Lagging rubber, a term often associated with industrial applications, plays a significant role in enhancing the efficiency and longevity of machinery. Understanding its importance involves delving into its practical applications, benefits, and expert recommendations.
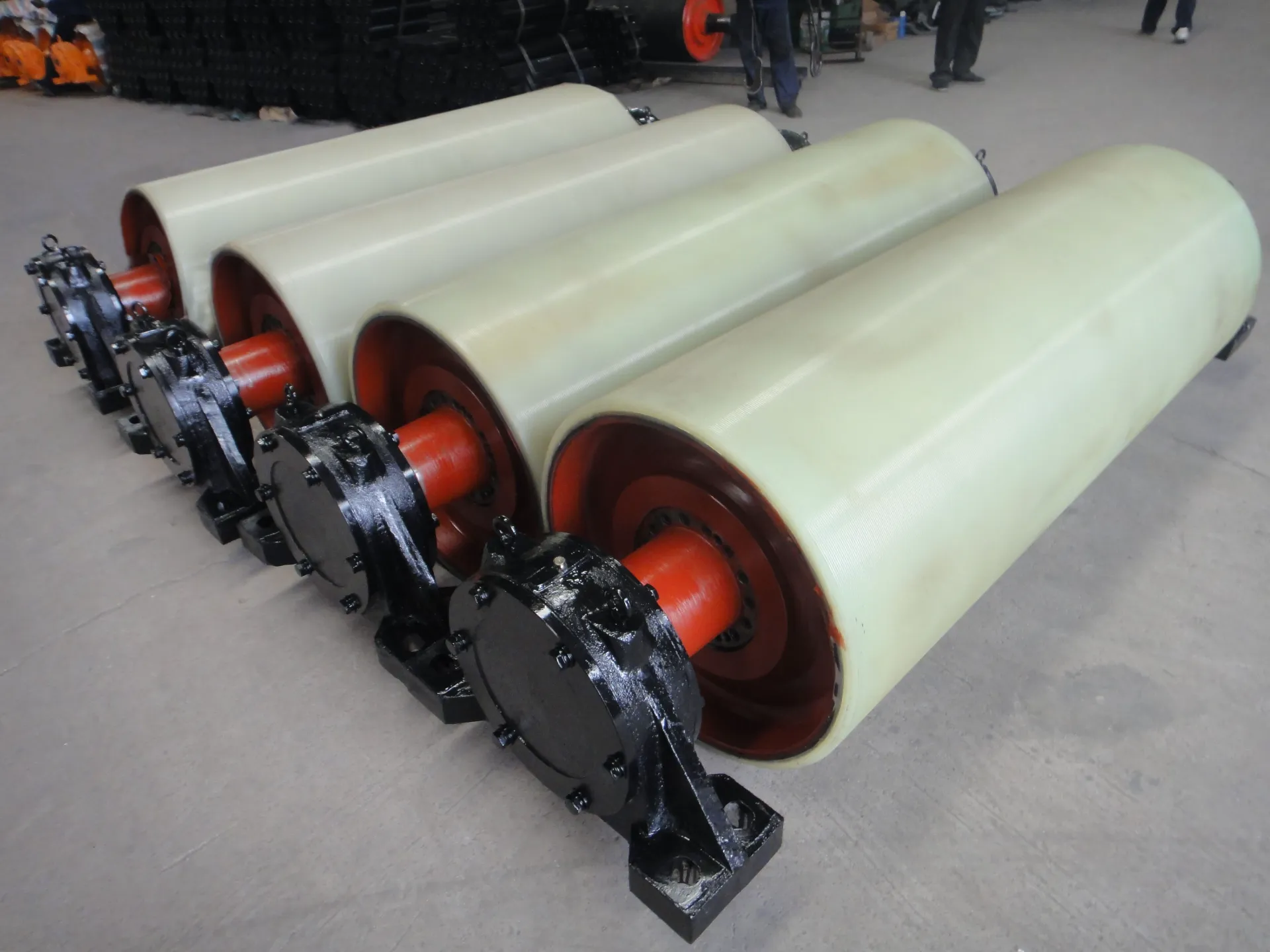
Rubber lagging serves as a protective cover for conveyor pulleys and other machinery components. It is crucial for minimizing slippage, improving traction, and ensuring the smooth operation of industrial tools. Its application can be observed across several industries, including mining, manufacturing, and logistics, where conveyor systems form the backbone of operations. Slippage in these systems can lead to downtime, increased wear and tear, and considerable maintenance costs. Lagging rubber, therefore, is not just a material, but a solution for efficiency and cost-reduction.
From an expert's perspective, the type of rubber used for lagging is critical. Natural rubber, known for its elasticity and abrasion resistance, is commonly utilized. However, other variants like neoprene and silicone offer specialized benefits such as resistance to oils, extreme temperatures, and environmental conditions. The selection of the appropriate type of rubber should be based on environmental conditions and the specific industrial application. For instance, in a mining context where machinery is exposed to harsh surroundings, abrasion-resistant rubber lagging is advisable.
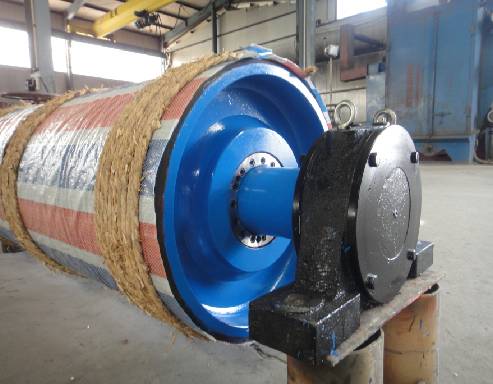
The application process of rubber lagging itself demands precision. Misapplication can lead to uneven wear, reduced efficiency, and potential damage to equipment. Experts suggest a few key considerations for effective rubber lagging application. The surface must be adequately prepared, often requiring cleaning and priming. Applying adhesives requires precision to ensure a uniform bond, and curing times must be strictly adhered to, in alignment with manufacturer specifications.
The introduction of modern technologies has advanced the production and application of lagging rubber. Automated machinery and laser-guided alignment systems have improved the precision and effectiveness of application, enhancing overall longevity and performance. In addition, the development of multi-layered rubber sheets and custom-molded rubber lagging provides tailored solutions capable of handling the specific needs of diverse industrial environments.
lagging rubber
Authoritativeness in choosing rubber lagging solutions is marked by the understanding of both the product’s capabilities and the industrial demands. Trusted providers in the market offer consultation services, aiding industries in selecting the most appropriate rubber compounds and application techniques. Their expertise ensures the reliable and efficient integration of rubber lagging into existing systems, resulting in performance optimization.
Real-world experience with rubber lagging demonstrates significant performance improvements. Several case studies highlight reduced operational downtimes and maintenance expenditures. One notable instance is a logistics company that adopted advanced rubber lagging solutions and reported over a 20% increase in operational efficiency, decreased maintenance frequency, and an extended lifespan for their conveyor systems. This is a testament to the product’s capability in transforming industry operations.
To ensure trustworthiness in this realm, industry professionals should seek materials and services from established and reputable sources. Quality certifications such as ISO and compliance with industrial safety standards are indicators of reliability. Moreover, ongoing training and updates on the latest rubber lagging technologies and methods will solidify operational trust and performance enhancement.
In conclusion, the application of lagging rubber is not merely a technical addition but a strategic investment for industries relying on conveyor systems. By carefully selecting materials, adhering to expert application practices, and staying informed of technological advancements, businesses can gain substantial benefits, enhancing their operational performance and extending the longevity of their machinery. The intricate balance of experience, expertise, authoritativeness, and trustworthiness shapes the success of rubber lagging applications.