Pulley rubber lagging is an indispensable component in various industrial sectors. Leveraging the right kind of lagging on your pulley systems significantly elevates operational efficiency, safety, and longevity. Let's delve into the intricacies of pulley rubber lagging, dissecting its expertise-driven attributes, real-life applications, and why it remains a trusted choice among industry leaders.
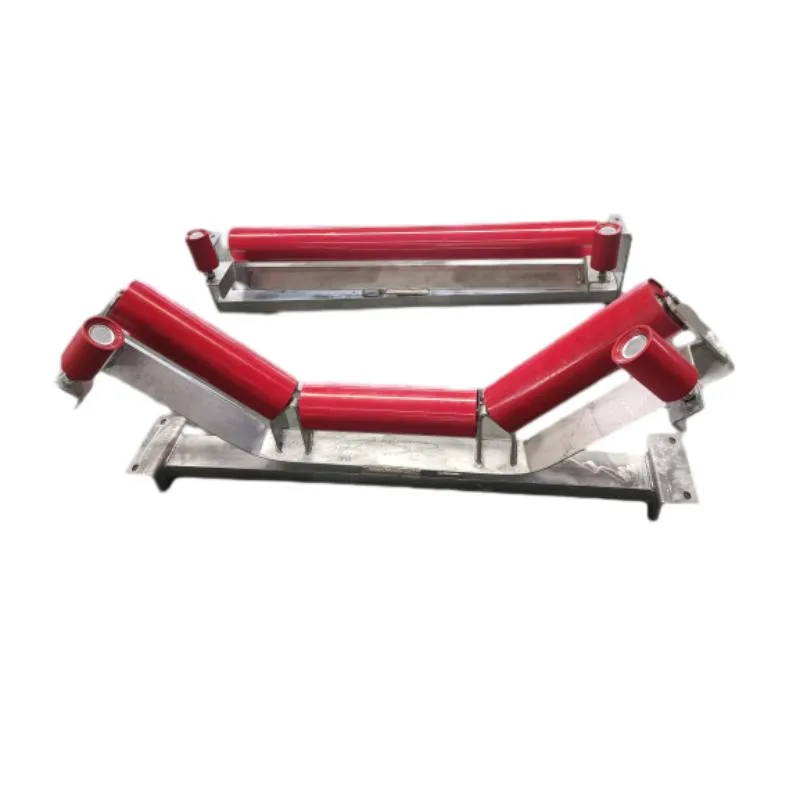
Industries ranging from mining to manufacturing consistently implement pulley systems at the core of their operations. However, the friction and wear-and-tear on these components, resulting from constant motion and heavy loads, can hamper productivity and increase maintenance costs. This is where pulley rubber lagging comes into play, offering practical solutions to these industrial challenges.
The application of rubber lagging on pulleys offers myriad benefits rooted in extensive industry expertise. It improves grip and traction, a critical need in conveyor systems transporting heavy materials. Enhanced traction reduces belt slippage, a common issue that can lead to unplanned downtimes and material wastage. Businesses employing rubber lagging experience a marked improvement in conveyor performance and, consequently, a reduction in operational disruptions.
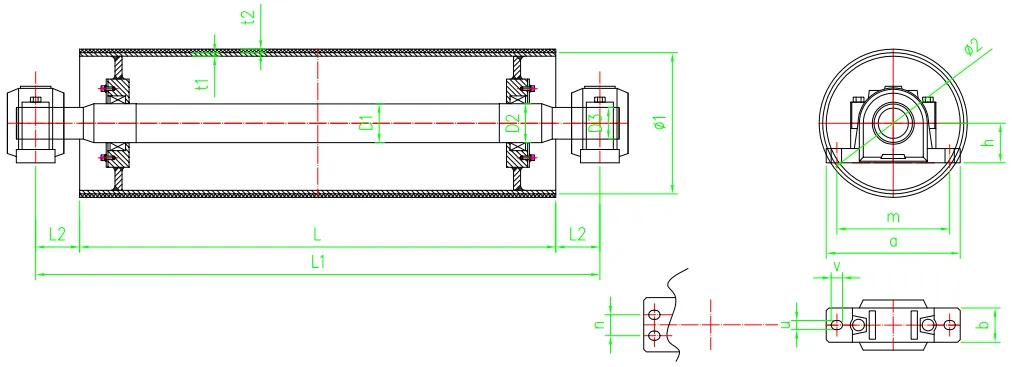
The durability of rubber lagging also reflects its expert engineering and material science development. Engineered to withstand harsh environmental conditions, including exposure to water, chemicals, and heat, rubber lagging minimizes direct contact between the pulley and belt. This protective barrier significantly reduces the wear and tear experienced by pulley systems, extending their service life and ensuring cost-effectiveness. It also contributes to a safer workplace by diminishing the likelihood of belt deviation or accidents caused by component failures.
pulley rubber lagging
Further adding to its expertise and authoritativeness is the customization potential of pulley rubber lagging. Manufacturers offer an array of rubber compounds and profiles tailored to specific operational needs. This flexibility allows companies to select lagging materials optimized for their unique environmental conditions and load requirements, ensuring peak performance across the board. Customization might include special additives to enhance oil resistance or UV protection for outdoor applications, underscoring the material's adaptability to varied industrial challenges.
Trustworthiness in pulley rubber lagging isn't just founded on its practical benefits but also its compliance with safety and environmental standards. High-quality rubber lagging is produced following stringent industry regulations and standards, ensuring that the materials used are safe for both the user and the environment. This commitment to safety and environmental stewardship enhances the trust users place in these products and assures continuous regulatory compliance.
Incorporating pulley rubber lagging reflects a forward-thinking approach to operational maintenance. Companies that prioritize investments in these materials often report lower maintenance expenses, reduced downtime, and improved overall system efficiency. Rubber lagging not only optimizes performance but also supports sustainable operations by decreasing the frequency of component replacements, thus reducing material waste.
In conclusion, pulley rubber lagging stands out as a prime example of industry expertise converging with practical innovation. Its ability to provide solutions underpinned by real-world experience and authority ensures that industries benefit from both improved operational reliability and financial savings. As businesses continue to seek sustainable, efficient, and reliable operational enhancements, pulley rubber lagging remains an invaluable asset, ready to meet and surpass the demanding expectations of industrial applications worldwide.