Roller lagging is an essential component in numerous industries, offering a solution that enhances the performance and longevity of conveyor systems. For professionals seeking to optimize their operations, understanding the intricacies and benefits of roller lagging can make a substantial difference in efficiency and cost-effectiveness.
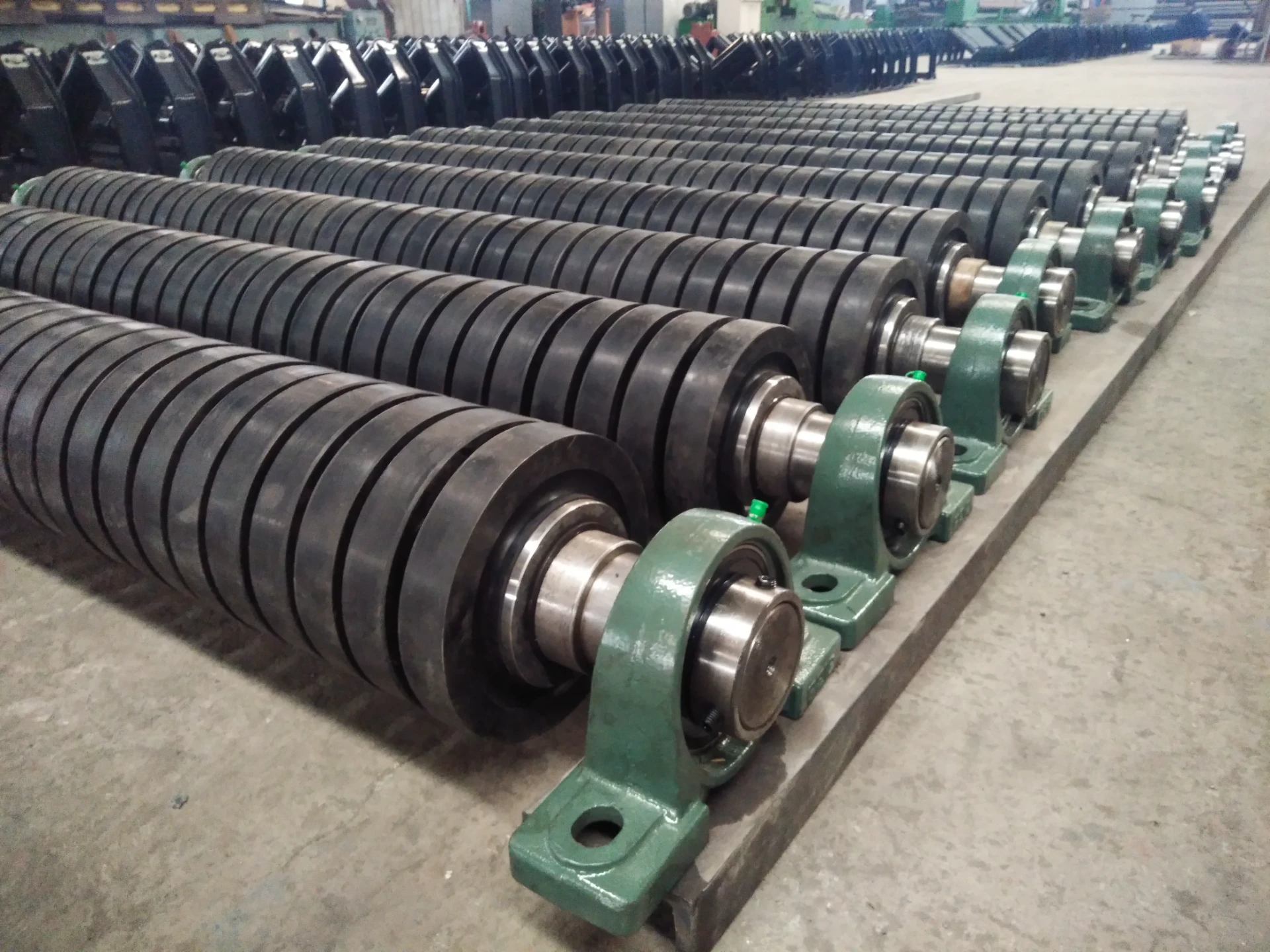
Roller lagging refers to the addition of material to pulleys or rollers, providing a wide array of benefits such as increased friction, minimized slippage, and enhanced longevity of the conveyor belts. The material used in lagging often depends on the specific needs of the application, ranging from rubber to ceramic. The choice of material can impact not just performance but also operational costs.
Experience has shown that properly applied roller lagging significantly improves the traction between the roller and the belt, which is critical for reducing downtime and maintenance costs. This improvement in traction can prevent excessive wear on both the roller and the conveyor belt, ultimately extending the life of the entire system. Companies utilizing this technology have reported decreased belt replacement and repair frequencies, resulting in significant cost savings over time.
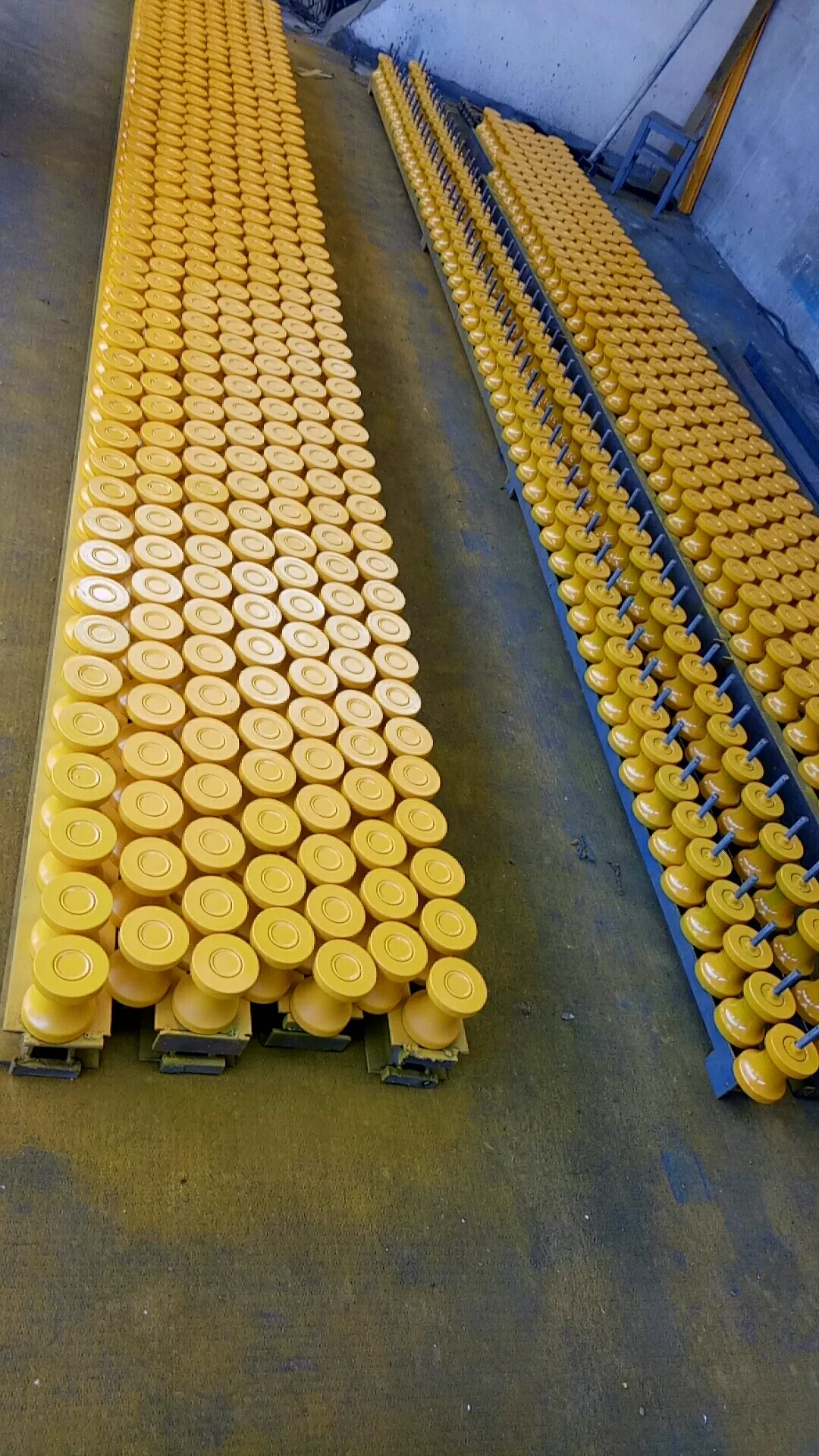
Expertise in roller lagging requires knowledge of various techniques such as cold bonding and hot vulcanizing. Each method has its advantages; cold bonding is often praised for its ease of application and effectiveness in different environmental conditions, while hot vulcanizing offers superior bond strength, making it ideal for demanding applications. Choosing between these methods will depend on specific operational requirements, such as temperature and workload conditions.
roller lagging
Authoritativeness in this field is often demonstrated by the use of certified, high-quality materials and adherence to industry standards during the application process. Reputable suppliers and manufacturers of roller lagging materials are committed to providing solutions that meet strict industry regulations, ensuring reliable and consistent performance. Companies that prioritize these standards are often better able to offer guarantees, which can be a deciding factor for businesses looking to invest in long-term, sustainable solutions for their conveyor systems.
Trustworthiness is built over time, through consistent quality and service. Companies with extensive track records in the roller lagging industry typically offer warranties and support that reassure their clients of their investment's value. They also invest in ongoing research and development to continuously offer better, more efficient materials and techniques. By fostering strong partnerships with their clients and maintaining transparency in their processes, these companies enhance their reputation for reliability and effectiveness.
For businesses considering roller lagging for the first time, consulting with a trusted expert in conveyor systems is crucial. These professionals can conduct a thorough assessment of current systems, identify potential improvements, and provide recommendations tailored to specific operational needs. Their insights ensure that companies receive maximum benefit, optimizing efficiency and reducing long-term operational costs.
In conclusion, roller lagging is a strategic investment for companies looking to enhance their conveyor systems' performance and lifespan. With the right choice of materials, application methods, and professional expertise, businesses can achieve significant improvements in their operational efficiency. By focusing on quality materials, trusted partnerships, and adherence to industry standards, companies secure their systems' reliability while positioning themselves competitively in their respective industries.