Rubber drive pulleys, a seemingly mundane component, play a pivotal role in various industrial applications, affecting efficiency and performance in areas ranging from conveyor systems to precision machinery. These components are not merely tools of motion transmission; they are engineering marvels that require a deep understanding of materials, design, and application to maximize their utility.
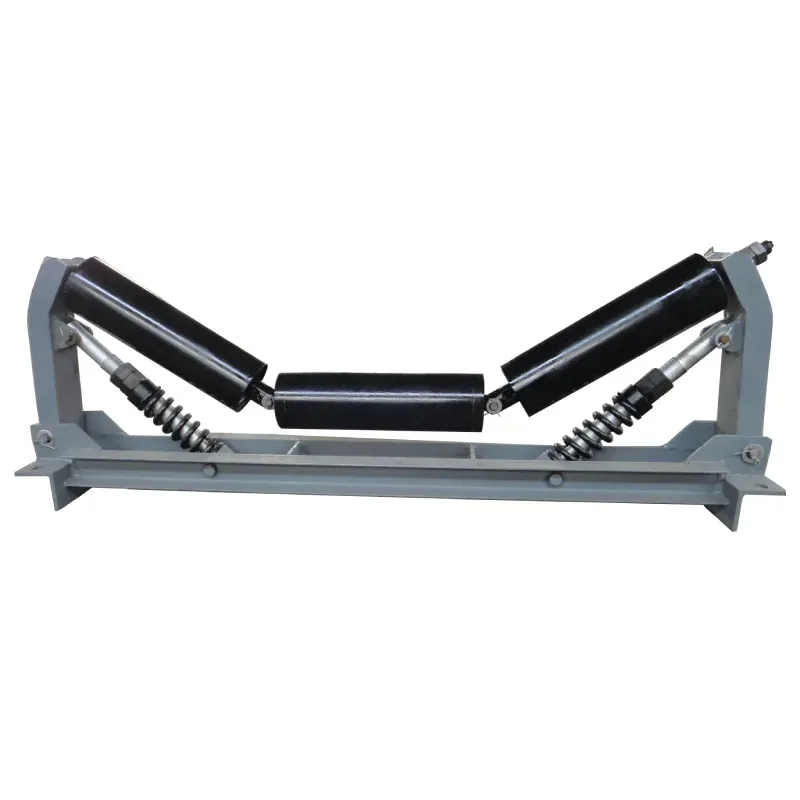
In the intricate dance of industrial mechanics, the rubber drive pulley serves as a linchpin, balancing force transmission with material resilience. These pulleys are often crafted from high-grade rubber, chosen for its superior flexibility, grip, and durability. Unlike metallic counterparts, rubber pulleys provide excellent shock absorption, which is critical in protecting the machinery and extending the lifespan of both belts and conveyor systems.
Experience in various fields demonstrates that selecting the appropriate rubber compound is vital. Industry veterans often rely on specific blends tailored to the demands of the environment. For instance, in high-temperature conditions, silicone rubber pulleys excel due to their thermal resistance. In contrast, environments exposed to oils or harsh chemicals may require nitrile rubber, known for its chemical resistance.
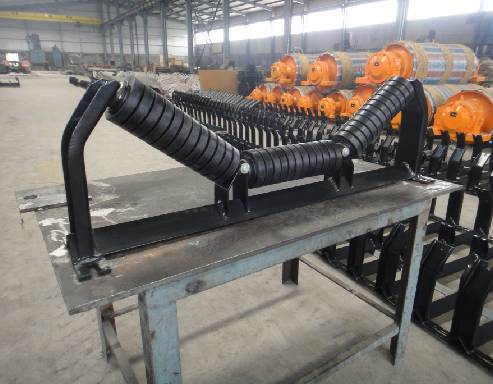
A common application of rubber drive pulleys is in conveyor systems, notably in those used within manufacturing and material handling sectors. Here, the choice of pulley impacts the system's overall energy efficiency. Rubber pulleys decrease the slippage rate, ensuring that the belt moves smoothly with minimal power loss. This efficiency not only conserves energy but also reduces operational costs, a significant advantage in large-scale operations.
From an engineering perspective,
expertise in pulley design is indispensable. Design considerations include the pulley’s diameter, the groove profile, and the hardness of the rubber, all of which influence the torque capacity and operational smoothness. Professionals with expertise in this area understand the interplay between these factors and tailor their specifications to fit specific operational needs, ensuring maximal output.
rubber drive pulley
Insights from authoritative sources suggest that maintenance plays a crucial role in maintaining the functionality of rubber drive pulleys. Regular inspection ensures the early detection of wear such as cracking or material degradation, which can compromise the system's efficiency. Trusted industrial practitioners advocate for the implementation of a predictive maintenance strategy. Using tools such as infrared thermography, potential issues can be identified before they escalate into costly downtimes.
Ensuring the longevity and effectiveness of rubber drive pulleys also involves embracing technological advancements. Current research emphasizes the development of composite materials, which enhance the pulley's strength while maintaining the essential flexibility of rubber. Experts in the field are exploring the use of biodegradable rubber blends, addressing environmental concerns and aligning with sustainable industrial practices.
The trustworthiness of rubber drive pulleys as critical components in various industries is reinforced by rigorous testing and compliance with international standards like ISO and ANSI. In selecting a supplier, it is imperative that these qualifications are verified. This not only guarantees product reliability but also builds a foundation of trust in industrial partnerships.
In conclusion, the realm of rubber drive pulleys encompasses a complex array of considerations, from material selection and design to maintenance and technological innovation. Professionals in the field bring a wealth of experience and knowledge, ensuring that these components meet the rigorous demands of modern industry. As industries evolve, so too does the role of the rubber drive pulley, continuing to adapt and meet the challenges of tomorrow with resilience and efficiency.