Conveyor drum lagging is a pivotal component in the efficient operation of conveyor systems, playing a significant role in enhancing productivity, reducing downtime, and minimizing operational costs. As industries globally, from mining to logistics, increasingly rely on conveyor systems for streamlined operations, the demand for effective drum lagging solutions has never been more pronounced. This article elucidates the intricacies of conveyor drum lagging, emphasizing its benefits, types, and installation expertise.
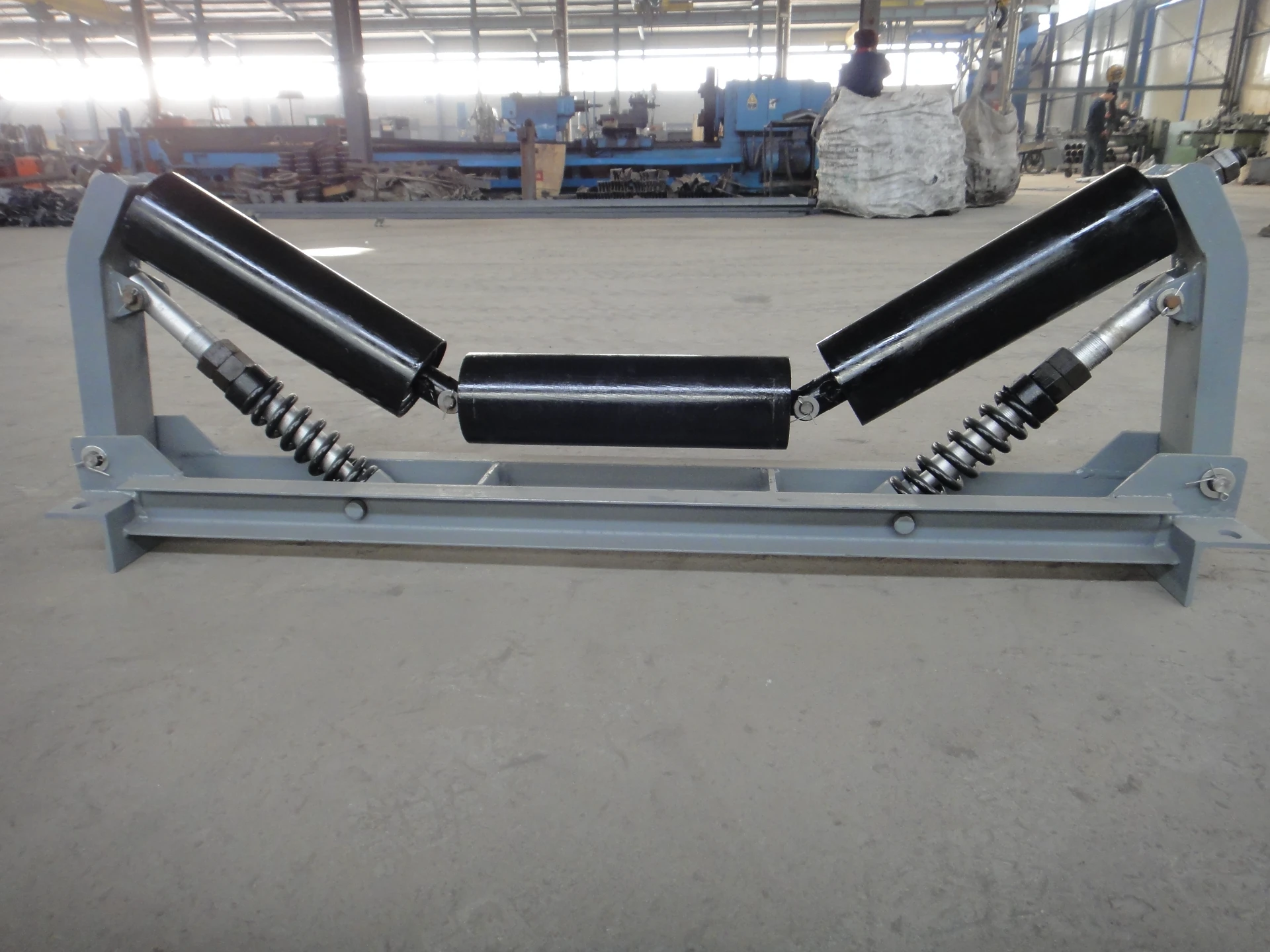
Conveyor drum lagging primarily functions to increase the friction between the conveyor belt and the pulley, thereby preventing slippage and improving overall grip. This is crucial for optimizing belt performance under various operational conditions. With enhanced grip, conveyor belts can operate more smoothly, effectively reducing wear and tear, and extending the lifespan of both the belt and the pulley.
There are several types of drum lagging materials, each catering to specific industrial needs. Rubber lagging is the most common type due to its cost-effectiveness and moderate durability. It is available in different designs like plain, diamond, and grooved patterns, each offering distinct advantages in terms of grip and water dispersion. Ceramic lagging, on the other hand, is favored in environments that demand superior abrasion resistance and longevity. It incorporates ceramic tiles embedded within the rubber matrix, providing exceptional durability and grip, making it ideal for high-tension and high-speed conveyor systems.
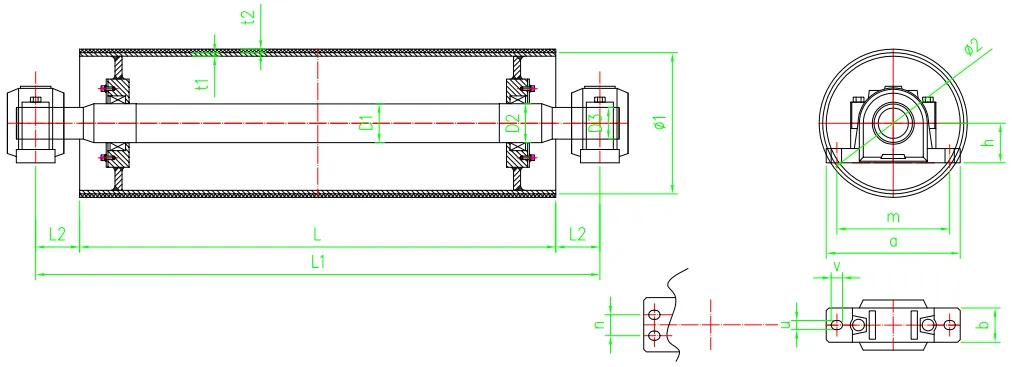
Another innovative solution is the use of polyurethane lagging. This type of lagging is renowned for its incredible resilience against abrasive materials and its ability to endure high-stress conditions, thus ensuring prolonged service life. Polyurethane lagging also offers excellent oil resistance, which is beneficial in sectors like manufacturing where conveyors may come into contact with oily substances.
Implementing the right kind of drum lagging can significantly impact a conveyor system's efficiency. For companies looking to enhance their conveyor operations, expert consultation is advised to determine the most suitable lagging material and pattern. This ensures not only the safety and efficiency of the conveyor system but also maximized return on investment by reducing downtime and maintenance costs.
conveyor drum lagging
The installation of drum lagging requires meticulous attention to detail and should be conducted by professionals with extensive expertise. Accurate installation ensures that the lagging performs its intended function effectively without premature wear. Experts recommend conducting a thorough analysis of the conveyor system’s operational parameters, including load capacities, speed, and the nature of materials being transported. This ensures the selection of an appropriate lagging solution tailored to specific operational demands.
In terms of maintenance, regular inspections of the drum lagging are essential to monitor wear and potential deterioration. Over time, even the most robust lagging materials will diminish in performance, necessitating timely replacement to maintain optimal conveyor performance. Adhering to a proactive maintenance schedule can significantly reduce unexpected operational downtime, thereby sustaining efficiency and productivity.
As industries continue to evolve, the advancements in drum lagging technology will undoubtedly play a crucial role in meeting the growing demands for reliability and efficiency in conveyor systems. Staying abreast of these technological developments can provide businesses with a competitive edge, enabling them to maintain seamless operations and deliver superior service.
In conclusion, conveyor drum lagging is an indispensable component in the operation of conveyor systems. Selecting the appropriate lagging material and ensuring its professional installation can lead to enhanced performance, longevity, and reduced operational costs. Companies must leverage expert knowledge and cutting-edge technologies to ensure their conveyor systems operate at peak performance, aligning with industry best practices for safety, reliability, and efficiency. As an essential aspect of modern industrial operations, understanding and implementing effective drum lagging solutions is key to achieving operational excellence and competitive advantage.