Rubber pulleys, integral components in a multitude of machinery, demonstrate exceptional utility across various industries. Their versatility makes them indispensable, yet choosing the right rubber pulley can be daunting without adequate expertise. This article aims to illuminate their nuances, advancing your understanding and helping refine your selection process.
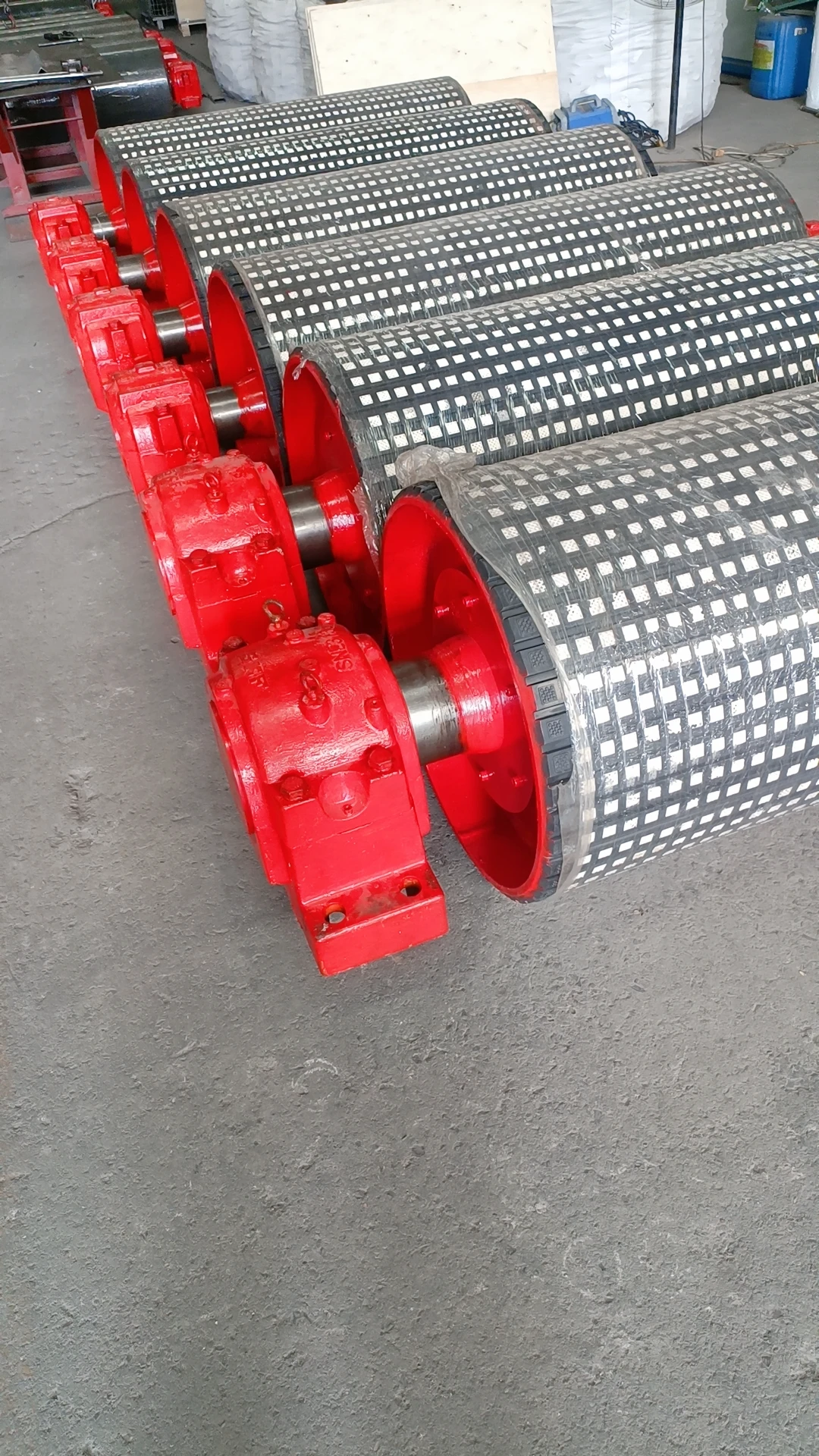
Rubber pulleys are known for their resilience and high-performance characteristics, functioning effectively in a range of environments. Their primary role is to transmit motion and change direction within power transmission systems, which is crucial in machinery that relies on belt and pulley mechanisms for operation. Generally, they're found in manufacturing, automotive, mining, and even consumer electronics. Due to the elasticity and high friction coefficient, rubber ensures minimal slippage and maximum grip, enhancing the efficiency of operations in which precision is paramount.
Experience tells us that the longevity of a rubber pulley depends on several factors, including the environment and the mechanical stressors involved. For instance, in the mining industry, pulleys are exposed to abrasive materials and must withstand harsh conditions. Therefore, selecting a rubber pulley with the right hardness and resistance to wear and tear is vital. Furthermore, evaluating temperature ranges and exposure to chemicals will influence your choice of material. Conducting a comprehensive assessment to determine these conditions can help significantly in extending the lifespan of pulleys.
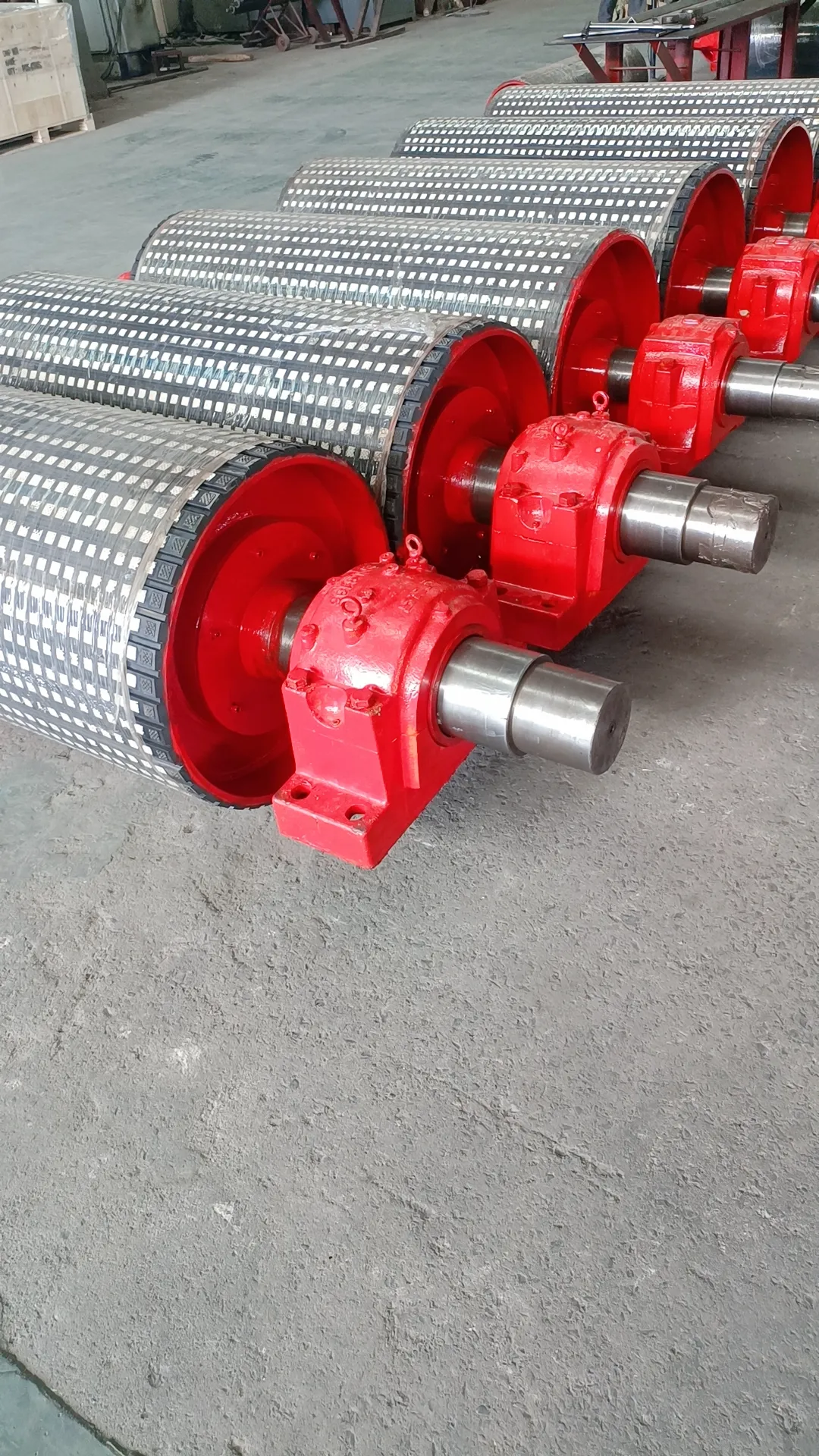
Expertise in rubber materials allows for innovations that perfect their application. Advanced manufacturing techniques now allow for custom-designed rubber compounds tailored to specific industrial requirements. Neoprene and nitrile rubbers, for example, are favored for their oil and temperature resistance, while silicone is preferred in high-temperature applications. The selection of the right compound cannot be overstated, as it directly impacts the pulley’s performance and durability.
rubber pulley
In terms of authoritativeness, it is essential to rely on manufacturers with a proven track record of producing high-quality rubber pulleys. Look for a provider that conducts rigorous testing and complies with international standards. Certifications like ISO 9001 ensure that the manufacturing processes meet strict quality criteria, offering assurance of reliability and performance. An authoritative manufacturer not only delivers a superior product but also offers valuable insights into product selection through expert consultations.
Trustworthiness stems from transparency and post-purchase support. A trusted rubber pulley supplier provides detailed product specifications and educational resources to help clients understand the functionality of various products. Moreover, dependable suppliers often offer comprehensive after-sales services, including maintenance tips and troubleshooting guides, which helps in building a long-term trusted partnership. Engaging with suppliers who prioritize customer education and satisfaction reinforces confidence in your investment.
To summarize, selecting the right rubber pulley requires a blend of experience, expertise, authority, and trust. Start with a detailed understanding of your machinery's requirements, followed by identifying the environmental conditions they will operate in. Leverage expert guidance when choosing materials suited to those conditions, and prioritize reputable manufacturers for assured quality and reliability. Ultimately, the combination of these aspects will empower you to make informed decisions, ensuring optimal operation and longevity of your machinery. Your careful selection will not only enhance your system’s efficiency but also provide a tangible return on investment through reduced downtime and maintenance costs, highlighting the invaluable role of rubber pulleys in modern industry.