In the intricate world of conveyor systems, the tail drum pulley emerges as an unsung hero, ensuring seamless operations across industries, from mining to food processing. This crucial component might not be in the limelight like its more famous counterparts, but its role is undeniably pivotal. With over 20 years of experience in industrial mechanics and equipment optimization, I've witnessed firsthand the profound impact that a high-quality tail drum pulley can have on operational efficiency and system longevity.
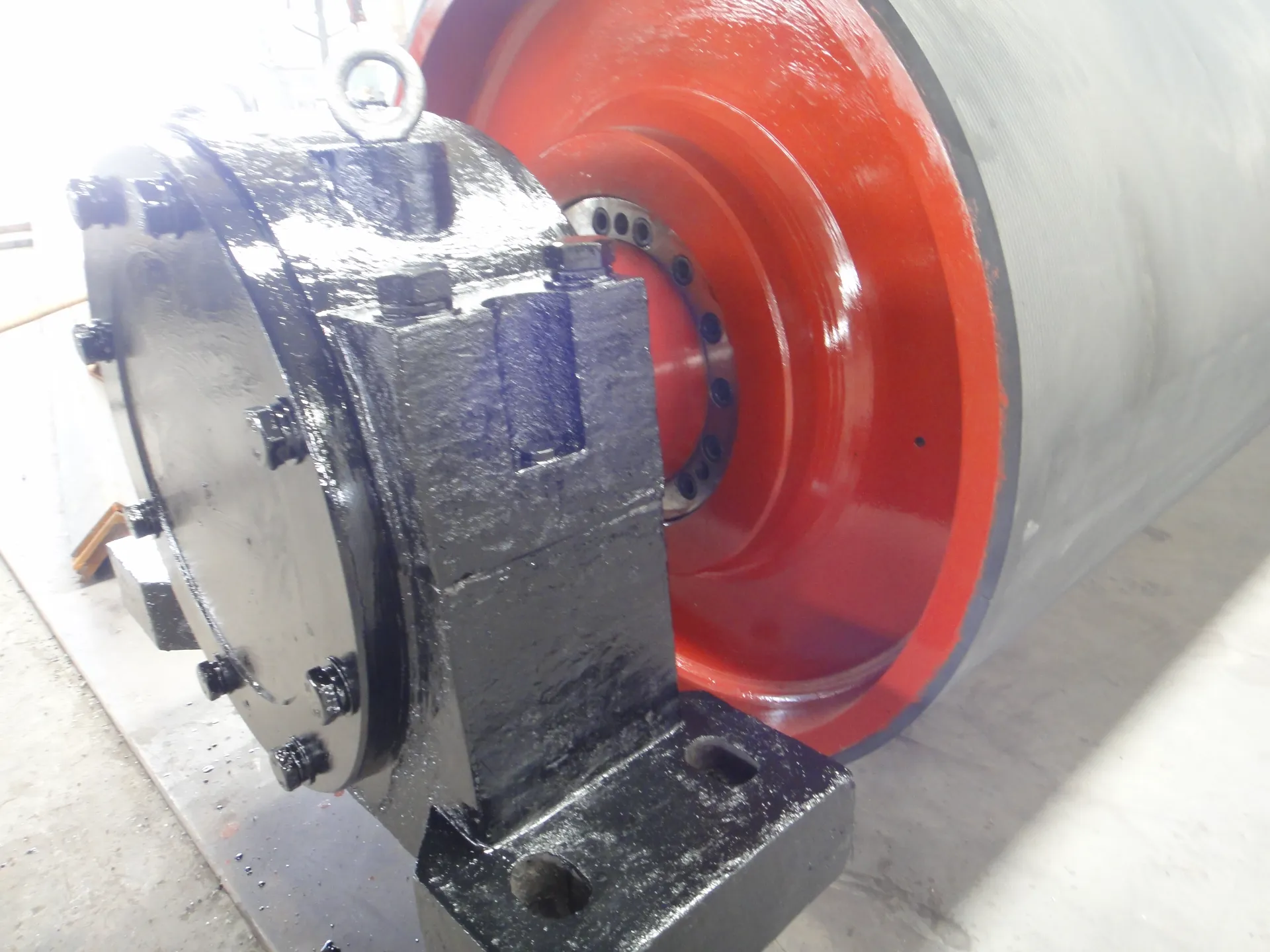
The tail drum pulley stands at the end of a conveyor belt system, playing the vital role of redirecting the belt back to the drive pulley, ensuring continuous movement. Without it, the synchronization that propels the conveyor into motion would falter, leading to costly downtimes and disrupted workflow. The durability and reliability of a tail drum pulley directly influence a system's productivity, making its selection and maintenance critical.
My journey through different manufacturing environments has taught me that not all tail drum pulleys are created equal. Factors such as material composition, surface finish, and balancing directly affect their performance. A well-engineered tail drum pulley, crafted with precision from materials like stainless steel or high-impact polymers, offers remarkable resistance to wear and environmental conditions, providing a robust solution for any industrial setting. The expertise in selecting the right material can transform a potentially weak link into the backbone of a conveyor system.
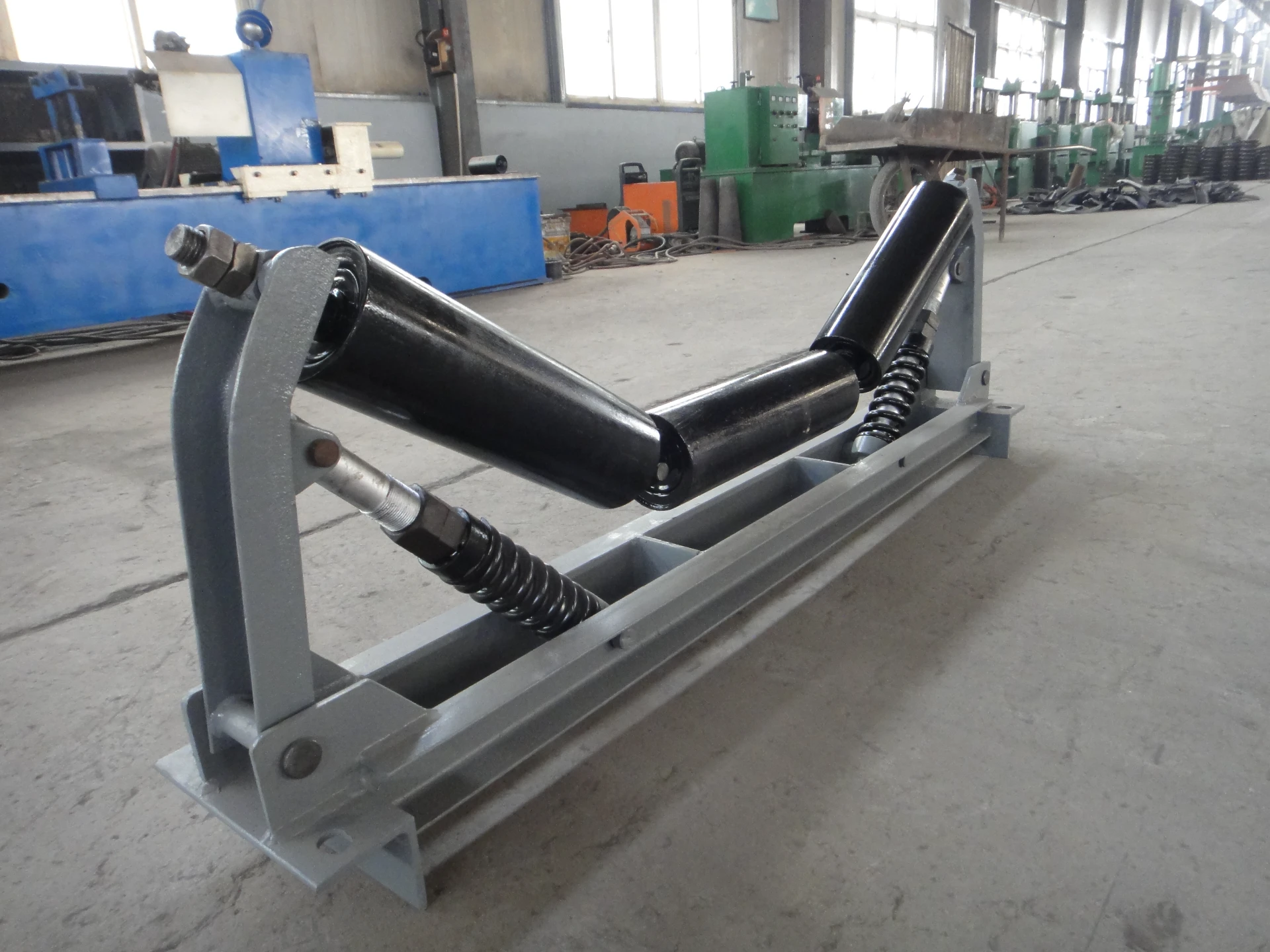
I recall an incident at a mining site several years ago, where frequent belt misalignments and premature wear were causing havoc. Upon closer inspection, the issue traced back to the poorly designed tail drum pulley. By upgrading to a dynamically balanced, corrosion-resistant model, specifically designed to handle abrasive materials, the site experienced a drastic reduction in maintenance interventions and a significant boost in productivity. This change not only underscored the importance of expert consultation but also showcased the tail drum pulley's contribution to operational excellence.
tail drum pulley
A key to maximizing the efficacy of these pulleys lies in regular maintenance and inspections. Over time, even the sturdiest pulleys can succumb to wear and tear—bearing failures, shaft misalignment, and surface degradation being some common issues. Regular checks and predictive maintenance can preempt these problems, ensuring the tail drum pulley continually performs at its best. Implementing a comprehensive maintenance schedule, informed by cutting-edge diagnostic tools, not only prolongs the lifespan of the pulley but enhances the overall trustworthiness of the conveyor system, reducing unexpected breakdowns.
Moreover, leveraging technological advancements can provide substantial returns. Today’s market offers smart tail drum pulleys equipped with sensors that monitor performance in real-time, alerting operators to potential failures long before they occur. This innovation marks a new era of preventative maintenance where a tail drum pulley doesn't just drive a belt but actively participates in the decision-making process about its upkeep, highlighting the ongoing evolution of industrial equipment intelligence.
Decades of on-site experience have taught me that a misunderstood or underestimated tail drum pulley can inadvertently become a bottleneck in an otherwise efficient system. This insight positions the tail drum pulley as an indispensable component not just in role, but in the strategic decisions regarding machine investments and maintenance.
To synthesize the many nuances I’ve encountered, an authoritative stance on the importance of selecting and maintaining the right tail drum pulley offers invaluable insights across industries. The true value of an optimized tail drum pulley becomes evident through augmented productivity, decreased downtimes, and overall better strategic resource allocation. Accurate, practical decisions regarding this underappreciated yet essential component can effectively turn the wheels of progress, literally and figuratively, ensuring systems operate at peak capability. By tapping into these insights, operations can gain a competitive edge, firmly establishing their reliability and authority in their respective domains.