When it comes to optimizing the performance and longevity of conveyor systems, one cannot overlook the vital role played by pulley lagging. In an industrial setup, pulley lagging serves as a protective shield, ensuring smooth operation and alignment of belts, ultimately leading to improved efficiency and reduced maintenance costs. However, not all laggings are created equal. There are several variations tailored to meet specific industrial needs and conditions, making it essential to choose the right type to maximize your conveyor system's performance.
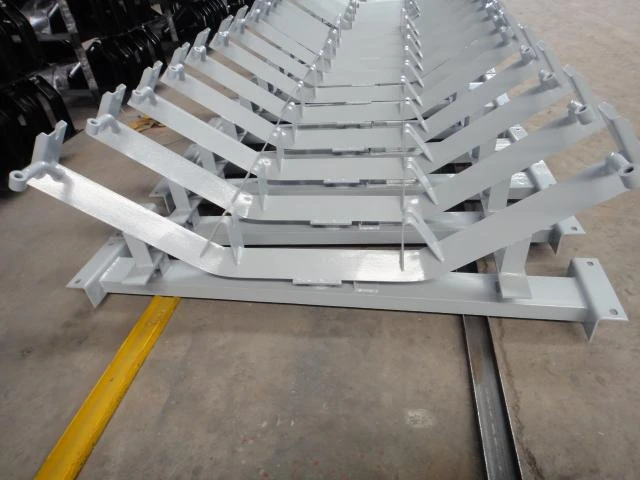
For businesses aiming to optimize conveyor functionality, understanding different types of pulley laggings is critical. The main types include rubber lagging, ceramic lagging, diamond grooved, and strip lagging, each offering unique advantages suited to different operational conditions.
Rubber lagging, often seen as the standard solution, is prized for its versatility and cost-effectiveness. It comes in natural or synthetic variants, offering good friction and wear resistance, making it suitable for a wide range of applications. It is particularly beneficial in industries where the conveyor system is exposed to moderate environmental conditions and where initial costs are a significant consideration.
Rubber lagging can come smooth or grooved. The grooved variations help dissipate water and contaminants, offering improved traction. It’s a reliable choice for most general conveyor pulley applications.
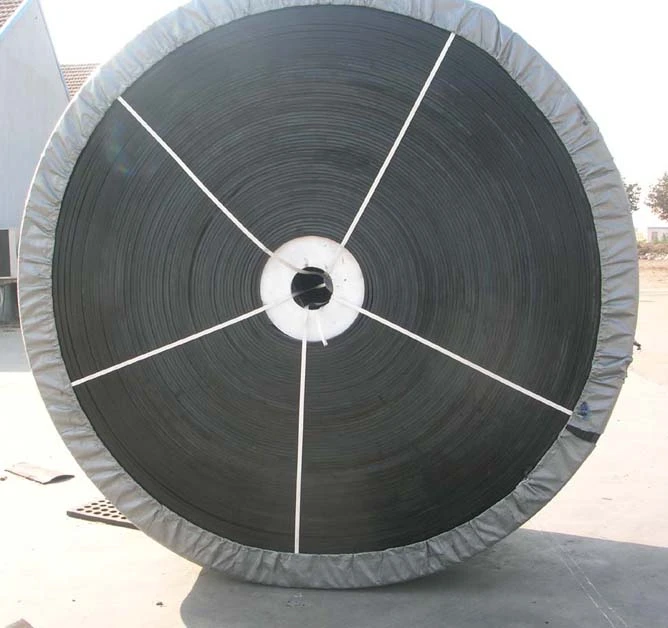
For harsher environments, such as those involving heavy loads, extreme climates, or materials that create intense wear, ceramic lagging may be a superior choice. Composed of ceramic tiles embedded into a rubber matrix, this type of lagging offers remarkable wear resistance and grip. The ceramic tiles create a high-friction interface, reducing slippage and improving the overall energy efficiency of the conveyor system. This type of lagging is ideal for mining and other heavy-duty applications where durability and robust performance are priorities.
Diamond grooved lagging is another popular choice, recognized for its pattern, which enhances grip and traction. The diamond groove design effectively channels away water and debris, making it particularly effective in wet or muddy conditions. This design minimizes belt misalignment and slippage, making it a viable option for industries like agriculture, where the equipment operates under variable weather conditions and involves the movement of earth or agricultural products.
pulley lagging types
Strip lagging, a more customizable option, involves applying individual strips of lagging material across the pulley face. This type allows for customization in terms of thickness, spacing, and material to perfectly suit unique industrial needs. Its modular nature ensures that if a portion of the lagging wears down, only that strip needs replacement, potentially saving on maintenance costs and downtime. This adaptability makes strip lagging a cost-effective and practical choice for operations requiring frequent adjustments or replacements.
Choosing the right type of pulley lagging requires a comprehensive understanding of the specific operational conditions and challenges. Environmental factors, material types, load weights, and even the speed of the conveyor system can influence this decision. Consulting with experts who have hands-on experience and technical knowledge can provide insights into which type will yield the best results for your specific application.
Incorporating the suitable pulley lagging type not only extends the longevity of the conveyor system but also enhances its performance, thereby improving the operational efficiency and profitability of the business. While initial costs might vary, investing in the appropriate lagging can lead to substantial long-term savings by minimizing maintenance needs and downtime.
In conclusion, pulley lagging is a critical component that significantly impacts the effectiveness of conveyor systems. Businesses that take the time to select the appropriate lagging type, considering their unique environmental and operational challenges, are more likely to enjoy a seamless, efficient, and cost-effective conveyor operation. Leveraging professional expertise ensures that this selection aligns with industrial demands, facilitating not only operational efficiency but also contributing to the trustworthiness and authority of a business in its respective field.