Understanding the various types of pulleys used in conveyor belt systems is pivotal for optimizing industrial operations. These specialized components play an indispensable role in enhancing efficiency, reliability, and safety. In this guide, we delve into the unique types of pulleys in conveyor belt systems, offering insights based on industry expertise and authoritative evaluations.
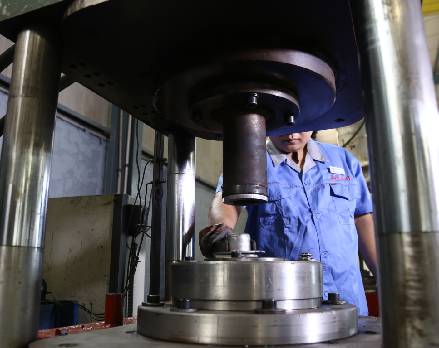
1. Drive Pulley
The drive pulley, often referred to as the head pulley, is accountable for driving the conveyor belt. It is directly connected to the motor and provides the necessary force to initiate and maintain the movement of the belt. Achieving optimal performance from a drive pulley involves ensuring proper alignment and tension, which can prevent slippage and wear. The materials used in making drive pulleys, typically coated with rubber or lagging materials, provide improved traction and longevity, critical for reducing downtime in high-demand environments.
2. Tail Pulley
Located at the opposite end of the conveyor system from the drive pulley, the tail pulley serves as a placeholder, maintaining tension and guiding the belt back to the drive pulley. The tail pulley does not contribute to power transmission; it often features adjustable mechanisms to ease the tension adjustments of the conveyor belt. Regular maintenance checks to ensure it remains free of debris and properly aligned are essential tips for sustaining operational efficiency.
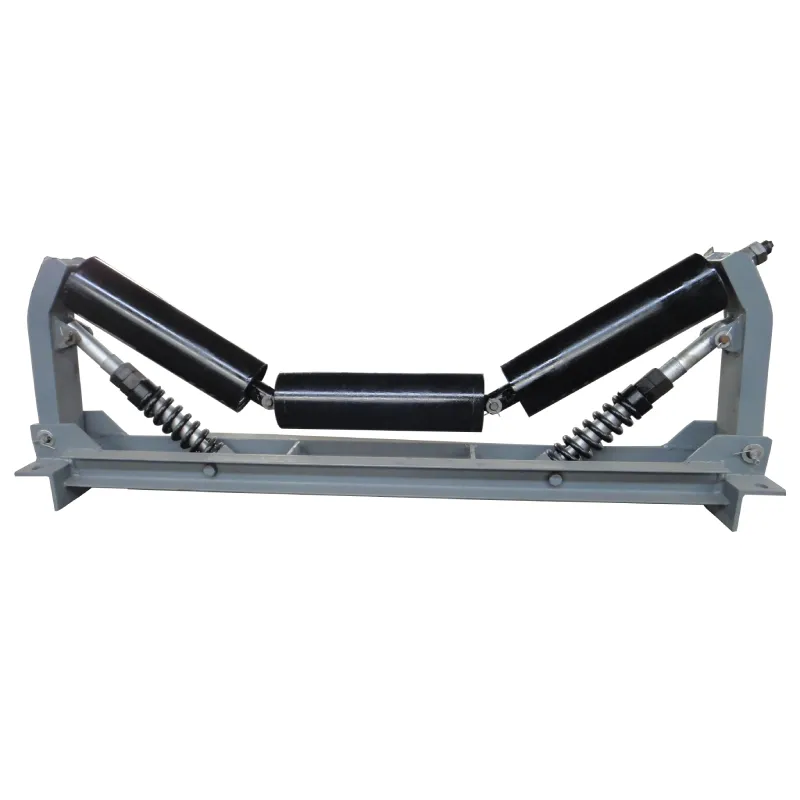
3. Snub Pulley
Snub pulleys are strategically positioned to increase the amount of contact between the belt and the drive pulley, thereby enhancing the wrap angle for better traction. Industry professionals recognize that by properly implementing snub pulleys, one can reduce the operational strain on the drive pulley, extending its lifespan and optimizing power consumption. This is especially beneficial in systems where load weights fluctuate.
4. Take-Up Pulley
The take-up pulley plays a vital role in automatically adjusting belt tension to counteract any stretching or strain caused by operational use. It is commonly part of a counterweight or screw-type mechanism. Ensuring the take-up pulley is correctly set up and routinely checked can mitigate risks of belt slippage and misalignment. Its ability to manage tension keeps the belt securely aligned with other pulleys, reducing maintenance needs and operational interruptions.
types of pulley in conveyor belt
5. Bend Pulley
Typically found on the return side of the conveyor system, bend pulleys help change the belt's direction. Proper configuration of bend pulleys can facilitate smoother operations, particularly in complex systems that require a high degree of maneuverability. Ensuring these pulleys are of robust construction is crucial for bearing the stresses of high-tension applications in heavy-duty industries like mining and material handling.
6. Wing Pulley
Wing pulleys are distinguished by their unique design, featuring vanes that project from the center axis like spokes. This innovative design enables debris to be easily expelled from the belt, significantly reducing the risk of build-up that could cause damage or inefficiency. Experts recommend wing pulleys for environments where material spillage and residue build-up are of concern, as they enhance the lifespan of the conveyor system by minimizing cleaning and maintenance intervals.
7. Live Shaft vs. Dead Shaft Pulleys
Understanding the differentiation between live shaft and dead shaft pulleys can directly impact the conveyor’s maintenance strategy. Live shaft pulleys come with internal bearings and bolts, facilitating easier installation and lower initial costs. In contrast, dead shaft pulleys are constructed with an immobile shaft, offering superior stability and better load distribution, which is crucial for high-capacity applications. Selecting the appropriate type based on operational load and maintenance capabilities can provide a significant advantage.
Incorporating these specialized pulleys is not merely about maintaining the conveyor belt’s functionality. It is about enhancing productivity and ensuring long-term operational success. By leveraging expertise in selecting the right pulleys for specific conveyors, businesses can reduce maintenance costs, minimize downtime, and optimize overall system performance. For industrial sectors relying heavily on conveyor systems, informed pulley choice is a decisive factor for competitive advantage, operational safety, and longevity.