Rubber lagging pulleys are pivotal in the machinery and industrial sectors, serving as essential components in conveyor systems and other machinery applications. These pulleys are engineered with a layer of rubber on the surface to maximize the grip and improve friction between the belt and the pulley, ensuring the seamless operation of conveyor systems. Understanding the intricate details of rubber lagging pulleys not only aids in selecting the right product but also enhances operational efficiency and system longevity.
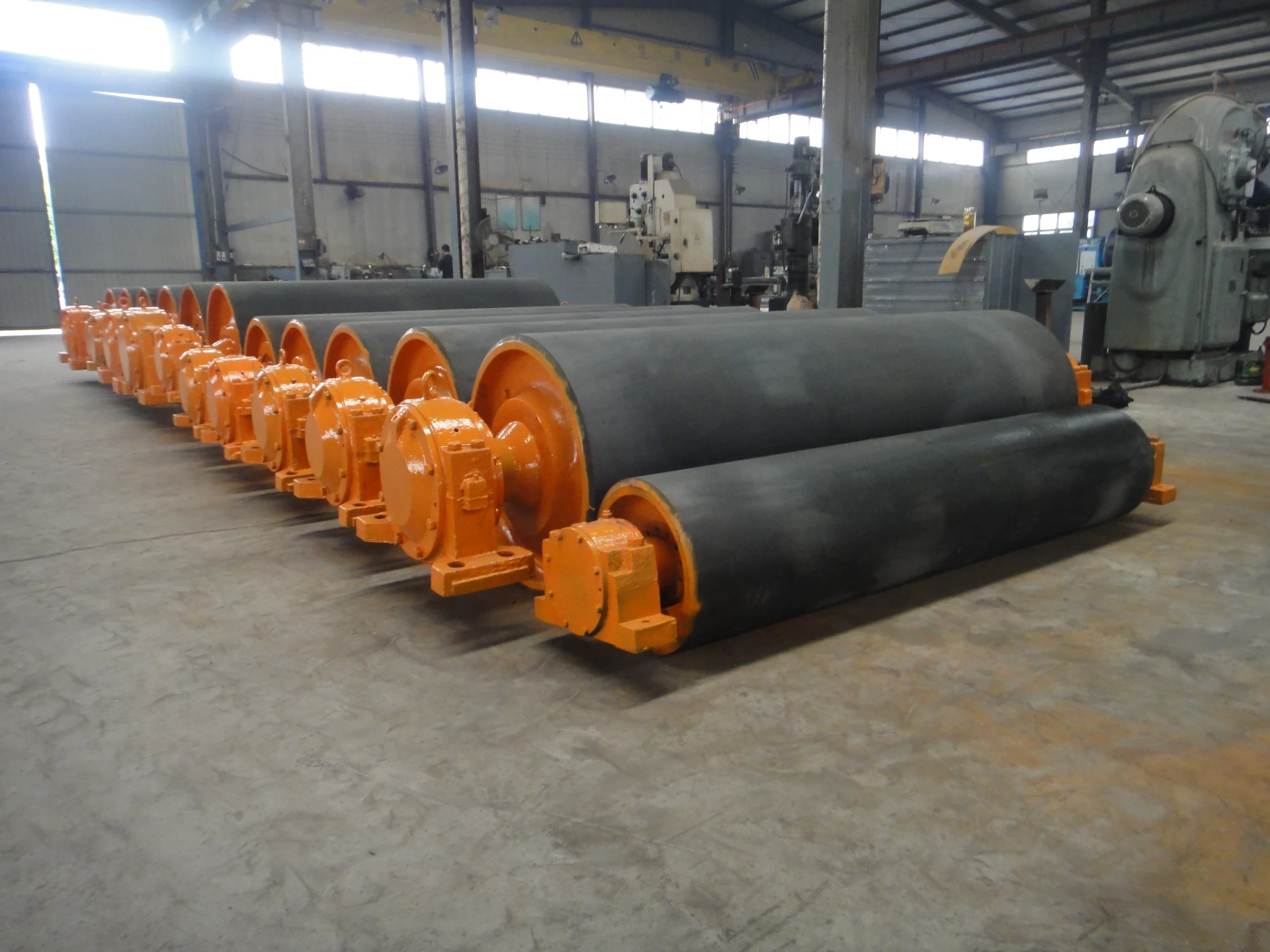
The primary advantage of rubber lagging pulleys lies in their ability to minimize slippage, a common problem in conveyor systems. Slippage can lead to untimely wear, increased maintenance costs, and operational inefficiencies. By utilizing rubber lagged pulleys, industries can significantly reduce downtime and improve productivity. The rubber surface of the pulley provides increased grip, making it possible to operate belt systems at reduced tension without risking belt misalignment or slippage, thus promoting longer belt life.
Beyond preventing slippage,
rubber lagging also offers noise reduction benefits. In environments where heavy machinery is already a source of significant noise pollution, the added rubber layer acts as a dampener, absorbing operational sounds and contributing to a quieter workplace. This aspect is crucial for industries keen on adhering to health and safety regulations, which often include strict noise management policies.
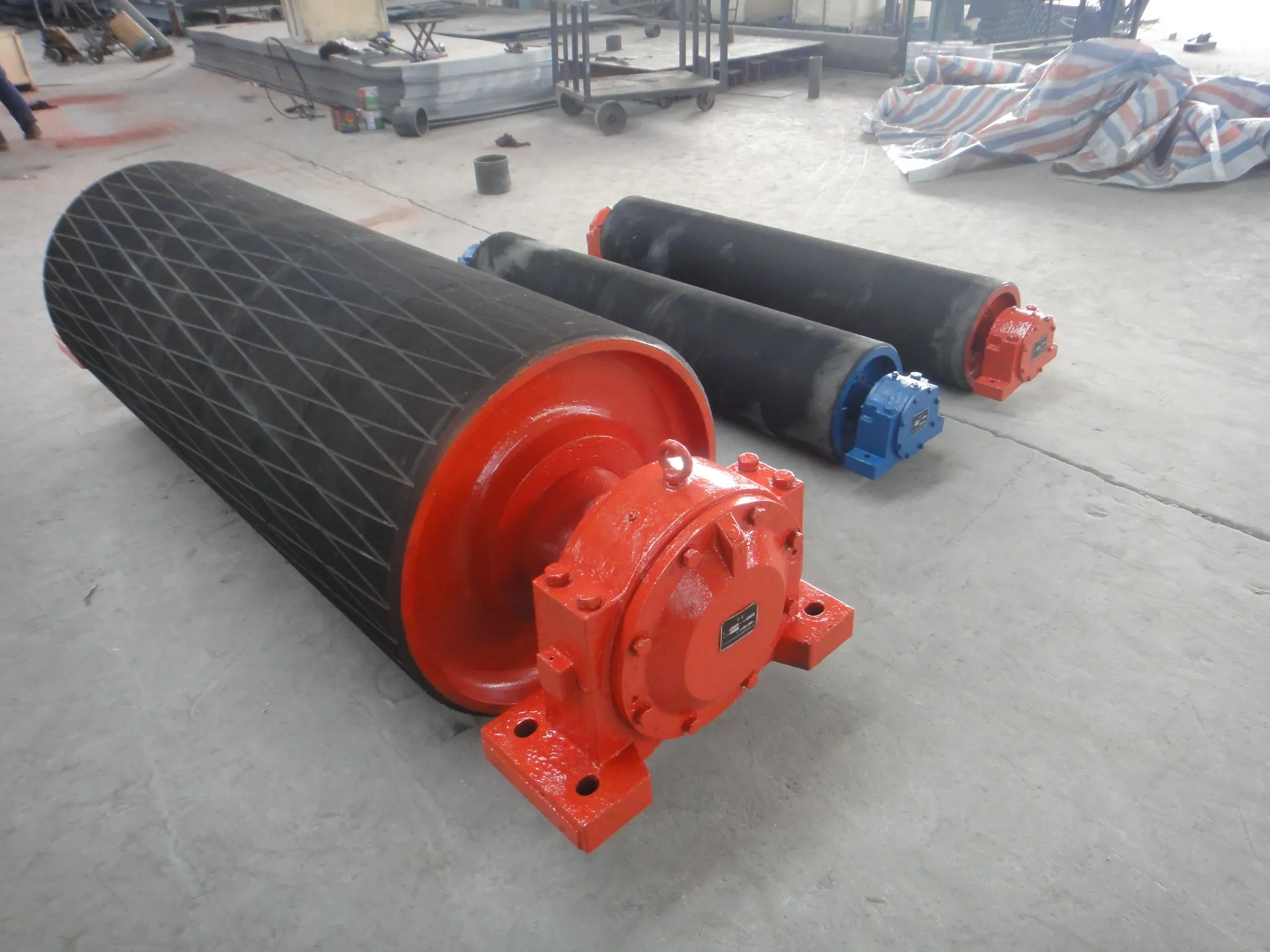
Rubber lagging comes in various formulations, each designed to tackle specific industrial challenges. For example, diamond-patterned lagging is often recommended for humid environments where water might increase the risk of belt slippage. This pattern allows for water dispersion, akin to tire treads on a wet road. On the other hand, plain pattern lagging might be used in applications where maximum belt cover is necessary. Selecting the correct rubber compound, whether natural, synthetic, oil-resistant, or flame-retardant, can exponentially enhance pulley performance and service life.
rubber lagging pulley
Expertise in understanding and deploying the right type of rubber lagging pulley lies at the heart of optimizing industrial workflows. It demands a careful evaluation of the working environment, material conveyed, belt type, and expected load. For instance, a heavy-duty mining operation would require a different rubber specification compared to a food processing facility, where cleanliness and non-toxicity are paramount. Such an assessment ensures that the pulley system meets specific operational demands while adhering to safety and environmental standards.
Rubber lagging pulleys contribute to the broader environmental objectives by facilitating efficient resource management. By reducing energy consumption and prolonging equipment life, they help industries lower their carbon footprint. Advanced rubber technologies continue to evolve, offering eco-friendly and sustainable options that do not compromise on performance.
Notably, the authoritative presence of rubber lagging pulley experts is indispensable for industry conferences and knowledge-sharing platforms. Sharing case studies and real-world evidence of pulley performance allows stakeholders to make informed decisions, cultivating a community of trust and mutual growth. Industry leaders and manufacturers often engage in collaborative ventures to gather field data, validating best practices and disseminating expertise across the board.
In essence, rubber lagging pulleys are more than just components; they are integral to the operational excellence of various industries. Their potential to improve safety, efficiency, and sustainability while minimizing costs speaks to the ever-evolving nature of industrial technology. For stakeholders seeking to refine conveyor operations, understanding the versatile applications and benefits of rubber lagging pulleys is a step toward future-proofing their endeavors.