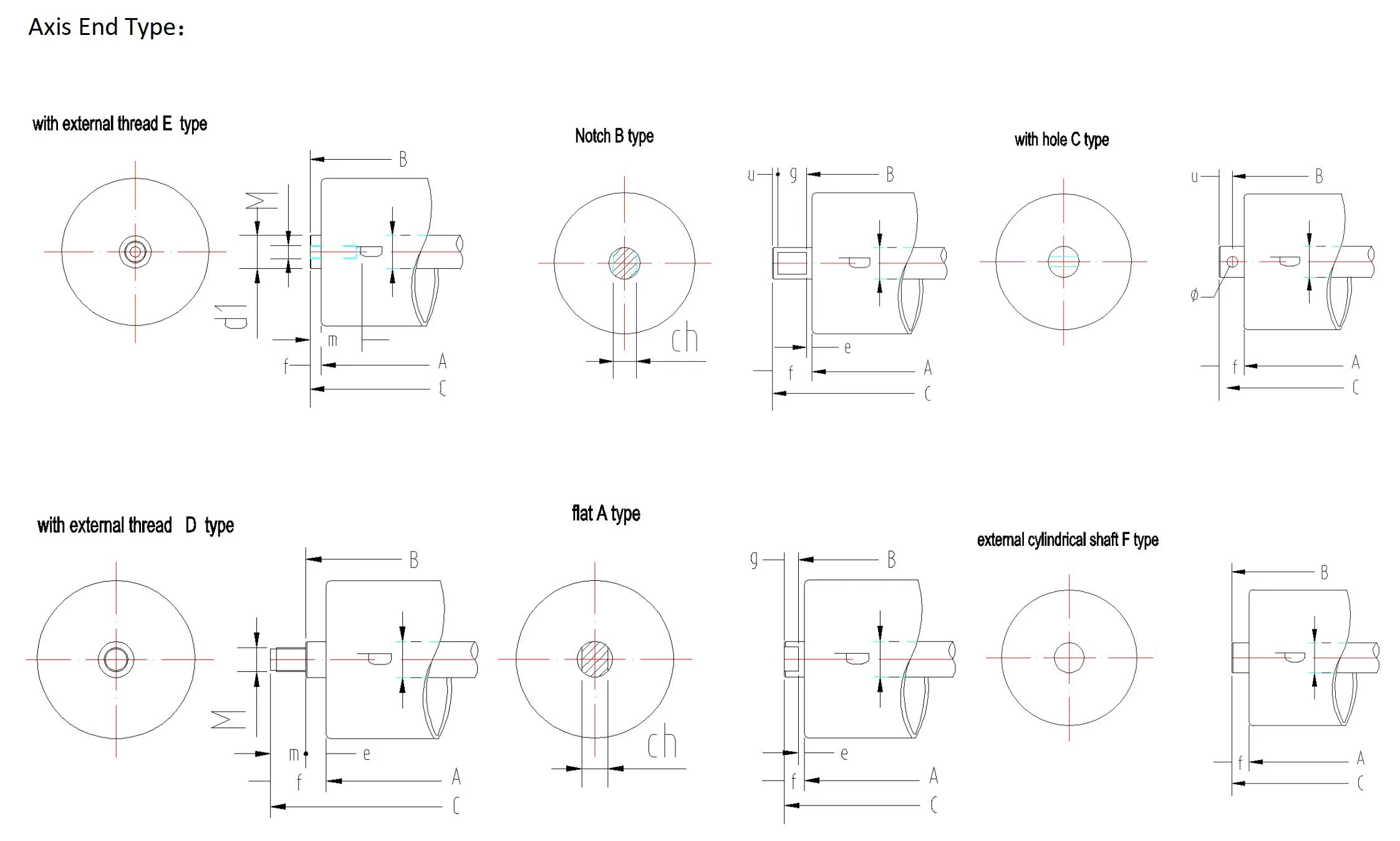
An experienced mechanical engineer recognizes the importance of the coefficient of friction between the pulley and the driven surface. This coefficient determines the efficiency of power transmission and is affected by factors such as material choice, surface finish, and environmental conditions. Regular maintenance, including the inspection of wear and tear and ensuring proper tensioning of the belts, can greatly enhance the lifespan of the friction drive system.
friction drive pulley
In terms of authoritativeness, it is vital to refer to established standards and manufacturers’ guidelines when dealing with friction drive pulleys. Reputable manufacturers provide detailed documentation on the performance characteristics of their products, which can serve as a reliable source for ensuring compliance with applicable mechanical standards and best practices. Consulting these resources can prevent costly mistakes and improve the reliability of the machine setup.
Trustworthiness in product reviews and user testimonials also plays a pivotal role in the decision-making process. Engaging with user communities or tech forums can provide insights into the durability and performance of specific pulley models in real-world applications. For instance, one user reported a significant increase in machine output by replacing a generic pulley with a model designed specifically for high-torque applications, demonstrating the value of peer feedback.
When considering upgrades or replacements, it is essential to evaluate the total cost of ownership. While initial costs might seem prohibitive, investing in a high-quality friction drive pulley typically results in lower maintenance costs and reduced operational disruptions over time. An analysis revealed that businesses that prioritize quality over short-term savings experience a notable decrease in total maintenance expenses, often covering the initial investment within a year.
Friction drive pulleys are indispensable across industries, from automotive to heavy machinery. Implementing the correct friction drive pulley can increase efficiency, reduce maintenance costs, and extend the life of your equipment. By leveraging real-world experience, technical expertise, authoritative resources, and trustworthy feedback, businesses can make informed decisions that enhance operational productivity and reliability. As industries evolve with new technological innovations, the role of friction drive pulleys in mechanical systems is likely to expand, underscoring the need for ongoing education and adaptation in this crucial area.