In the world of mechanical systems, particularly those involving power transmission, the concepts of the driven pulley and driver pulley hold paramount importance. These are not mere components; they are the linchpins that facilitate the seamless operation of countless machines, from simple conveyor belts to complex industrial machinery. Understanding their roles, differences, and applications can significantly impact efficiency and productivity.
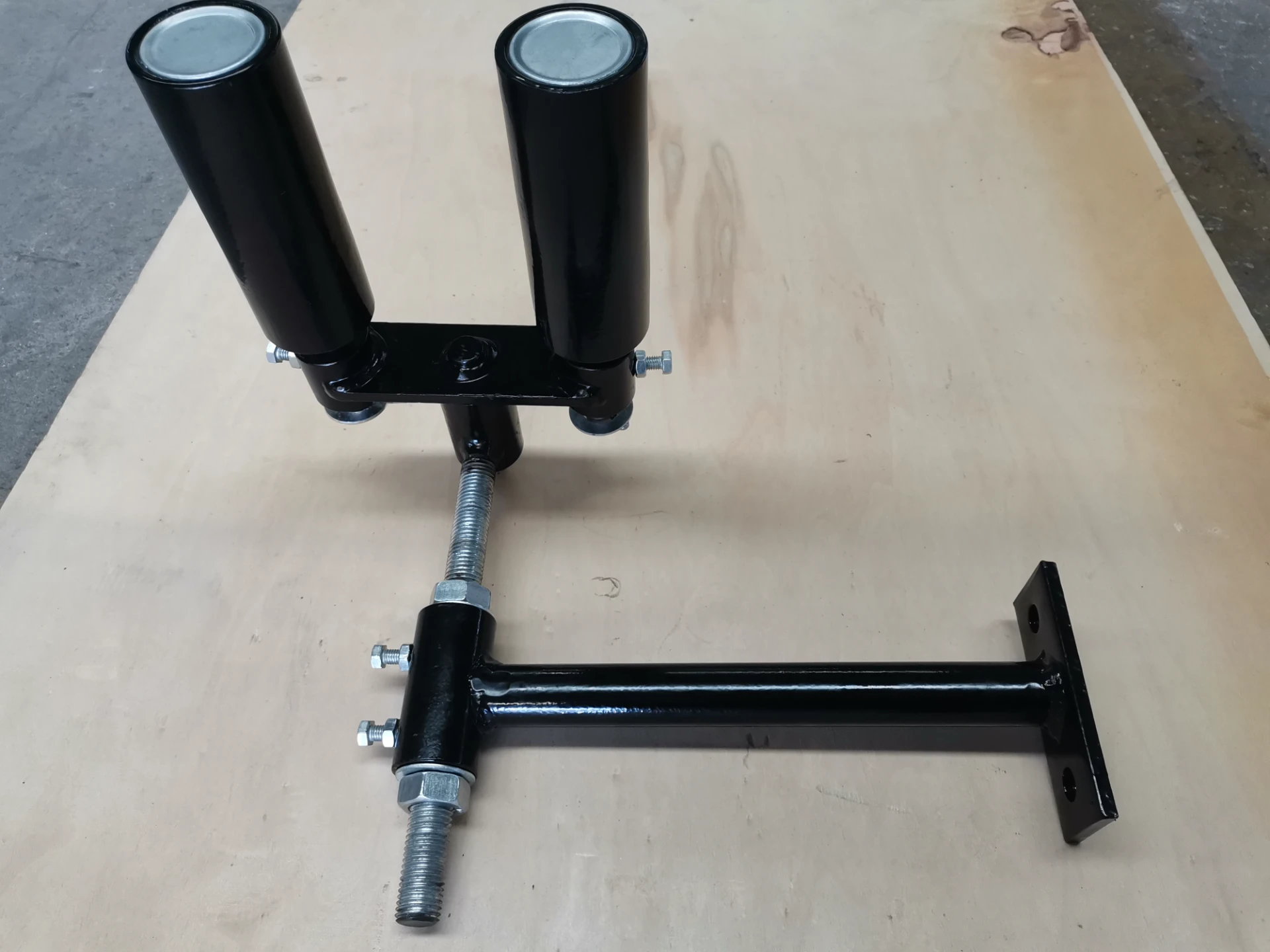
At the heart of any pulley system is the driver pulley. It is the component directly connected to the power source, such as an engine or motor. The driver pulley initiates motion, converting the power source's energy into mechanical movement. This movement is then transferred to the driven pulley, setting into motion the connected mechanical parts or system.
In contrast, the driven pulley is the recipient of this energy transfer. Functionally, it is tasked with converting the mechanical energy received from the driver pulley into usable power for other components of the machinery, often resulting in the desired mechanical output, whether that be rotational motion, lifting, or conveyance of materials.
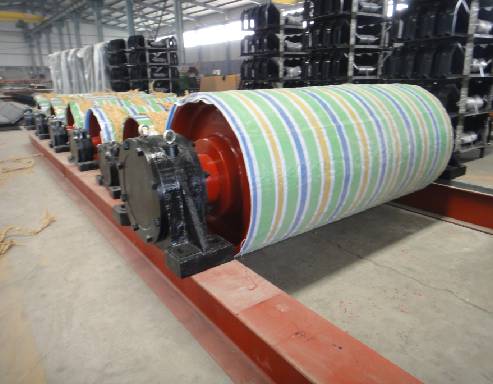
The synergy between driven and driver pulleys is critical and is governed by several factors, including size ratio, material, and tensioning. The size relationship, known as the pulley ratio, determines the speed and torque of the driven mechanism. A larger driver pulley compared to a driven pulley results in a speed increase, whereas a smaller driver pulley increases torque. This understanding allows engineers and designers to tweak pulley systems to meet specific operational needs.
Material selection for both driver and driven pulleys also plays a key role in their performance and longevity. High-quality materials, often metals or reinforced polymers, are chosen based on the application's endurance requirements. This is where the expertise of material science meets practical application, ensuring that the pulleys can withstand the operational stresses they face daily.
driven pulley and driver pulley
From an expertise standpoint, the installation and maintenance of these pulleys require precision and regular monitoring. Misalignment or incorrect tensioning can lead to slippage, excessive wear, and eventual system failures. Regular maintenance checks, including belt condition and alignment inspections, are crucial for prolonging the lifespan of both pulleys and ensuring efficient operation.
Authoritativeness in the context of driven and driver pulleys can be seen in industry standards and certifications that ensure these components are produced and perform to established benchmarks. Leaders in pulley manufacturing adhere to strict quality controls, providing users with components that boast reliability and durability.
Experience with these systems underlines their versatility across industries. In manufacturing, for example, pulley systems streamline production lines, enhancing efficiency. In the agricultural sector, they drive essential machinery, from tractors to irrigation systems, showcasing their adaptability and indispensability.
A trusted pulley system is not just about the mechanical parts in play but also about the partnerships between manufacturers and end-users. Companies specializing in pulley systems often offer extensive support, from initial consultation to after-sales service, ensuring users can maximize their mechanical investments with peace of mind.
In conclusion, the intricacies of driven and driver pulleys encompass more than just basic mechanical concepts. Their profound impact on system efficiency, the importance of material choice, the necessity of precise installation and maintenance, adherence to authoritative standards, and the trust built through strong manufacturer-client relationships all contribute to their critical role in modern mechanical systems. As industries evolve, the driven and driver pulleys continue to adapt and innovate, underpinning the success and advancement of countless applications worldwide.