Pulley lagging is a crucial element in numerous industrial applications, playing an integral role in the efficiency and performance of conveyor systems. Its relevance is underscored by the various types that cater to diverse operational demands. An understanding of the different types of pulley lagging, their specific features, and applications enhances the decision-making process for engineers and plant managers, ensuring optimal system performance.
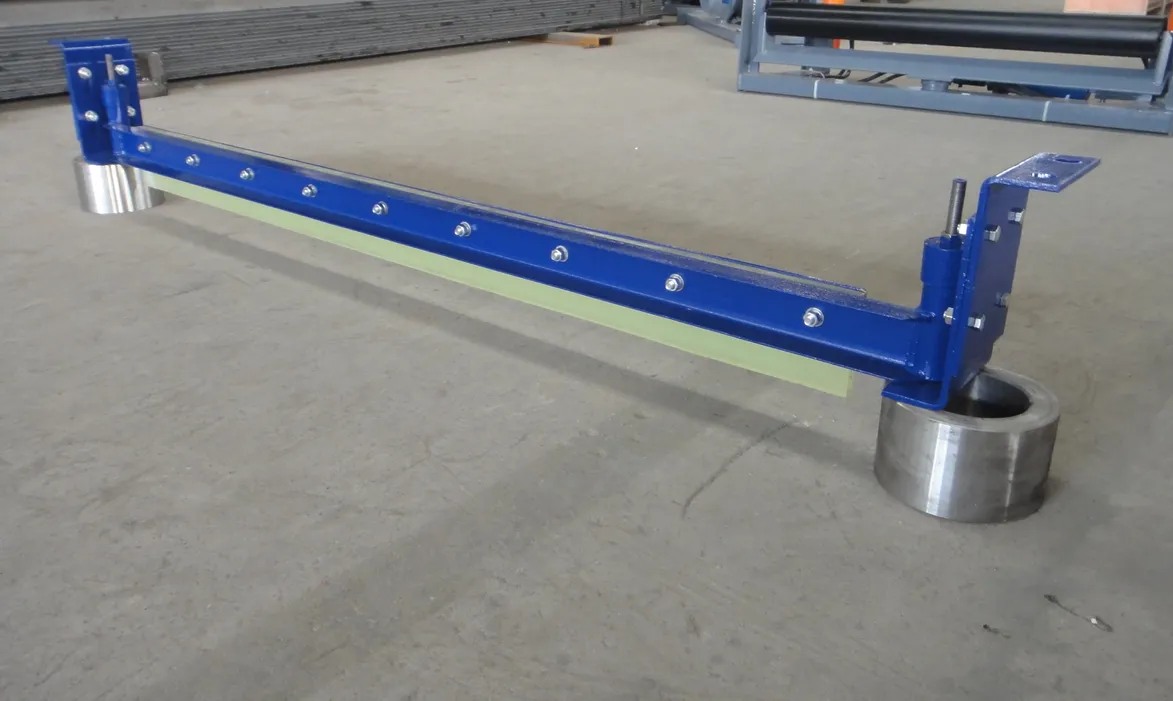
Rubber lagging is one of the most ubiquitous types, known for its versatility and resilience. It is typically chosen for environments where impact resistance and belt wear protection are paramount. Rubber lagging provides a high coefficient of friction, bolstering the grip between the pulley and the conveyor belt, reducing slippage, and enhancing the belt’s longevity. The material’s adaptability allows it to conform to the contour of the pulley, making it a preferred choice for irregular pulley surfaces. Furthermore, rubber lagging is often available in both natural and synthetic compositions, with the latter offering improved resistance to oil and temperature fluctuations, which is beneficial in industries such as mining and manufacturing.
On the other hand, ceramic lagging stands out with its exceptional wear resistance properties. This type is selected primarily for high-tension applications where abrasion from mineral materials is a significant concern. Ceramic lagging comprises embedded ceramic tiles that improve grip and reduce wear exponentially compared to traditional materials. The unique design accommodates the high-stress points across the pulley surface, maintaining structural integrity and ensuring reliability over extended periods. Additionally, ceramic lagging’s self-cleaning surface keeps the system functional even in harsh conditions, making it ideal for heavy-duty conveyor operations in the quarry, mining, and steel sectors.
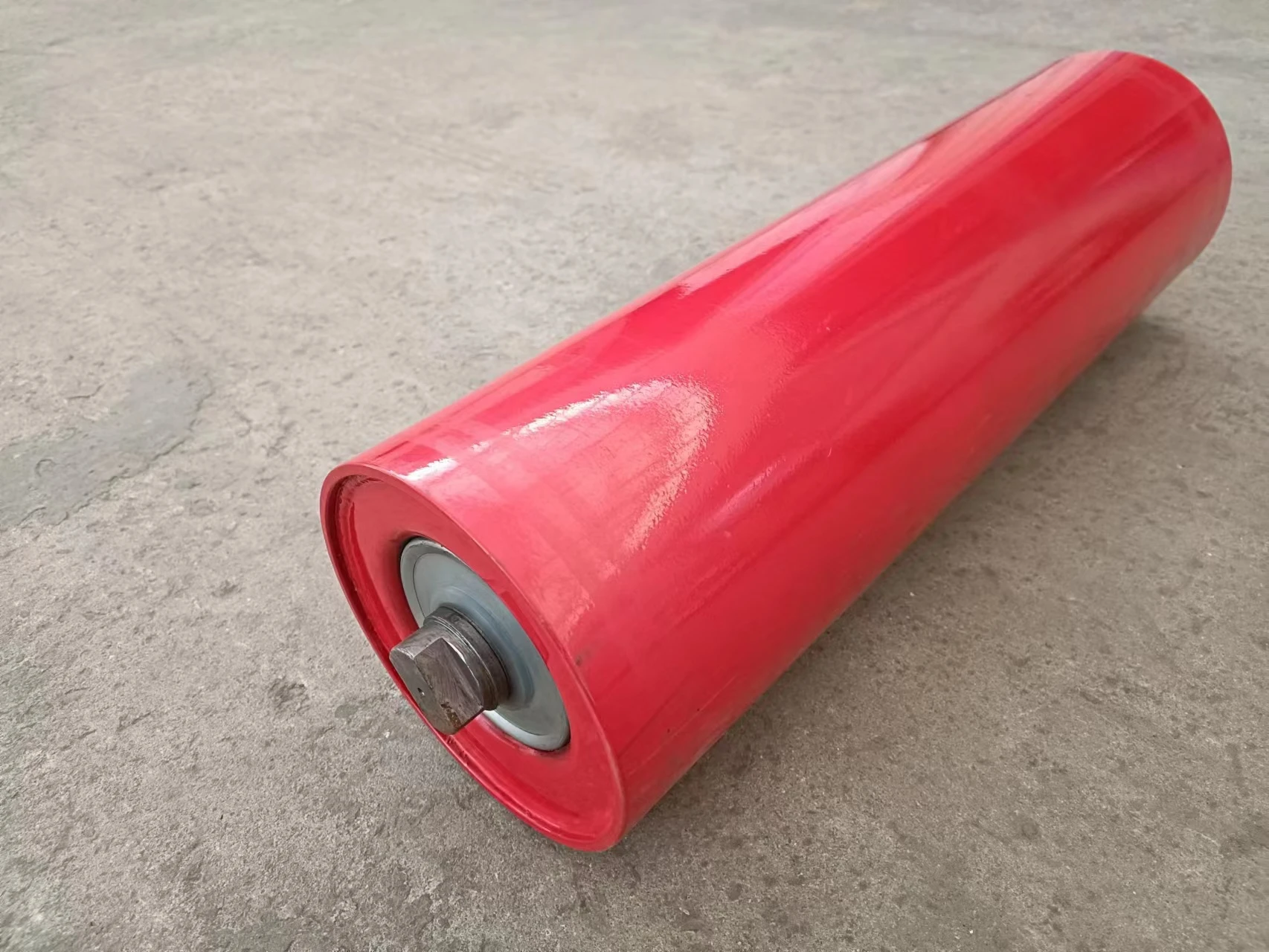
For environments where corrosion could severely impact pulley performance, stainless steel lagging offers an unparalleled solution. This type of lagging exhibits unmatched durability in settings exposed to moisture and chemical agents, such as food processing plants and chemical facilities. Its non-reactive nature ensures that the lagging will not degrade in corrosive atmospheres, maintaining its efficacy and system integrity over time. The smooth surface of stainless steel lagging also facilitates easy cleaning and maintenance, a critical factor in sectors with stringent hygiene standards.
types of pulley lagging
Polyurethane lagging serves as a flexible yet tough alternative for applications requiring a mix of durability and elasticity. Its chemical resistance and ability to withstand cuts and tears make it suitable for textile and logistics industries where lightweight and robust materials are essential. Polyurethane lagging’s superior bonding with metal substrates guarantees lasting adhesion, reducing the need for frequent repair or replacement.
Finally, diamond-pattern lagging is engineered to optimize traction and enhance water drainage. This pattern is vital in outdoor conveyor systems where water can accumulate, potentially causing belt slippage and inefficiency. The raised diamond shapes in the lagging design disperse water effectively, maintaining optimal belt-pulley contact and operational continuity. This type of lagging is particularly beneficial in agricultural and construction settings dealing with variable weather patterns.
Choosing the right type of pulley lagging is instrumental in achieving operational excellence. Factors such as environmental conditions, material type, and required traction levels all play a pivotal role in determining the most suitable option. By selecting lagging that aligns with specific industrial requirements, operational downtime is minimized, and conveyor belt longevity is maximized. This decision not only optimizes performance but also substantiates a commitment to efficiency and sustainability, marking a strategic advancement in industrial operations.
Each type of pulley lagging presents distinct advantages that align with particular industrial needs, enabling engineers to make informed selections that bolster system reliability and efficiency. As technology and materials continue to advance, these options will offer even greater customization and specificity, driving productivity across sectors.