Troughing rollers play a pivotal role in the efficiency and effectiveness of conveyor systems across various industries, including mining, agriculture, and manufacturing. As specialized components, troughing rollers ensure that materials are transported smoothly and securely along the conveyor path. Their design and function not only enhance productivity but also minimize downtime and maintenance costs, adding significant value to operations.
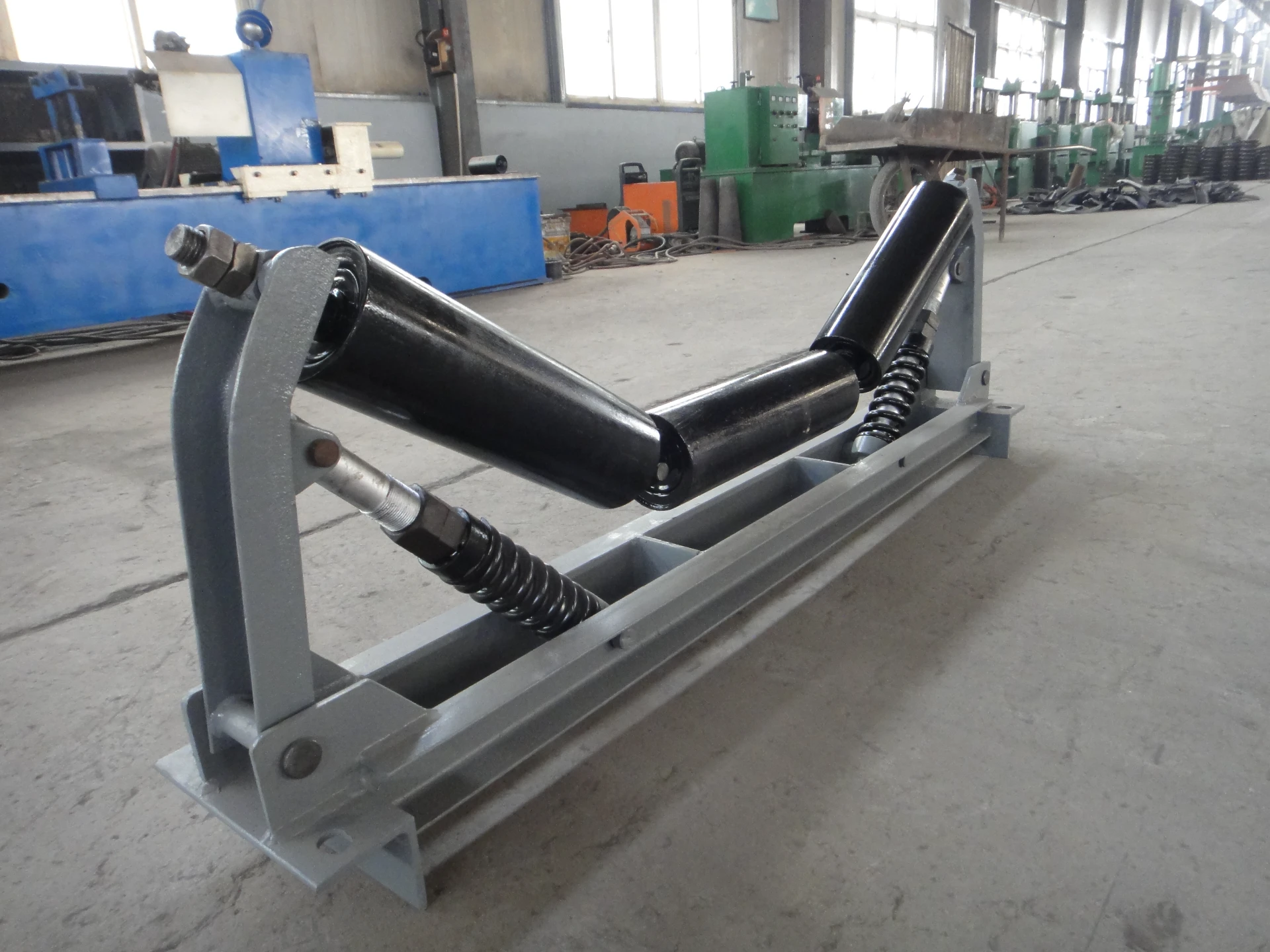
One of the most noticeable advantages of troughing rollers is their ability to maintain the alignment and stability of the conveyor belt. These rollers are strategically positioned along the carrying side of the belt, contoured to form a trough shape. This unique design concept enhances the belt's ability to contain bulk materials, preventing spillage and ensuring consistent material flow. Unlike flat rollers, troughing rollers handle larger volumes more efficiently by reducing the chances of overflow, which significantly improves operational throughput.
The expertise behind the design of troughing rollers lies in the understanding of dynamic loads and the varying characteristics of transported materials. Engineers pay close attention to the angle of the trough (typically 20, 35, or 45 degrees) to match the specific requirements of different materials and conveyor systems. This degree customization ensures that the troughing roller setup maximizes load-carrying capacity and minimizes wear on both the belt and the rollers themselves. By optimizing the belt contact area, these rollers also reduce the frictional forces between the belt and the rollers, thereby extending the longevity of both components.
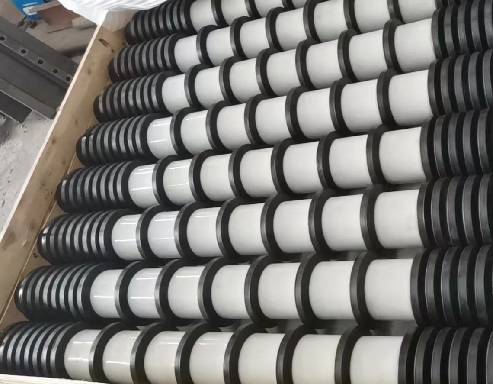
Choosing high-quality troughing rollers is a critical decision that can impact the entire conveying system's reliability and performance. Manufacturers often construct these rollers using robust materials like steel or high-impact plastics, which are selected based on the operational environment and the material's abrasiveness being transported. The selection process demands a thorough understanding of the system's demands, from load conditions to environmental exposure, to ensure the rollers provide consistent performance under diverse conditions.
Expertise in maintenance and regular inspection forms the backbone of ensuring peak operational efficiency with troughing rollers. Scheduled inspections should focus on identifying signs of wear and tear, such as unusual noises, increased resistance, or visible damage to the roller surface. Proactively addressing these issues can prevent minor problems from escalating into significant downtime events, illustrating the importance of a well-planned maintenance strategy.
troughing roller
The authority of troughing roller solutions is often demonstrated through their integration into comprehensive conveyor system designs. By engaging with established suppliers who offer custom solutions and expert consultation, businesses can optimize their conveyor operations to align with specific production goals. These suppliers not only provide the rollers themselves but also deliver insights into system enhancements, contributing to greater overall organizational efficiency and profitability.
Building trust in troughing roller solutions extends beyond the immediate functional benefits. By investing in high-quality rollers and adhering to a disciplined maintenance routine, companies position themselves as responsible operators within their industries. This dedication to operational excellence not only boosts internal productivity but also enhances external perceptions of reliability and commitment to quality.
Finally, embracing advancements in roller technology, like self-cleaning designs and sensor integration for predictive maintenance, can yield additional long-term benefits. By staying at the forefront of conveyor technology, businesses demonstrate their commitment to leveraging cutting-edge solutions, ensuring their operations are as reliable and efficient as possible.
In conclusion, troughing rollers are indispensable to the successful operation of conveyor systems.
Their design intricacies and material handling capabilities provide a blend of stability, efficiency, and durability. When expertly integrated with maintenance and system optimization insights, they empower industries to achieve seamless material transportation, minimize operational hiccups, and elevate production standards to new heights.