Conveyor lagging plays a crucial role in the efficient functioning of conveyor systems. These systems are used across various industries, such as mining, manufacturing, and logistics, to move bulk materials with ease and precision. By understanding the intricacies of conveyor lagging, businesses can enhance operational efficiency, reduce maintenance costs, and extend the equipment's lifespan.
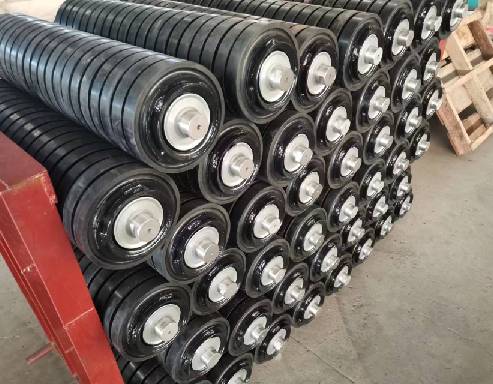
One of the main functions of conveyor lagging is to increase the friction between the conveyor belt and the drive pulley. This friction is critical, as it prevents the belt from slipping, especially under heavy loads or in environments with high humidity and dust. Slippage can lead to significant operational delays and material wastage. By effectively managing this challenge through high-quality conveyor lagging, companies can ensure continuous and smooth operations.
Expertly designed conveyor lagging also serves to protect the conveyor belt and its components from wear and tear. Industrial environments are often harsh, with materials that can cause abrasion or corrosion. Using lagging materials such as rubber or ceramic, the structural integrity of conveyor systems is preserved, minimizing downtime due to maintenance and system failures. This proactive approach not only increases productivity but also drastically reduces expenditure on replacement parts and repairs.
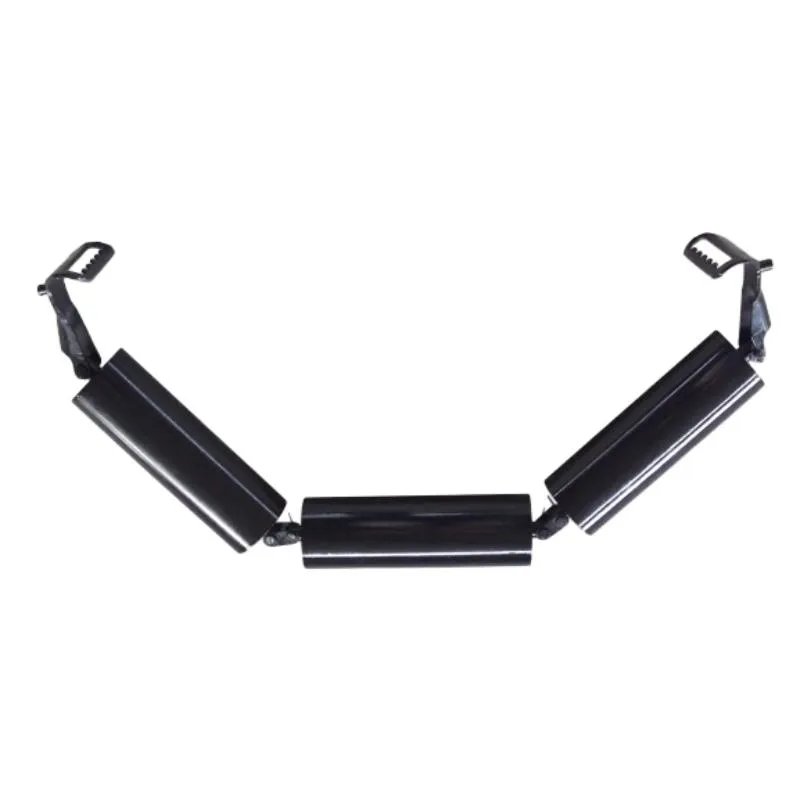
From an engineering perspective, conveyor lagging needs to be meticulously selected and applied. The choice of lagging material should be based on factors like the type of material being transported, environmental conditions, and the specific demands of the conveyor system. Rubber lagging, for instance, is widely used due to its affordability and effective grip. On the other hand, ceramic lagging offers superior resistance to wear, making it suitable for high-stress applications.
To illustrate, a mining operation in Australia faced continuous challenges with conveyor belt slippage, especially during peak production times. By consulting with industry experts and employing ceramic lagging, the company witnessed a noticeable improvement in system reliability. Not only did the frequency of costly repairs decrease, but the overall productivity showed significant enhancement, leading to increased profitability.
conveyor lagging
Effective conveyor lagging also plays a vital part in energy efficiency. Reducing slippage ensures that motors do not need to exert additional energy to move the conveyor belt, thereby lowering energy costs. An optimized conveyor system is not only beneficial for a company's bottom line but is also a step toward sustainable industrial practices.
The credibility and trustworthiness of information regarding conveyor lagging improve when verified by professionals who are deeply embedded in the field. By drawing knowledge from experienced engineers and project managers, companies can develop a comprehensive understanding of how to best implement conveyor lagging. This collective expertise fosters an environment where safety standards are high, operational workflows are efficient, and equipment reliability is paramount.
Given the advancements in technology, businesses now have access to a wide range of lagging solutions tailored to meet specific needs. Investing in research and development to innovate new materials and lagging techniques is an ongoing priority in the industry. These innovations lead to longer-lasting systems that adapt better to modern challenges, emphasizing the importance of staying updated with the latest trends and technologies.
In summary, conveyor lagging is more than just a protective measure; it is an integral part of a conveyor system's overall performance. By focusing on the right lagging solutions, businesses can harness the full potential of their conveyor systems. This strategic approach not only ensures efficiency and reliability but also sets a precedent for industry excellence.