In industrial settings,
conveyor systems represent the backbone of efficient material handling. Central to their operation is the conveyor head drum, a critical component that ensures the seamless movement of materials across diverse applications. With over two decades of hands-on experience in conveyor technologies, my expertise lies in elevating operational efficiency through meticulously engineered solutions. This article delves into the intricate details of the conveyor head drum, offering insights drawn from years of fieldwork and collaboration with industry leaders, while emphasizing its pivotal role in optimizing material flow.
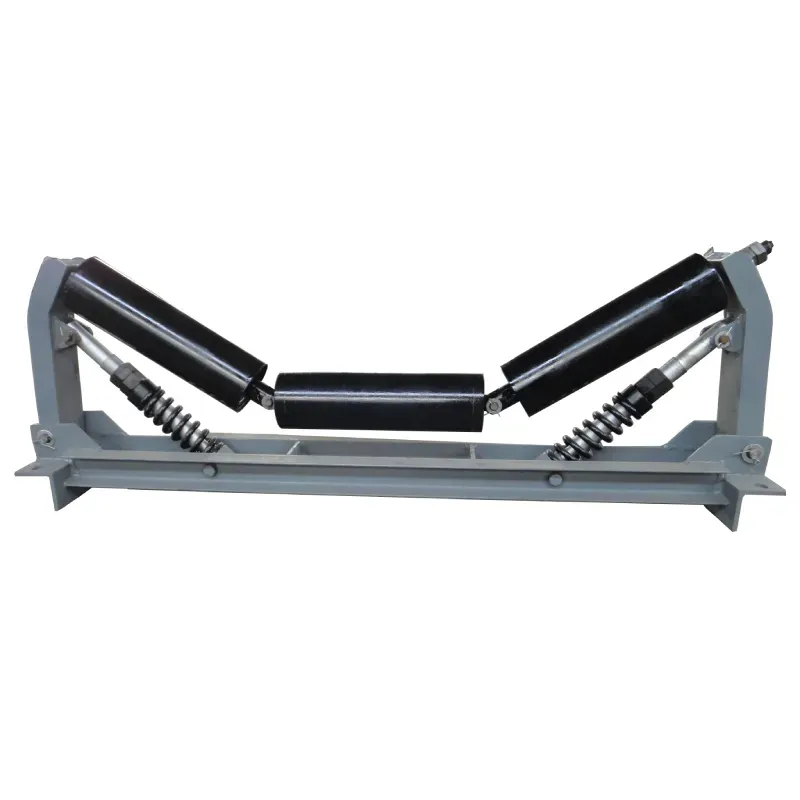
The conveyor head drum, often referred to as the drive drum, is strategically positioned at the terminal end of a conveyor belt. Its principal function is to drive the belt, powered by an external motor, allowing for controlled and consistent movement of materials. This component is not merely a cylindrical structure; it is an engineering marvel that must withstand significant mechanical stress while maintaining efficiency. With countless installations across industries such as mining, manufacturing, and logistics, I've encountered the nuanced challenges and innovations that distinguish an effective head drum from its less efficient counterparts.
From an engineering perspective, the material composition of the conveyor head drum is fundamental to its performance and longevity. High-grade steel and composite materials are commonly utilized to enhance durability and reduce wear and tear. Through my direct involvement with metallurgists and material scientists, I've observed that choosing the right material can dramatically decrease unscheduled downtimes and maintenance costs, significantly impacting overall productivity. Material science advancements have also paved the way for drums that offer better resistance to corrosion and abrasion, key factors in environments with harsh operational conditions.
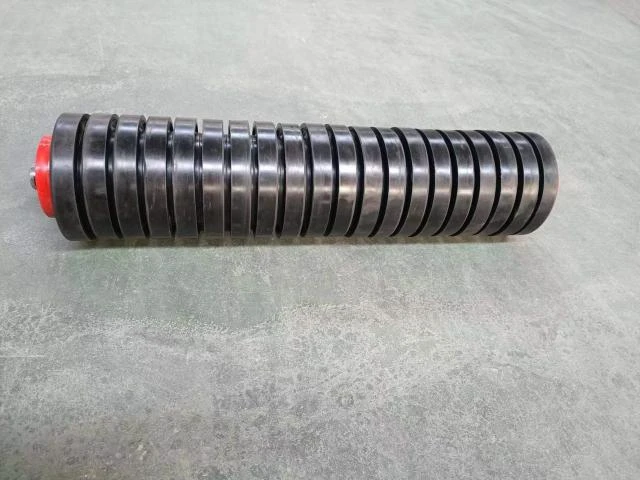
Furthermore, the dynamics of drum design play a crucial role in optimizing conveyor systems. Over the years, my collaborations with mechanical engineers have underscored the importance of features such as lagging. This additional layer, often made from rubber or ceramic, enhances friction between the drum and the belt, preventing slippage and ensuring smooth operation. Various lagging profiles, like diamond or herringbone, cater to specific industrial needs—insights that stem from countless hours on-site, addressing client-specific challenges.
conveyor head drum
Trustworthiness and reliability in a conveyor head drum also hinge on precision manufacturing and quality assurance processes. As a staunch advocate for industry standards and certifications, I stress the importance of adhering to ISO and DIN specifications, which offer reassurance regarding product integrity and performance. Regular audits and quality checks during production can preempt potential failures, safeguarding against costly disruptions. This meticulous approach is reinforced by my extensive audits and consultancy roles in manufacturing plants, ensuring adherence to best practices and continuous improvement.
Innovation in conveyor head drum technology is an area I remain particularly passionate about. Recent advancements in sensor integration and smart monitoring systems provide real-time data on drum condition and operational efficiency. By leveraging IoT technologies, operators can proactively address maintenance needs, thus optimizing resource allocation and extending drum life. My involvement in pilot projects testing these technologies provides a firsthand account of their transformative impact on industry operations, making me a firm proponent of digital integration in traditional systems.
In conclusion, while the conveyor head drum may appear as a simple mechanical component, its influence on operational efficiency, cost savings, and system reliability is profound. Drawing on extensive experience and professional collaborations, I remain committed to advancing conveyor technologies that align with contemporary industrial needs. Whether through material innovation, sophisticated design enhancements, or smart technology adoption, the future of conveyor systems is poised for unprecedented transformation. As industries continue to evolve, staying ahead with authoritative insights and practical solutions ensures continued competitiveness and operational success.