Pulley tail mechanisms have revolutionized various industrial applications, gaining a reputation for their efficiency and reliability.
These integral components use the mechanical advantage of pulleys to perform tasks more efficiently. Understanding them can help businesses and professionals harness their full potential in improving operational workflows.
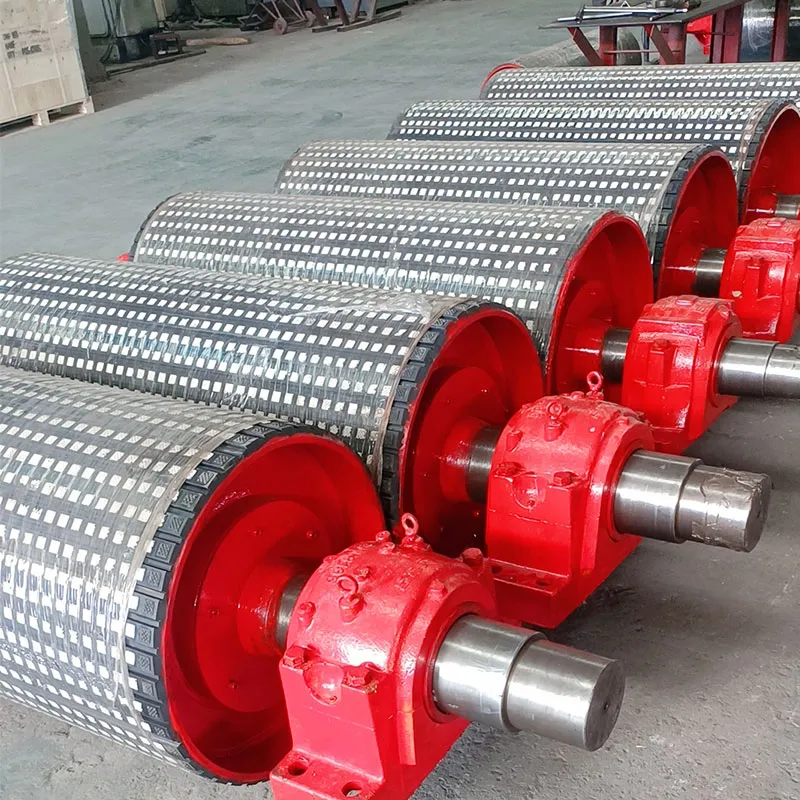
Pulley tail systems are often leveraged in settings where tensioning and guiding are crucial, and they play a vital role in conveyor systems, especially in sectors such as mining, manufacturing, and logistics. Their purpose is simple but significant they help maintain the tension needed to keep belts aligned and operational without slippage.
From an experiential standpoint, integrating pulley tail systems into your machinery lineup offers tangible benefits. For instance, in a manufacturing plant, using pulley tails in a conveyor belt setup drastically reduces maintenance needs. Unlike fixed pulley systems, pulley tails allow for automatic tension adjustment. This is particularly beneficial in operations where belts expand or contract due to load or temperature fluctuations. The immediate impact is a reduction in downtime and greater flexibility in handling materials of varying weights and sizes.
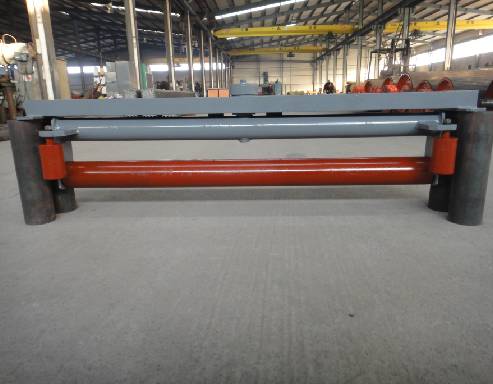
Expertise in deploying pulley tail systems requires understanding the specific needs of your operation. Selecting the right materials, sizes, and configurations ensures that the system will handle the operational load efficiently. Professionals in the field need to balance cost with the potential operational benefits. Engineers often recommend galvanized steel or stainless steel for environments exposed to moisture or chemicals, due to their resistance against corrosion and durability.
The authoritative aspect of pulley tails comes from their vital role in industry-standard conveyor systems. Many organizations attribute increased longevity and robustness of their conveyor systems to the precision engineered pulley tails they employ. For instance, in the agriculture industry, the use of pulley tails in grain handling conveyor systems has become standard practice. They not only facilitate seamless movement of bulky grains but also minimize spoilage by ensuring consistent belt movement and alignment.
pulley tail
Trustworthiness of these systems is reflected in their widespread adoption and proven track record across industries. Case studies from logistics companies show that integrating pulley tails can lead to a 15-20% increase in conveyor efficiency. This efficiency is measured in terms of reduced operational costs and increased throughput. A notable example is a logistics hub that reported enhanced sorting capabilities, which improved package handling precision and speed by adopting pulley tail systems.
For businesses considering a transition to pulley tail systems, several factors need to be weighed. It is crucial to perform an initial assessment of your current conveyor setup to ascertain necessary adjustments. Upgrading to a pulley tail system might require modifications to existing equipment, but the long-term benefits often outweigh initial investments. Consultants and industry experts typically recommend a phased approach, beginning with pilot tests to fine-tune the system to specific needs.
Finally, regular maintenance of pulley tail systems is essential to ensure peak performance and longevity. Scheduled inspections for wear and tear, prompt replacement of worn-out components, and ensuring proper lubrication are best practices to maintain efficiency. Training your maintenance teams or employing specialist services can prevent unwanted downtimes and associated costs.
In summary, pulley tail mechanisms are not just auxiliary components - they play a central role in enhancing operational efficiency and reducing costs across various industries. Leveraging their benefits requires a blend of understanding their mechanical nuances and tailoring them to fit specific industrial needs. With the right approach, businesses can transform their conveyor systems into highly efficient, low-maintenance assets.