Conveyor belt pulleys, integral to the functionality of conveyor systems, come in various types, each tailored to specific applications. Understanding these differences not only enhances operational efficiency but also extends the lifespan of conveyor systems. Below is a detailed exploration of the essential types and their distinct roles in material handling systems, drawing from decades of industry experience and expertise.
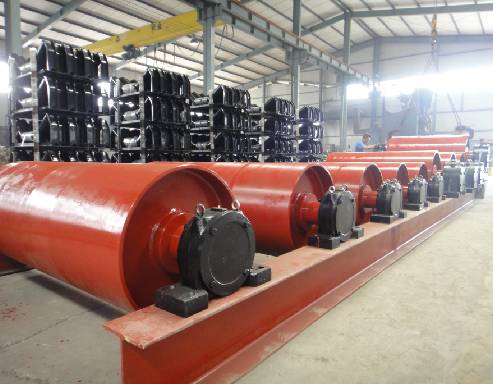
1. Drum Pulleys
Drum pulleys are the most common type employed in various industries. Characterized by their cylindrical shape,
they are designed to support the conveyor belt's weight and movement. Constructed from steel or aluminum, drum pulleys are renowned for their durability and robust construction, making them suitable for heavy-duty applications. Their versatility allows them to be used in numerous orientations, whether as a head, tail, or snub pulley.
2. Wing Pulleys
Primarily used in wet or very dirty environments, wing pulleys play a critical role in preventing material build-up on the belt. Their design, featuring a series of wings or fins, encourages material to fall away from the contact surface, reducing maintenance requirements and potential belt damage. By improving belt traction, they significantly contribute to the reliability and efficiency of conveyor operations, especially in industries like mining or aggregate processing.
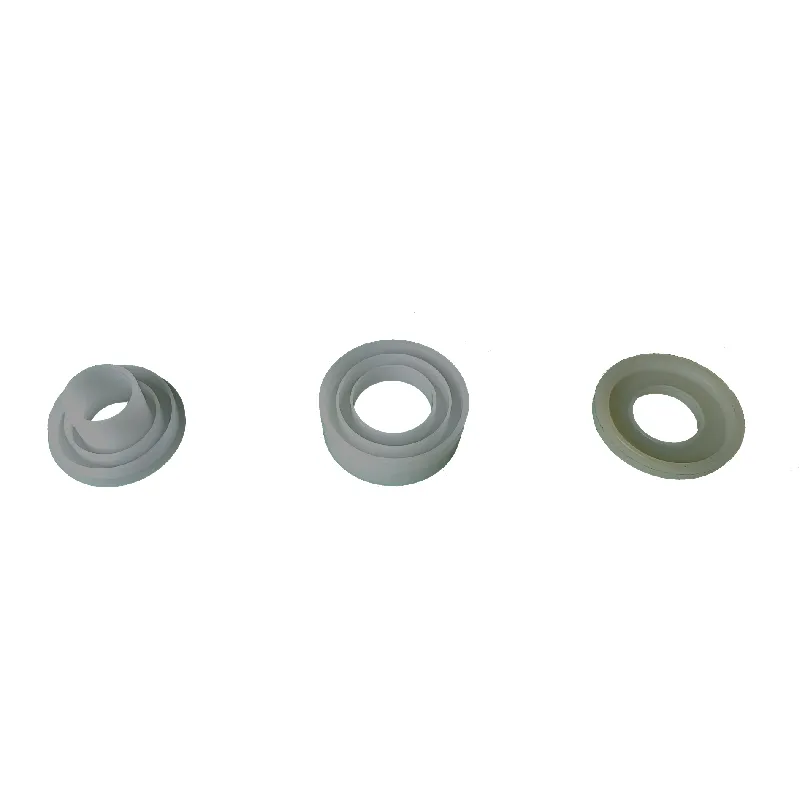
3. Lagged Pulleys
Lagged pulleys, equipped with a layer of material such as rubber on their surface, are engineered to enhance the grip between the pulley surface and the conveyor belt. This grip is crucial in high-torque applications and wet conditions where slippage might occur. The lagging material can also extend pulley and belt life by reducing wear and tear. These pulleys are indispensable in environments where temperature fluctuations or moisture might affect belt tension.
types of conveyor belt pulleys
4. Tapered Pulleys
Used in applications where conveyor belt direction changes, tapered pulleys assist in reducing wear and tear on the belt edges. Their conical design helps align the belt automatically, minimizing the risk of misalignment that could lead to significant operational downtime. Industries with complex conveying tasks greatly benefit from the deployment of tapered pulleys, as they offer a solution that promotes longevity and reduces maintenance intervals.
5. Motorized Pulleys
Also known as drum motors, motorized pulleys offer a compact and efficient option for driving conveyor belts. They house motors within the pulley body itself, eliminating the need for external motor drives or chains. This contained design reduces maintenance, improves hygiene (important in food processing), and maximizes efficiency by minimizing power loss. Installation is straightforward, and their sealed construction prevents ingress of dust or water, making them highly reliable in diverse conditions.
6. V-Groove Pulleys
These specialized pulleys are utilized when high-tension applications are necessary. The grooved design enhances the belt's grip on the pulley, reducing slip and improving power transmission. This makes V-groove pulleys ideal for situations where heavy loads are involved or where precise movement is required.
The selection of a conveyor belt pulley is dictated by numerous factors including material type, operational environment, and specific functional requirements. By leveraging insights from experts who have honed their craft over years in the industry, choices can be tailored to deliver maximum reliability, efficiency, and lifespan for the entire conveyor system. Recognizing the subtle yet crucial distinctions between pulley types ensures that systems are not only optimized for today’s demands but are resilient against the challenges of tomorrow.