Idler rollers with bearings are an essential component in various industrial applications, serving as a pivotal part in conveyor systems, machinery setups, and other mechanical assemblies. Their role, though often underappreciated, is critical in reducing friction, guiding materials, and ensuring the smooth operation of equipment.
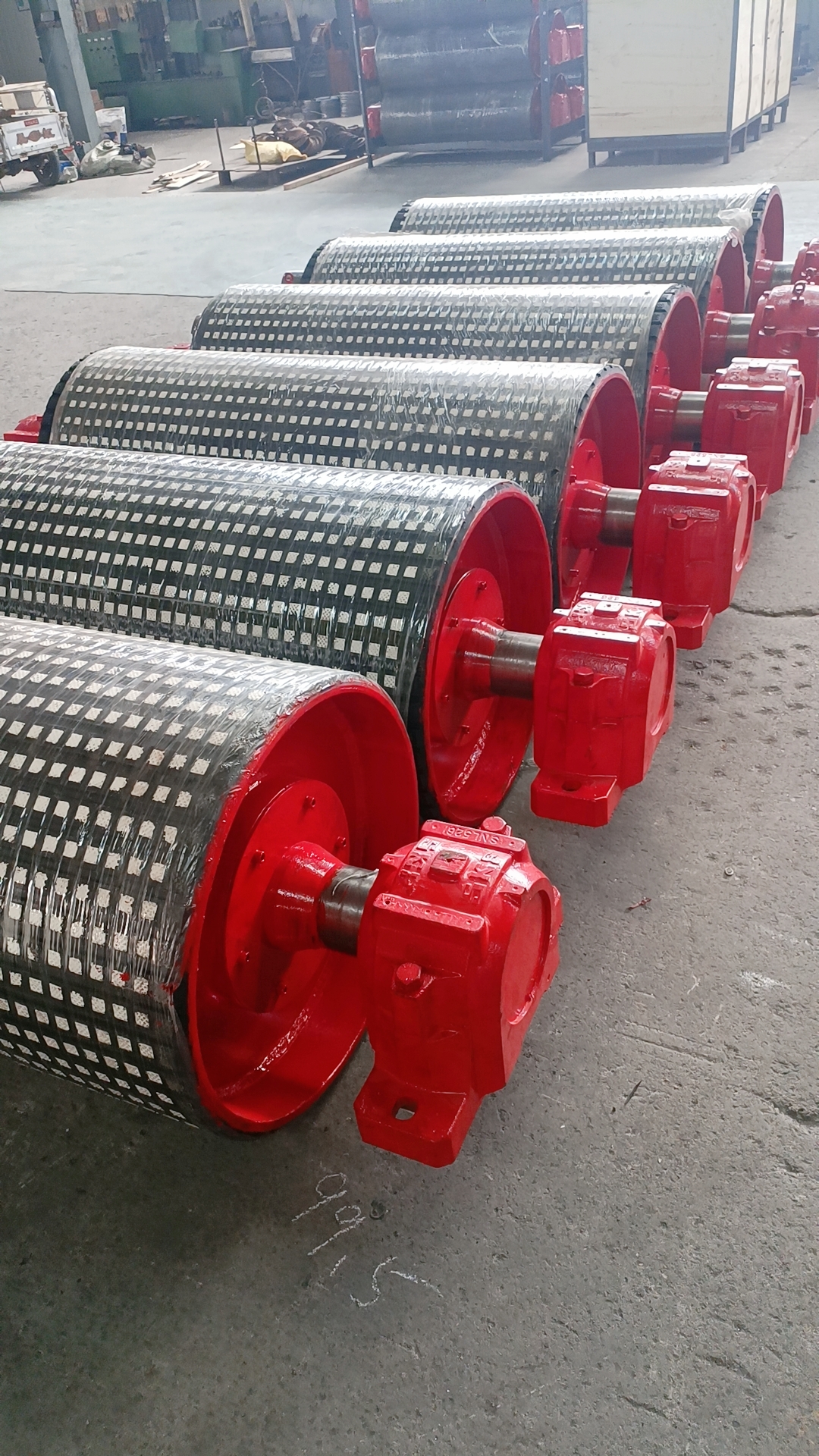
The intricacies of idler rollers with bearings can be broken down into key elements such as design, material selection, and operational efficiency. Understanding these elements can differentiate between a standard product and one that offers substantial improvements in performance.
Design is the cornerstone of a quality idler roller with bearings. Typically constructed with a robust core, these rollers must support different weights and fulfill specific rotational demands. The core might be made of steel, aluminum, or high-strength polymers, each providing unique benefits relating to weight, durability, or resistance to environmental factors. Similarly, the outer shell of the roller is crafted to withstand wear and tear, often utilizing materials like polyurethane or vinyl, which cater to different conveyor belt interactions and longevity requirements.
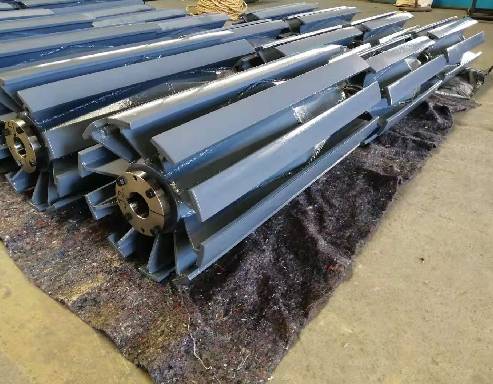
Incorporating bearings within these idler rollers elevates their functionality by facilitating low-friction movement and enhancing the roller’s lifespan. A diverse range of bearings, such as ball bearings or cylindrical bearings, can be integrated based on load requirements and operational speed. Bearings must be chosen to match the specific needs of the application for optimal performance and to reduce the need for frequent maintenance. Seal design further augments bearing utility by protecting it from contaminants that could compromise efficiency and durability.
Material selection for idler rollers with bearings bears great significance, directly impacting the product's efficiency and functionality. Metals like stainless steel are preferred in environments with corrosive agents or extreme temperatures, providing a balance between strength and resistance to adverse conditions. Conversely, polymer-based rollers are often used in scenarios where noise reduction and lightweight properties are prioritized.
idler rollers with bearings
Operational efficiency of idler rollers with bearings is measured by their ability to minimize energy consumption while maximizing output. An efficiently operating roller aids in reducing operational costs by extending the life of conveyor belts and minimizing energy usage. Advanced engineering and quality manufacturing processes ensure that these components can handle higher load capacities with minimal rotational resistance.
For anyone evaluating idler rollers with bearings, it’s crucial to consider the product from a holistic perspective, weighing factors such as compatibility with existing systems, maintenance requirements, and cost-efficient life-cycle performance. Providers of these components often come with varying degrees of expertise; therefore, choosing a supplier with a proven track record of reliability and technical support can make a substantial difference in overall system performance.
Companies investing in idler rollers with bearings should look beyond the purchase price, focusing on the total cost of ownership which includes installation, maintenance, downtime, and replacement intervals. A trusted manufacturer will offer insights and testing methodologies to ensure that the selected rollers are tailored to the bespoke needs of any given application, further reinforcing longevity and reliability.
In conclusion, idler rollers with bearings are much more than mere components within a machine; they are integral elements that contribute significantly to the functionality and efficiency of industrial processes. Expertise in selection, understanding of material properties, and evaluation of design considerations align to provide a solution that supports continuous, trouble-free operation, enhancing overall productivity and profitability.