Conveyor pulley lagging is a critical component in the efficient operation of conveyor systems. Pulley lagging not only enhances traction between the belt and pulley but also reduces wear and minimizes slippage. While there are various types of lagging materials available, choosing the appropriate type is essential for system efficiency and longevity. With decades of industry experience, the correct selection and application of conveyor pulley lagging can significantly impact productivity and maintenance costs.
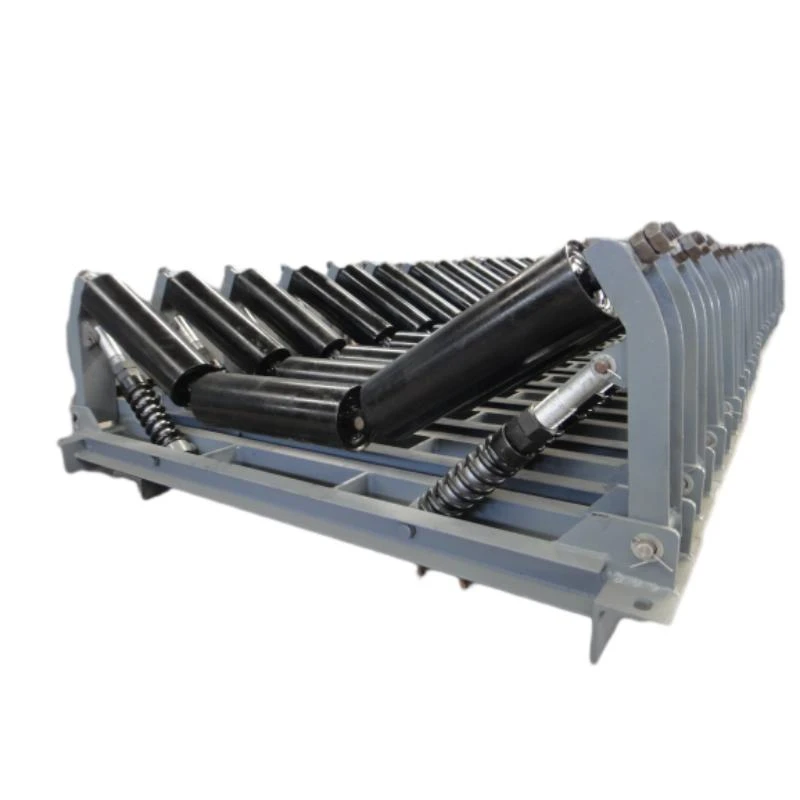
Rubber lagging is one of the most commonly used types, known for its versatility and cost-effectiveness. Available in a variety of patterns, such as diamond and herringbone, rubber lagging provides excellent grip and reduces belt slippage under different load conditions. The elastic nature of rubber also helps in absorbing shock loads and reducing noise, making it ideal for a variety of industrial applications. However, selecting the right compound and thickness is crucial to ensure suitability for specific environmental conditions and operational demands.
Ceramic lagging, heralded for its durability and superior friction properties, is typically used in more demanding settings. It offers remarkable wear resistance and is designed to handle significant abrasive conditions where conventional rubber lagging might falter. Ceramic lagging features embedded ceramic tiles that enhance grip, particularly in wet or muddy environments. This type of lagging is often used in mining or heavy-duty material handling industries, where the conveyor systems are subjected to harsh, abrasive materials. Nevertheless, proper installation by experienced professionals is vital to fully leverage the advantages of ceramic lagging.
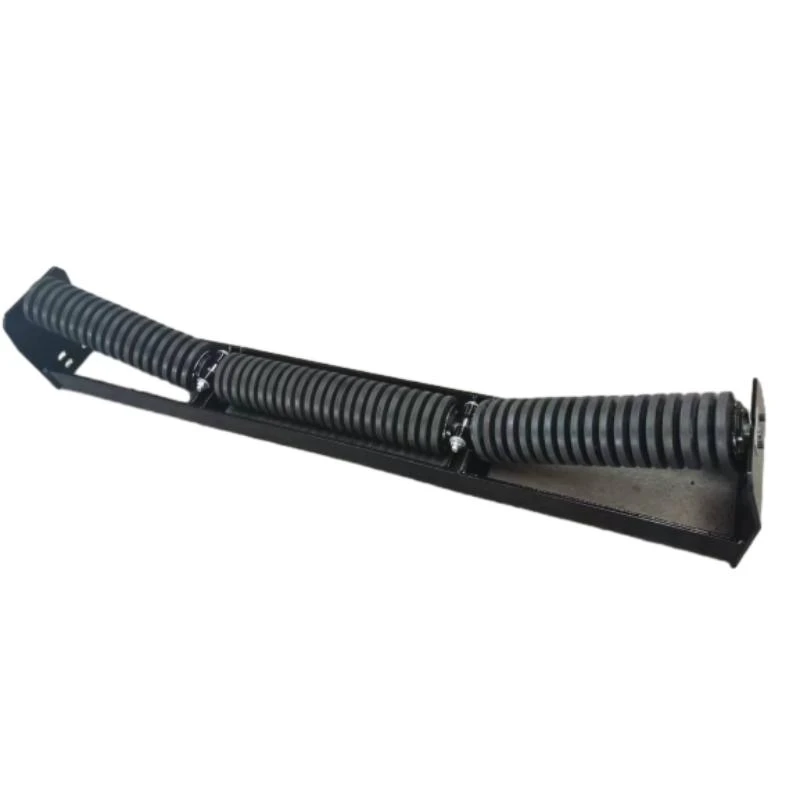
Polyurethane lagging, a relatively new addition to the lagging options, brings a balance of durability and flexibility. Polyurethane's natural resistance to chemicals and oil makes it ideal for environments where these contaminants are prevalent. Its resilience to cuts and tears further enhances its applicability in sectors requiring robust solutions to avoid frequent maintenance shutdowns. While boasting longer service life, polyurethane lagging can be more cost-intensive than rubber, necessitating a careful cost-benefit analysis before implementation.
conveyor pulley lagging types
Each type of lagging comes with its own set of benefits, but the key to maximizing these benefits lies in the expertise with which the lagging is applied. Selecting an appropriate lagging type involves assessing factors such as environmental conditions, the nature of materials being conveyed, temperature variations, and the overall design and speed of the conveyor system. An expert evaluation can determine whether the lagging should be cold-bonded or hot-bonded, each method offering distinct advantages in terms of adhesion strength and application convenience.
While the choice of lagging is paramount, expertise in the installation process can’t be overstated. An improperly installed lagging can lead to premature wear, slippage, and even catastrophic system failure. Therefore, engaging seasoned professionals equipped with the latest installation technologies ensures that the lagging adheres perfectly to the pulley, which, in turn, optimizes the conveyor performance.
Building trust and authority in conveyor pulley lagging requires transparency and reliability; thus, collaboration with manufacturers who offer comprehensive after-sales services and technical support is invaluable. A manufacturer’s commitment to quality through rigorous testing procedures and adherence to industry standards further cements their reputation as a trustworthy partner in conveyor system maintenance.
Ultimately, choosing the right conveyor pulley lagging and maintaining it effectively leads to improved operational efficiency and reduced costs. Businesses can benefit from enhanced productivity and minimized downtimes by investing in quality materials and expert installation. As the industry progresses, continuous innovations in lagging materials and methods will undoubtedly provide even greater opportunities for optimizing conveyor system performance. It is imperative for businesses to stay informed about these advancements, ensuring that their systems are equipped with the most efficient and durable lagging solutions available.