Seal rollers are indispensable tools in a myriad of industrial and construction applications, offering both efficiency and precision in sealing tasks. Understanding their unique features and applications can significantly enhance operational productivity and ensure the longevity of seals across various industries.
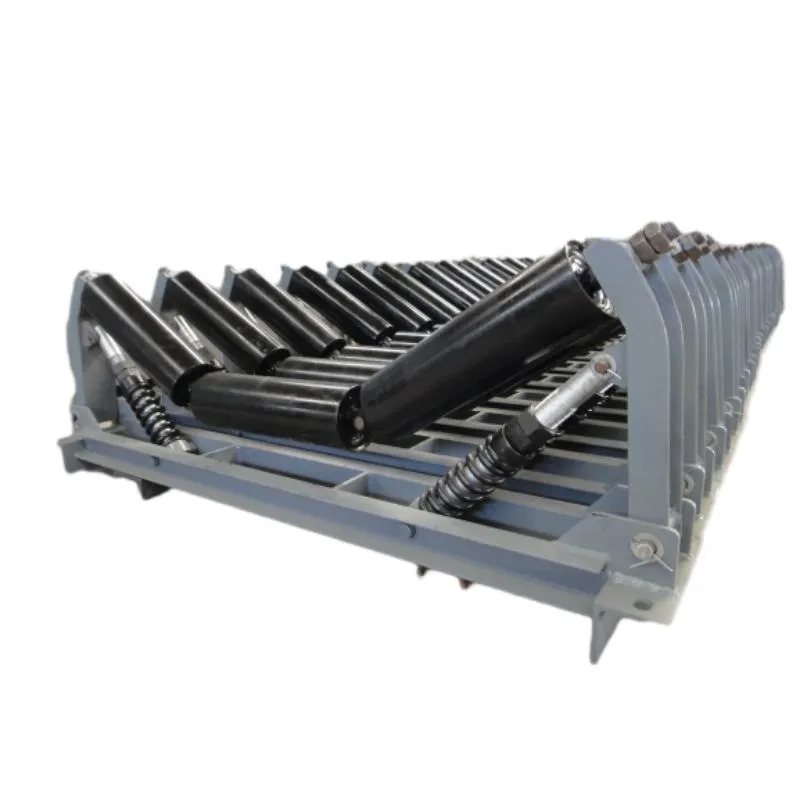
Crafted with ergonomics in mind, seal rollers are engineered to apply consistent pressure during seal installations.
This ensures that seals adhere properly, preventing leaks and potential failures in sealed joints. The precision offered by seal rollers not only enhances the quality of the seal but also reduces material waste and minimizes the time required for fixing improper seals, thus improving operational efficiency.
The expertise in selecting the right seal roller involves understanding the materials being sealed as well as the environment in which the seal will operate. These tools are constructed from various materials, including rubber, silicone, and polyurethane, each suited to specific types of seals and applications. Rubber rollers, for instance, are often preferred in applications involving delicate materials due to their flexibility and soft touch. In contrast, polyurethane rollers offer superb abrasion resistance and are ideal for more demanding applications.
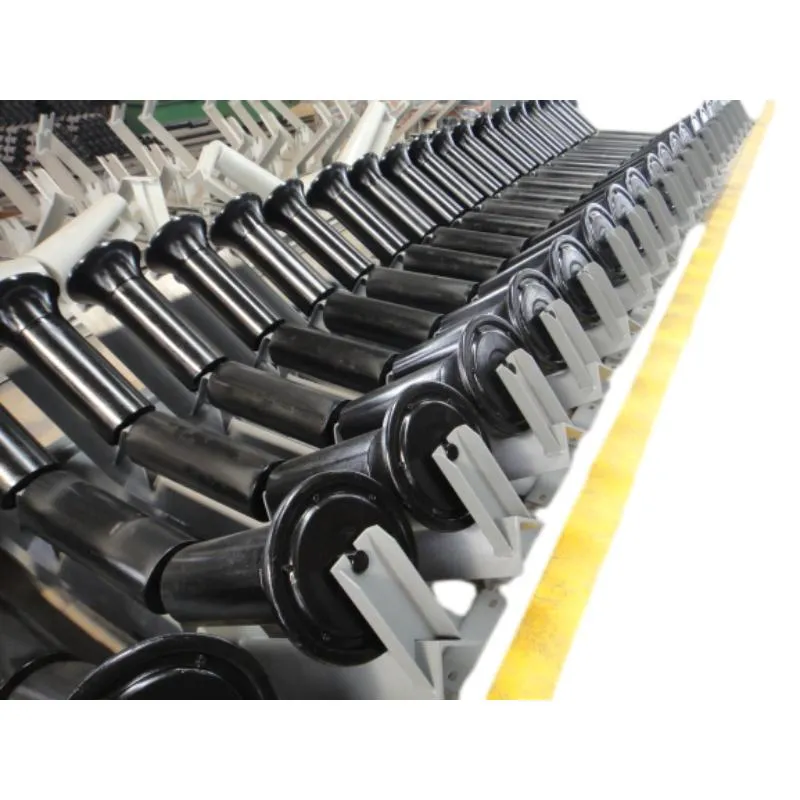
Authoritativeness in the realm of seal rollers is demonstrated through adherence to industry standards and innovations that enhance performance. Industry leaders continually research and develop new materials and technologies to increase the durability and effectiveness of seal rollers. For instance, advancements in the design of rollers with variable durometer levels contribute to adaptable pressure application, suitable for a wide range of sealing surfaces—from smooth metal to textured rubber.
seal roller
Trustworthiness in the manufacture and application of seal rollers is critical. Reputable manufacturers conduct rigorous testing to ensure that each roller meets high standards for both durability and performance. Additionally, user reviews and case studies are valuable resources for verifying the reliability of a particular brand or model. Real-world applications highlight the importance of choosing the right tool for the job—whether for sealing automotive windshields or securing industrial-grade pipe joints.
In terms of experience, consider the insights from industry professionals who work with seal rollers daily. They emphasize the significance of proper maintenance and handling to extend the lifecycle of these tools. Regular cleaning and inspection for wear and tear are recommended practices to maintain the roller's effectiveness. Moreover, understanding the correct technique—such as maintaining a consistent rolling speed and pressure—ensures optimal results and minimizes rework.
Discussing the economic implications, seal rollers represent a cost-effective solution in sealing operations. Their ability to enhance sealing accuracy reduces the likelihood of costly re-sealing efforts and prevents downtime caused by seal failures. As industries strive to improve sustainability, the role of seal rollers becomes more pronounced, enabling efficient use of materials and resources, which contributes to a reduced environmental impact.
In conclusion, seal rollers are a pivotal component in ensuring reliable and efficient sealing across numerous applications. Mastery over their selection, usage, and maintenance can significantly enhance an industry professional's skill set, driving improved outcomes in both quality and efficiency. By choosing the appropriate seal roller and applying it with precision, industries not only uphold standards of operational excellence but also contribute to broader objectives of sustainability and resource optimization.